Slotted Bases
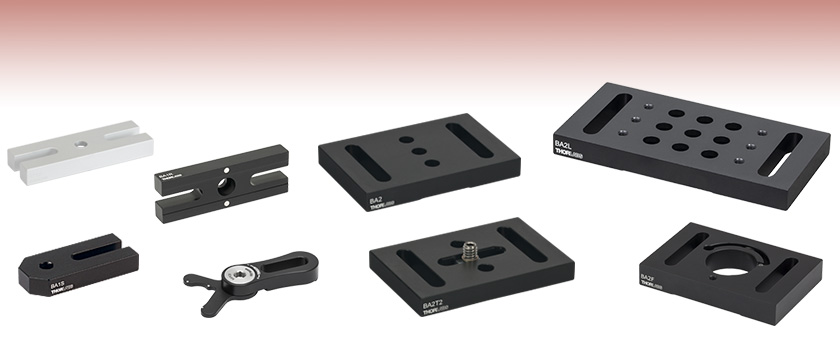
- Compatible with Imperial or Metric Posts and Post Holders
- Available with Imperial or Metric Footprint
- Bottom Relief Cuts Ensure Stable Mounting
BA1V
Vacuum Compatible
BA2
BA1S
RSPCS
Swiveling Position Retainer
BA2F
Flexure Clamping Mechanism
BA2T2
Adjustable Base
BA2L
Base with 6-32 and 8-32 Taps
BA1R
Magnetic Base
(Underside Shown)

Please Wait
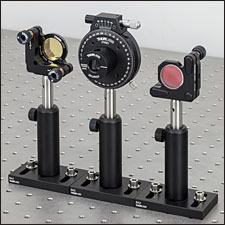
Click to Enlarge Figure 1.1 Components Mounted on BA2 Bases
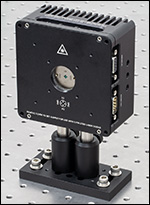
Click to Enlarge
Figure 1.3 LDM90 Laser Diode Mount on a BA2L Base
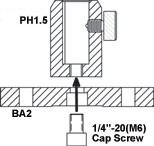
Figure 1.2 Post Holder and Base Assembly
Features
- Ideal for Mounting and Positioning Our Ø1/2" Post Holders
- Machined Bottom Relief Cuts Ensure Stability
- Vacuum-Compatible and Magnetic Versions of Popular Bases Available
- Imperial and Metric Footprints Available
The bases found on this page have a universal design that allows them to be used with imperial or metric components, such as post holders. However, it is best to use a metric base with a metric optical breadboard and an imperial base with an imperial breadboard. By matching metric with metric and imperial with imperial, the bases can be positioned flush against each other without leaving unused rows of holes, as shown in Figure 1.1. For more information on the differences between Thorlabs' imperial and metric components, please see our imperial vs. metric tutorial.
Standard Bases
These bases are most commonly used for positioning and fastening our Ø1/2" post holders to optical tables. Post holders are attached via 1/4"-20 (M6) cap screws placed through the bottom-located counterbores in the base, as shown in Figure 1.2. All bases are machined parallel and perpendicular to within 0.002" (0.05 mm) and contain bottom relief cuts that enhance stability.
Vacuum-Compatible Bases
These versions of our popular standard bases have a chemically cleaned finish instead of the standard black anodization. This allows them to be used directly out of the packaging at pressures as low as 10-6 Torr, or at even lower pressures with additional cleaning and processing. To complement these bases, we offer a complete vacuum-compatible Ø1/2" post system, as well as a selection of vacuum-compatible components.
Bases with Tapped Mounting Holes
These bases provide a larger mounting surface than our standard bases and have an array of counterbored and tapped mounting holes. These features make it possible to accommodate larger components, such as the LDM90 shown in Figure 1.3, or a small optical system. 6-32 (M4) tapped holes make these bases compatible with our clamping arms for mounting large beamsplitter cubes and prisms. Bases with 8-32 and 1/4"-20 (M6) tapped holes offer additional mounting options.
Bases with Holes for Alignment Pins
These anodized aluminum bases feature four holes for alignment pins around each counterbored or threaded mounting hole. Thorlabs' offers the BA2A1(/M) with #8 (M4) counterbores, the BA2A2(/M) with 1/4" (M6) counterbores, and the BA2A3(/M) with 8-32 (M4 x 0.7) tapped holes.
Magnetic Bases
When working on a magnetic optical table, the bottom-located magnets in our BA1R(/M), BA1SR(/M), and BA2R(/M) bases provide the ability to temporarily secure components during the setup process. The magnets in these bases are strong enough to help prevent accidental movement of components, while still allowing for easy repositioning. Once positioning is complete, these bases must be screwed down to be permanently secured to the table.
Adjustable Bases
The BA2T2(/M) Adjustable Base complements our popular line of standard bases. Designed for greater flexibility, this base features three long slots and two 1/4"-20 (M6) counterbored holes. A 1/4"-20 (M6) threaded stud (included) can slide along the central slot for coarse alignment adjustments. This base is ideal for use with our Ø1/2" post holders.
Flexure Bases
The BA2E(/M) and BA2F(/M) Flexure Mounting Bases feature a double bore for mounting Ø1/2" (Ø12.7 mm) posts or Ø1/2" post holders and Ø1" (Ø25.0 mm) posts, respectively, with a non-marring flexure clamping mechanism. In addition to providing rotational and some height adjustment, these bases also allow a post to be mounted in direct contact to the optical table surface because of the double bore through the part. With standard bases, such as the BA2, the post is mounted on top of the base directly or within a post holder. This method will inherently increase the minimum height of the optical axis. The double bore flexure design mounts optical components within the base to provide more stability and allow the components to be closer to the optical table surface. It also removes the need to use intermediary parts, such as a post holder, when mounting a post.
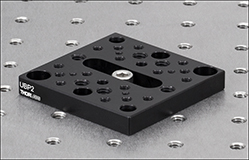
Click to Enlarge
Figure 1.4 UBP2 Universal Base Plate
In addition to the advantages stated above, using these bases to directly mount a post will also remove the issue of table flexing, or bridging, that is commonly seen when using standard clamping forks. Please click here for more information on the detrimental effects of table flexing.
Universal Base Plates
These base plates increase the flexibility of any optical setup by providing mounting holes in virtually any orientation on an optical table or breadboard. This freedom allows users to mount various components or stages in a wide array of orientations outside of what is dictated by the standard 1" (25.0 mm) hole pattern, as shown in Figure 1.4.
Rotation Baseplate
This baseplate is desgined for use with our fixed optic mounts for OEM applications. Four 1/4"-20 (M6 x 1.0) tapped mounting holes on the surface provide mounting options. A curved clearance slot and included dowel pin adapter provide up to 90° of rotation without moving the mounting cap screw.
Swivel Base Adapter
Our 360° swivel base adapter fits all standard Ø1/2" post holders with 1/4"-20 (M6) mounting holes. The swivel design is ideal for applications that require a large number of components to be packed into a small area. Additionally, the swivel base will decrease the time required to assemble an optical system.
Base Position Retainers
Thorlabs' Position Retainers can be used to realign bases and other squared-off components that have been removed from an optical system. They act as markers on the breadboard or optical table in the event that you need to remove a component from your setup.
Image (Click to Enlarge) |
Description |
---|---|
![]() BE1 |
Base Adapter for Ø1/2" Post Holders and Ø1" Posts The BE1 Pedestal Base Adapter features a 1/4"-20 (M6)-threaded stud which fits into the bottom of our standard Ø1/2" post holders or Ø1" post extensions to convert them into pedestal-style mounts. Made from solid 303 stainless steel with a 1.25" (31.8 mm) outer diameter, this adapter allows these posts to be used with our CF125 and CF175 clamping forks. |
![]() RS05PC |
Ø1" Ceramic Pedestal Pillar Post The RS05PC Ceramic Pedestal Post is designed to provide high levels of thermal and electrical isolation. It is ideal for mounting components that may be sensitive to heat or sources of electrical noise. This adapter is compatible with our CF125 and CF175 clamping forks. |
![]() CF125 |
Small Clamping Fork The CF125 Clamping Fork was designed with positional flexibility in mind. This clamping fork is directly compatible with our Pedestal Style Post Holders and RSP-Series Ø1" Pedestal Pillar Posts. The solid steel construction, complete with carefully placed relief cuts and landing pads, provides exceptional clamping stability. The counterbored slot is 1.25" (32 mm) in length, is designed to accept a 1/4"-20 (M6) cap screw and washer, and allows the clamp to swivel about the pedestal base in order to align with the most convenient mounting holes. |
![]() CF175 |
Large Clamping Fork The CF175 Clamping Fork was designed with positional flexibility in mind. This clamping fork is directly compatible with our Pedestal Style Post Holders and RSP-Series Ø1" Pedestal Pillar Posts. The solid steel construction, complete with carefully placed relief cuts and landing pads, provides exceptional clamping stability. The counterbored slot is 1.75" (44.4 mm) in length, is designed to accept a 1/4"-20 (M6) cap screw and washer, and allows the clamp to swivel about the pedestal base in order to align with the most convenient mounting holes. |
![]() POLARIS-CA1 |
Polaris™ Non-Bridging Clamping Arm The Polaris Clamping Arm is the ideal solution for stably mounting any Ø1" post. Each clamping arm, which is constructed from heat-treated, stress-relieved 303 stainless steel, provides extremely high holding forces with minimal torquing of the mounting screws. The side-located clamping mechanism is actuated using a 1/4"-20 cap screw. Because the side-located clamp and mounting slot are tightened separately, the user can set the position of the fork and adjust the rotational alignment independently. The clamping arm has a compact 3.33" x 1.60" (84.5 mm x 40.6 mm) footprint for tight laser cavity setups, with a thickness of 0.60" (15.2 mm) for increased stability. A 1.30" (33.0 mm) long clearance slot allows for a variety of mounting solutions using a 1/4"-20 or M6 cap screw and washer. This clamping arm is also avaiable with a metric cap screw (POLARIS-CA1/M). |
![]() PB4 |
Base Adapter for Ø1" Post Holders and Ø1.5" Posts The PB4 pedestal base adapter features a 1/4"-20 (M6)-threaded stud which fits into the bottom of our Ø1.5" posts to convert them into pedestal-style mounts. Made from solid 303 stainless steel with a 1.85" (47.0 mm) outer diameter, this adapter allows these posts to be used with our PF85B, PF125B, or PF175 clamping forks. |
![]() PB4R |
Magnetic Base Adapter for Ø1" Post Holders and Ø1.5" Posts The PB4R pedestal base adapter features a 1/4"-20 (M6)-threaded stud which fits into the bottom of our Ø1.5" posts to convert them into pedestal-style mounts. Made from solid 303 stainless steel with a 1.85" (47.0 mm) outer diameter, this adapter allows these posts to be used with our PF85B, PF125B, or PF175 clamping fork. There are four high strength magnets in the base that are sufficiently strong to securely hold the base in place on an optical table. |
![]() PF85B |
Compact P-Series Clamping Fork The PF85B is specifically designed to secure our Ø1" Post Holders or our PB4 pedestal base adapters. It has a 0.85" (21.6 mm) long counterbored slot that is designed to accept a 1/4"-20 (M6) cap screw and washer. The clamp can swivel about the pedestal base in order to align with the most convenient mounting holes. |
![]() PF125B |
Small P-Series Clamping Fork The PF125B is specifically designed to secure our Ø1" Post Holders or our PB4 pedestal base adapters. It has a 1.25" (31.8 mm) long counterbored slot that is designed to accept a 1/4"-20 (M6) cap screw and washer. The clamp can swivel about the pedestal base in order to align with the most convenient mounting holes. |
![]() PF175B |
Large P-Series Clamping Fork The PF175B is specifically designed to secure our Ø1" Post Holders or our PB4 pedestal base adapters. It has a 2.12" (53.8 mm) long counterbored slot that is designed to accept a 1/4"-20 (M6) cap screw and washer. The clamp can swivel about the pedestal base in order to align with the most convenient mounting holes. |
![]() PB1 |
Mounting Post Base for Ø1.5" Posts This standard Ø2.48" post base bolts directly onto P-Series posts and adds 0.40" to the height of the post. To mount directly onto an optical bench, four 1/4 (M6) counterbored holes on 2" (50 mm) centers are provided. |
![]() PB2 |
Slotted Mounting Post Base for Ø1.5" Posts This universal Ø2.40" post base allows random placement of a P-Series post on an optical bench. The PB2 attaches to the P-Series posts using the 1/4"-20 (M6) center-tapped hole and adds 0.50" to the height of the post. |
![]() KB1X1 |
1" x 1" Kinematic Base This kinematic base consists of two plates: a top mounting plate and a bottom base plate. The two plates measure 1" (25 mm) to a side and are magnetically coupled using two pairs of high strength magnets. The top plate can be removed and replaced, automatically repositioning to an exact location with the repeatability of one microradian. The bottom plate can be fastened using a center-located #8 (M4) counterbore. Both the top (Item# KBT1X1) and bottom (Item# KBB1X1) plates can be purchased separately. |
![]() KB3X3 |
3" x 3" Kinematic Base This kinematic base consists of two plates: a top mounting plate and a bottom base plate. The two plates measure 3" (75 mm) to a side and are magnetically coupled using two pairs of high strength magnets. The bottom plate can be fastened to an optical bench using two 1/4"-20 (M6) clearance slots. These mounting slots can be accessed with the top plate in place. Both the top (Item# KBT3X3) and bottom (Item# KBB3X3) plates can be purchased separately. |
![]() KBM1 |
Lockable Kinematic Breaboard (3.94" x 3.94") This kinematic base consists of two plates: a top mounting plate and a bottom base plate. The two plates measure 3.94" (100 mm) to a side and are magnetically coupled using two pairs of high strength magnets. With a ball and V-groove design, the top plate can be removed and replaced with a lateral repeatability of 30 µm. The high repeatability of the unit allows minimal readjustment of the setup for applications where frequent removal and insertion of components is needed. The top plate has an array of 39 1/4"-20 (M6) tapped holes [0.46" (11.8 mm) deep] spaced 0.5" (12.5 mm) apart and provides the same mounting functionality as an optical breadboard. The bottom plate has two 2.00" (50.0 mm) long counterbored slots for 1/4"-20 (M6) cap screws for mounting to an optical table. |
![]() RB2 |
Adjustable Height Post Base The RB2 has a 0.90" (23 mm) deep base, which allows for maximum height adjustment of the RS Series of pillar posts. The locking screw is located on the top surface of the base, allowing for convenient vertical access. |
![]() MB175 |
Magnetic Base For use with our standard Ø1/2" stainless steel post or our Ø1" post holders, this heavy-duty magnetic base has a switchable magnet for quick positioning of optical components. It provides 175 pounds of holding force. The two bottom mounting surfaces have been precision ground for optical bench applications. |
![]() IB3 |
Instrument Base The IB3 precision-machined aluminum instrument base provides flat, stable mounting and is useful for maneuvering items such as a post-mounted power meter head into and out of the beam path. |
![]() PMB3 |
Permanent Magnetic Base The PMB3 combines the convenience of our IB3 Base (above) with the benefit of a powerful magnet. The magnet is sufficiently strong to hold the base in place securely without needing to clamp it to an optical table. These bases are ideal for semi-permanent placement of an instrument or optical head. |
![]() SB1 |
Switchable Kinematic Base This compact kinematic base is designed to allow easy removal and exact repositioning of the top plate. An On/Off switch controls the magnetic force that firmly holds the two plates together. Additional top (Item# SB1T) and bottom (Item# SB1B) plates can be purchased separately. |
![]() NX1NF |
Indexing Mounting Base This base is ideal for redirecting a laser to multiple targets on your optical table. Applications include precise switching of shared laser systems, directing optical signals to multiple test instruments, and easy exchange of optical components (with extra top mounts). For best performance, ensure that the NX1NF is securely attached to its support structure. A series of three #8-32 (M4-0.7) tapped mounting holes are provided for mounting the bottom plate to a post or breadboard and the top plate has a single 8-32 tap for mounting optical components. |
![]() NX1F ESK01 |
Bases and Post Holders Essentials Kit For those who are just starting out and need a little bit of everything, the ESK01 Bases and Post Holders Essentials Kit contains 130 of the most commonly used post holders, bases, and table clamps, all conveniently housed in a completely labeled cabinet. The large variety of sizes provides the maximum amount of flexibility when breadboarding an optical system. This kit is best used in conjunction with ESK03 Post and Accessories Essentials Kit. |
Insights into Best Lab Practices
Scroll down to read about a few things we consider when setting up lab equipment.
- Washers: Using Them with Optomech
- Bases: For Stability Orient the Side with the Undercut Down
Click here for more insights into lab practices and equipment.
Washers: Using Them with Optomech
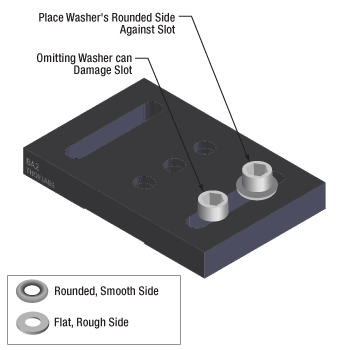
Click to Enlarge
Figure 174B Install washers before inserting bolts into slots to protect the slot from damage. The rounded, smooth side of the washer should be placed against the slot, and the rough, flat side should be in contact with the bolt head. The smooth surface is designed to translate easily across the anodized surface, without harming it. The BA2 base is illustrated.
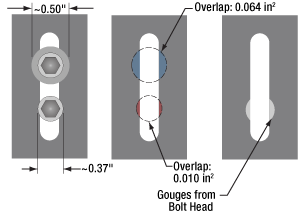
Click to Enlarge
Figure 174A The diameter of the washer is 35% larger than that of the bolt head. This results in over a six fold increase in overlap area with the slot of a BA2 base. By distributing the force of the bolt over a larger area, the washer help prevent gouging of the slot.
The head of a standard cap screw is not much larger than the major diameter of the thread (Figure 174A). For example, a 1/4"-20 screw has a head diameter between 0.365" and 0.375" and the clearance hole diameter for the threads is 0.264".
When the screw is tightened directly through the clearance hole to secure the device, the force is applied to the edge of the through hole, often cutting into the material (Figure 174A).
Once the material is permanently deformed, the screw head will want to fall back into the gouged groove, thereby moving the device back to that location when attempting to make fine adjustments.
A device with a circular through hole is not meant to translate around the screw thread so the deformation is not expected to be a problem.
However, a slot should provide the ability to secure the device anywhere along the length for the lifetime of the part. Using a washer distributes the force away from the slot edge to decrease the chance of deforming the slot and extending the lifetime of the part. Figure 174A illustrates the difference a washer can make. The contact area between the slot of a BA2 base and a 0.27" diameter cap screw is 0.010 in2. When a 0.5" diameter washer is used the contact area is 0.064 in2, which is over six times larger.
When using a Thorlabs washer, there are two distinct sides (Figure 174B). One side is flat and rough and the other is curved and polished. The curved and polished side should be placed against the device, which has an anodized surface.
As the screw tightens, the screw head can force the washer to spin against the anodized coating.
If the flat side is pressed down against the anodization, the friction created by the rough flat side can scratch the anodized aluminum. However, if the curved side is facing down, the smooth surface has less friction leading to less scratches and extending the visual appearance of the device.
Date of Last Edit: Dec. 4, 2019
Bases: For Stability Orient the Side with the Undercut Down
An undercut is machined into the bottom surface of bases like the BA2 (Figures 174C and 174D). The undercut creates feet, which are called pads. For maximum stability, the base should be oriented with its pads in contact with the table or breadboard.
The top surface of the base does not have an undercut and is the intended mounting surface for components.
Mounting the base upside down could result in the base rocking on the table or breadboard, or the base may exhibit other mechanical instability.
The Pads are Flatter than the Top Surface
The undercut is key to the flatness of the pads. The pads are machined flat after the undercut is made.
Friction heats the pads during the processing step that provides them with a maximally flat profile. By reducing the surface area of the pads, the undercut reduces the amount of heat generated during this step.
It is beneficial to minimize the heat generated during machining. Metal expands when heated, and the uneven heating that occurs during machining can distort the dimensions of the part. If the dimensions of the part are distorted during machining, the part can be left with high spots and other undesirable features after it cools. This can cause instability and misalignment when using the part.
Precision Instruments and Devices have Pads
Another example of a component with pads is the LX10 linear stage shown in Figure 174E.
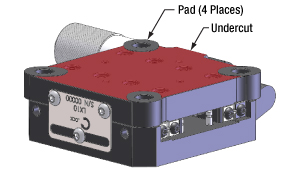
Click to Enlarge
Figure 174E Pads machined into Thorlabs' devices improve their stability when bolted in place. The pads are highly flat and project above the undercut region, which is highlighted red. The undercut limits the contact area with the table or breadboard.
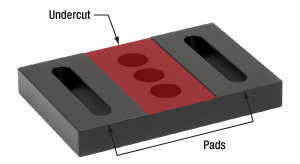
Click to Enlarge
Figure 174D This view of the bottom shows the undercut highlighted in red. By removing this material, the pads can be made maximally flat.
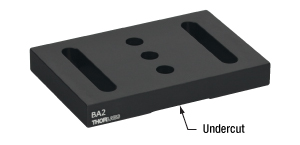
Click to Enlarge
Figure 174C For optimal stability, the base should be mounted with the undercut facing the optical table or breadboard.
Date of Last Edit: Dec. 9, 2019
Posted Comments: | |
Jonathan Sager
 (posted 2024-01-03 13:30:47.053) Do these use standard 7/16” square nuts? jpolaris
 (posted 2024-01-04 03:32:44.0) Thank you for contacting Thorlabs. Yes, the nut in BA2T2 is a 1/4"-20 tapped, 7/16" width, 3/16" height square nut. li yancheng
 (posted 2022-06-29 15:01:54.683) what is the material of the black oil paint? jdelia
 (posted 2022-06-29 01:22:19.0) Thank you for contacting Thorlabs. We do not use black oil paint on our slotted bases. The black color comes from our Type-II sulfuric acid anodization layer of the aluminum. jooeonoh
 (posted 2017-05-17 14:50:11.227) While I used this product for my experiment, I have a question.
For my temperature measurement, I wonder this product is made from what. Is it ok to increase the temperature around 400 degrees with attached TEC(thoralab_model#_HT24S)? tfrisch
 (posted 2017-05-19 04:17:01.0) Hello, thank you for contacting Thorlabs. I will reach out to you directly about this resistive ceramic heater. franxm
 (posted 2013-04-29 15:47:06.363) suggestion: laser etched ruler on bottom edge of BA1S (and BA1SR) along 2.3" length. application: mount with iris to align beam (parallel to table edges) using table holes jlow
 (posted 2013-04-30 12:42:00.0) Response from Jeremy at Thorlabs: Thank you very much for your feedback. We will look into the possibility of adding this to our bases. In the meantime, we should be able to provide you with a custom solution for this. I will get in contact with you directly to discuss about this. bdada
 (posted 2012-02-02 19:02:00.0) Response from Buki at Thorlabs:
Thank you for using our product feedback tool. The material used for the BA2T2/M is anodized aluminum, which is non magnetic. We will look into adding more information on our website. Please contact TechSupport@thorlabs.com if you have any questions. user
 (posted 2012-02-02 17:16:28.0) Could you tell me what materials are used in these bases? We have an application for which we need non-magnetic parts. Could you suggest another product that allows translational flexibility if these wouldn't work? Thanks. bdada
 (posted 2012-01-23 08:57:00.0) Response from Buki at Thorlabs:
Thank you for pointing out the omission of the UPHA swivel base. We have added it to the page. user
 (posted 2012-01-22 15:57:20.0) The UPHA swivel base is missing from your page on bases. technicalmarketing
 (posted 2007-11-13 16:12:16.0) In response to acable’s suggestions we have implemented the following changes to this page:
(1) We have retaken the photograph of the BA2T2 to show the locking screw in the center slot
(2) We have also enlarged the application photo so that the magnets can be more easily viewed
(3) We have added an “other bases” tab, which highlights the other base options that Thorlabs offers. In addition, this tab contains links to all of the products so that more information can be found.
(4) We have presented the bases in numerical order in the price box
(5) We have shuffled the photos in the first subgroup image so that they could be enlarged.
(6) We have fixed the broken link under the related products tab.
We are still in the process of implementing some of the ideas from your first post (in terms of creating a circle of visibility) but wanted to comment on the current progress. We thank you for your interest in Thorlabs, and your willingness to help us improve our web presentations! acable
 (posted 2007-10-11 09:40:03.0) The BA2T2 photo doesnt show the locking screw that is fixed within the center slot but instead has it in one of the auxillary mounting holes. Also the application photo which is what i used to understand the operation of the part is really small and hard to read, and there seems to be plenty of room to enlarge it.
Also please have a look at the old comment from May of 2006, most are still not acted on. |

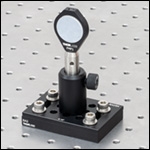
Click to Enlarge Figure G1.2 The height of any component mounted on a BA2(/M) base can be increased in increments from 0.010" (0.25 mm) to 2" (50 mm) using a mounting base spacer.
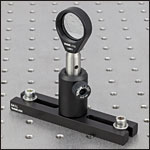
Click to Enlarge Figure G1.1 Post Holder with Lens Mounted on BA1L Base
- Compatible with Imperial and Metric Breadboards, Posts, and Post Holders
- Attach to Post Holders via Bottom-Located 1/4"-20 (M6) Counterbored Mounting Hole(s)
- Mount on Breadboard or Optical Table via Clearance Slot(s) for 1/4"-20 (M6) Cap Screws
- Fabricated from Black Anodized Aluminum with Bottom Relief Cuts for Stable Mounting
- Our Most Popular Bases are Also Available in Packs of 5
Thorlabs offers a variety of standard anodized aluminum bases to best utilize space on an optical breadboard. For close positioning of components, our BA1S(/M) base features the smallest footprint, while the BA1SL(/M) base offers a longer slot length for flexibility. For increased stability while maintaining a small footprint, the two-slotted BA1(/M) is a good option. For the greatest stability, consider our BA2(/M) and BA3(/M) bases, which offer a larger contact area. The BA2(/M) features two straight slots, while the BA3(/M) has two radial slots for 90° of manual rotation. As our longest standard base, the BA1L(/M) provides 1.44" (36.6 mm) of lateral positioning and can be secured to an optical breadboard by two screws, even when oriented at varying angles with respect to the tapped hole pattern (see Figure G1.1).
Please note that a 3/8" long, 1/4"-20 (10 mm long, M6) cap screw is recommended for attaching post holders to our standard mounting bases.
To reduce packaging waste, we offer our most popular sizes in packs of five.

- Vacuum-Compatible Design (>10-6 Torr)
- Double Vacuum Bagged for Cleanroom Environments
- Same Stability and Footprint as Our Standard Mounting Bases Sold Above
These vacuum-compatible bases are constructed from 6061-T6 aluminum and are chemically cleaned and prepared for vacuum applications before packaging. They are compatible directly out of the packaging with vacuum environments down to 10-6 Torr. With additional cleaning and processing, they can be used at even lower pressures, only limited by the outgassing rate of the aluminum. The material properties of the 6061-T6 aluminum and the cleaning methods that are completed by the end user should be used to determine the appropriateness of these products and materials in a specific vacuum system operating at pressures under 10-6 Torr.
These bases are packaged in double airtight bags for cleanroom and vacuum chamber applications. A 3/8" (10 mm) long 1/4"-20 (M6) vented cap screw (SH25S038V or SH6MS10V, respectively) is recommended for attaching post holders to our mounting bases. We also offer additional vacuum-compatible Ø1/2" post system components.

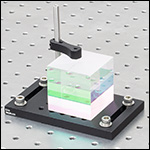
Click to Enlarge Figure G3.1 2" Beamsplitter Cube Mounted on BA4 Mounting Base Using a PM4 Clamping Arm
- Compatible with Imperial and Metric Breadboards, Posts, and Post Holders
- Nine 1/4" (M6) Counterbored Mounting Holes
- 6-32 (M4) Taps for Use with Our Clamping Arms
- 1/4"-20 (M6) Taps on BA4(/M) for Mounting Optomechanical Components
- Clearance Slots for 1/4"-20 (M6) Cap Screws
- Fabricated from Black Anodized Aluminum with Bottom Relief Cuts for Stable Mounting
These mounting bases offer a larger mounting surface than our standard bases and an array of tapped and counterbored mounting holes. These features make it possible to mout larger components or small optical systems. Each base has nine counterbored mounting holes for 1/4"-20 (M6) cap screws. 6-32 (M4) taps compatible with our clamping arms allow these bases to be used as base plates for large prisms and beamsplitter cubes. The BA4(/M) also features ten 1/4"-20 (M6) taps for mounting optomechanics. The imperial versions of each size also have two 8-32 tapped holes for additional versatility.
Please note that a 3/8" long, 1/4"-20 (10 mm long, M6) cap screw is recommended for attaching post holders to these mounting bases.

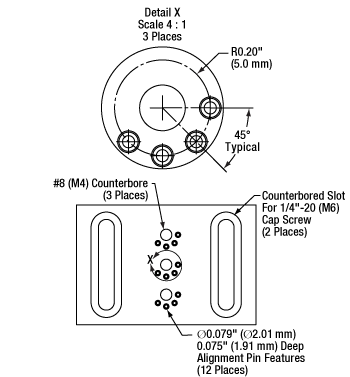
Click for Details
Figure G4.1 This diagram shows the BA2A1 Base with the mounting and alignment holes labeled. The BA2A1/M, BA2A2(/M), and BA2A3(/M) have the same arrangement of alignment pin holes around the mounting holes.
- Three Counterbored or Threaded Mounting Holes for Mounting Posts or Post Holders
- Four Holes for Ø2 mm Alignment Pins Around Each Mounting Hole (See Figure G4.1)
- Mount on a Breadboard or Optical Table via Counterbored Slots for 1/4"-20 (M6) Cap Screws
- Fabricated from Black Anodized Aluminum with Bottom Relief Cuts for Stable Mounting
These anodized aluminum bases feature four holes for Ø2 mm DIN-7m6 ground dowel pins (not included) around each counterbored or threaded mounting hole. The alignment pin holes are positioned on a circle with a 0.20" (5.0 mm) radius centered on each mounting hole and evenly spaced over a 135° angle (see Figure G4.1). These mounting bases feature two counterbored slots for 1/4"-20 (M6) screws, making them mountable on Thorlabs' breadboards and optical tables.

- Magnetic Versions of Our Most Popular Bases
- Holds Position of Components During Initial Setup Process
- Relief Cuts in Base Provide Excellent Stability
These anodized aluminum magnetic bases are modeled after our popular standard bases but are enhanced by bottom-mounted rare earth magnets, which provide the ability to temporarily secure components during the setup process. The force from these magnets is strong enough to help prevent accidental movement of components, while still allowing for easy repositioning. The full functionality of these bases can only be achieved when using them on a magnetic table or breadboard; however, they can function as a standard base on non-magnetic surfaces as well.
Each base attaches to a post holder via cap screws that fit within a bottom-located 1/4" (M6) counterbored hole. For final attachment to an optical breadboard, each base features at least one slot for a 1/4"-20 (M6) cap screw. Once positioning is complete, these bases must be screwed down to be permanently secured to the table. The BA1SR provides one 1.10" (27.9 mm) slot and allows for the smallest footprint. For increased stability while maintaining a small footprint, the BA1R provides two 0.81" (20.1 mm) slots. Finally, for the most support, the BA2R features two 1.25" (31.8 mm) slots. In addition, the BA2R comes with four bottom-located M3 counterbored holes for 34 mm rail mounting.

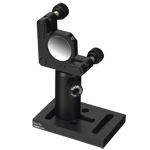
Click to Enlarge
- Two-Dimensional Adjustment of Components Without Removing Base from Breadboard
- Same Stability and Footprint as the BA2 Base
- Machined Bottom Relief Cuts Ensure Stability
The anodized aluminum BA2T2(/M) complements our popular line of standard mounting bases. It features a 1" (25.4 mm) long, counterbored slot along the center length that contains a 1/4"-20 (M6) threaded stud ideal for use with our Ø1/2" post holders. This slot provides for two-dimensional positioning of any attached optical component. To reposition a post holder on the base, loosen it by rotating it counter-clockwise, slide it into the desired position, and retighten it to the base. The base also contains two 1/4"-20 (M6) counterbored holes located on either side of the 1" long slot.
The BA2T2 is shown in Figure G6.1 with a Ø1/2" post holder, a Ø1/2" post, and a KM100 Ø1" mirror mount.

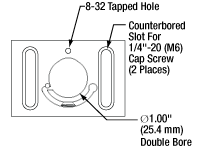
Click for Details
Figure G7.2 BA2F Base for Ø1" (Ø25.0 mm)
Posts Mechanical Drawing
(Click Here for the Metric BA2F/M Drawing)
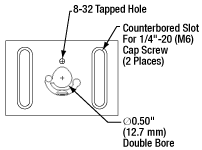
Click for Details
Figure G7.1 BA2E Base for Ø1/2" (Ø12.7 mm)
Posts Mechanical Drawing
(Click Here for the Metric BA2E/M Drawing)
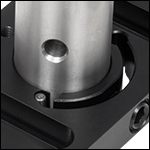
Click to Enlarge
Figure G7.3 Steel Insert Prevents Damage to Flexure Mechanism by Limiting Overall Travel
- Mounting Base with Double Bore Flexure Clamping Mechanism
- BA2E(/M): Ø1/2" (Ø12.7 mm) Double Bore
- BA2F(/M): Ø1" (Ø25.0 mm) Double Bore
- Mounts Ø1/2" (Ø12.7 mm) Posts, Ø1/2" Post Holders,
or Ø1" (Ø25.0 mm) Posts - Coarse Height and 360° Rotational Adjustment
- 8-32 (M4) Tapped Hole for Rotation Hard Stop with a Post Collar
- Machined Bottom Relief Cuts Ensure Stability
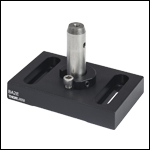
Click to Enlarge Figure G7.5 When Used with a Screw the 8-32 (M4) Tap Acts as a Rotational Stop
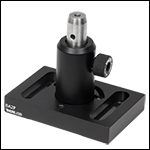
Click to Enlarge Figure G7.4 BA2F Holding a Ø1/2" post holder
These mounting bases contain a central double bore and non-marring flexure clamping mechanism that allows for the mounting of Ø1/2" (Ø12.7 mm) posts, Ø1/2" post holders, or Ø1" (Ø25.0 mm) posts. The flexure clamp is actuated by a side-located 3/8"-24 (M10 x 1.5) setscrew and 3/16" (5 mm) hex key. A permanent steel insert at the end of the flexing mechanism, shown in Figure G7.3, acts as a hard stop and prevents damage to the clamp from over tightening.
The double bore that goes through the part allows a post to be mounted within the base and in direct contact to the optical table surface. Standard bases have the post or post holder mounted directly on their surface which will inherently increase the minimum optical axis height and make the system less stable*. The method of mounting also removes the need for intermediary parts, such as a post holder, when mounting a post.
The height of the mounted post can be stably raised by 6.0 mm (0.24") within the Ø1/2" (Ø12.7 mm) double bore of the BA2E(/M) and by 7.0 mm (0.28") within the Ø1" (Ø25.0 mm) double bore of the BA2F(/M). The use of an R2 or R2T post collar with the BA2E(/M) or an RM1A or RM1B collar with the BA2F(/M) will create a hard stop for repeatable height adjustments. Each mount also contains an 8-32 (M4) tapped hole next to the double bore. With a cap screw or setscrew inserted into this hole, the post collars can also be used as a rotational stop, as shown for the BA2E in Figure G7.5.
Each base has two 1.25" (31.8 mm) long counterbored slots for 1/4"-20 (M6) cap screws for attachment to an optical table or breadboard. Please see Figure G7.1 and Figure G7.2 for details.
Please note that the flexure mechanism for the BA2F will contact the steel insert when mounting Ø1/2" post holders, since they are slightly smaller in diameter than Ø1" posts. This is normal operation and will not harm the mounting base.
If a Japanese post standard (Ø12.0 mm) needs to be used with the BA2E(/M), an AD12BA barrel adapter will be needed to bridge the 0.7 mm (0.03") gap between the post and flexure arm. The flexure arm will not be able to contact the smaller post diameter without this.
*A stability test was performed with a Ø1/2" (Ø12.7 mm) post mounted in a BA2E so that the post was in contact with the optical table. This was compared with a post mounted via a cap screw to our standard BA2 base. A 20 in-lb force was applied perpendicular to the post axis in both cases and the deflection of the post was recorded. Upon completion, the post within the BA2E had an overall deflection from center of about 0.001", while the post on the BA2 had a deflection from center of 0.002".

- Six Variants Offered with a Wide Variety of Mounting Options
- Central Counterbored Slot Allows for Rotation and Translation
- Models Available for 16 mm, 30 mm, and 60 mm Cage System Mounting
Our UBP Series Universal Base Plates increase the flexibility of any optical setup by providing mounting holes in virtually any orientation on an optical table or breadboard. This freedom allows users to mount various components or stages in a wide array of orientations outside of what is dictated by the standard 1" (25.0 mm) hole pattern. The counterbores in these plates also allow users to adapt metric components to an imperial optical table and vice versa.
Refer to Table 208A for specifications and detailed mounting options, including mechanical drawings. Each base plate has a counterbored slot in the center for mounting flexibility at any rotation, as well as counterbored holes at the corners for mounting to compatible breadboards. Cage system compatibility is offered via 4-40 tapped holes with the appropriate spacings.
Table 208A Detailed Mounting Options | ||||||
---|---|---|---|---|---|---|
Item # | Counterbored Slot Size |
Threaded Mounting Holes |
Counterbored Mounting Holes |
Cage Sytem Compatibility (via 4-40 Threaded Holes) |
Dimensions (W x L x H) | Mechanical Drawings |
UBP1 | #8 0.38" Long |
8-32 (10 Places) 4-40 (8 Places) |
#8 (6 Places) | 16 mm Cage Systems | 2.00" x 2.00" x 0.38" | ![]() |
UBP1/M | M4 8.8 mm Long |
M4 x 0.7 (10 Places) M3 x 0.5 (4 Places) 4-40 (4 Places) |
M4 (6 Places) | 50.0 mm x 50.0 mm x 9.5 mm | ![]() |
|
UBP2 | 1/4" 1.25" Long |
1/4"-20 (6 Places) 8-32 (16 Places) 4-40 (4 Places) |
1/4" (4 Places) #8 (4 Places) |
30 mm Cage Systems | 2.50" x 2.50" x 0.38" | ![]() |
UBP2/M | M6 31.8 mm Long |
M6 x 1.0 (6 Places) M4 x 0.7 (16 Places) 4-40 (4 Places) |
M6 (4 Places) M4 (4 Places) |
65.0 mm x 65.0 mm x 10.0 mm | ![]() |
|
UBP3 | 1/4" 1.25" Long |
1/4"-20 (24 Places) 8-32 (24 Places) 6-32 (6 Places) 4-40 (8 Places) |
1/4" (4 Places) #8 (4 Places) |
30 mm Cage Systems 60 mm Cage Systems |
3.50" x 3.50" x 0.38" | ![]() |
UBP3/M | M6 29.8 mm Long |
M6 x 1.0 (24 Places) M4 x 0.7 (30 Places) 4-40 (8 Places) |
M6 (4 Places) M4 (4 Places) |
90.0 mm x 90.0 mm x 10.0 mm | ![]() |
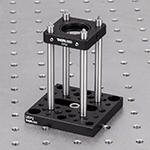
Click to Enlarge
Figure 208B The UBP2 plate can be used to vertically mount a 30 mm cage system and the centrally located slot allows mounting of components outside of the standard hole pattern.

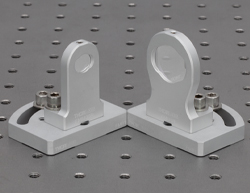
Click to Enlarge
Figure 788A Two Rear-Loading Mirror Mounts with Dichroic Mirrors Mounted on FMB1 Baseplates
- Attach Fixed Mirror Mounts via 1/4"-20 (M6 x 1.0) Tapped Holes
- Included Dowel Pin Adapter Provides Pivot Point for Rotation
- Mount on Breadboard or Optical Table via Clearance Slot for 1/4" (M6) Cap Screws
- Clearance Slot Provides Up to 90° Rotation
The FMB1(/M) Rotation Baseplate provides compatibility between the OEM fixed mirror mounts and standard breadboards or optical tables. Four 1/4"-20 (M6 x 1.0) tapped holes through the baseplate match the footprint of all sizes of the fixed mirror mounts. An included dowel pin adapter is threaded into the central 1/4"-20 (M6 x 1.0) tap, providing a pivot point about which the baseplate can rotate when placed in one of the holes of a breadboard or optical table. A curved clearance slot allows the baseplate to be secured to a breadboard or optical table and provides up to 90° of rotation without removing the mounting cap screw.

- Convert Your Existing Post Holders into Universal Post Holder Style Mounts
- 360° Swiveling Base Fastens to Existing Ø1/2" Post Holders via a 1/4"-20 (M6) Cap Screw
- Magnets in Base Hold Position of Components on Breadboard During Initial Setup
- Also Available in Packs of Five
Our 360° swivel base adapter fits standard Ø1/2" post holders with 1/4"-20 (M6) mounting holes and minimizes the amount of time it takes to assemble an optical system. In addition, the swivel design is ideal for applications that require a large number of components to be packed into a small area. When our Ø1/2" post holders are used with this adapter, the combination is nearly that of our very popular Universal Post Holders. This anodized aluminum adapter has the benefit of compatibility with any of our existing Ø1/2" post holders but does not offer the same height flexibility of the swiveling post holders, which allow the post to be lowered all the way to the table. For ease of ordering, these base adapters are also available in packs of five.

- Mark the Position of Bases within an Optical System
- Realignment Based on Three Contact Points
- Use Two Contact Points to Re-Position Ø1" and Ø1.5" Posts within an Optical System
- Swivel Head Retainer Available with 200° of Rotation
Thorlabs' Position Retainers can be used to realign bases and other squared-off components that have been removed from an optical system. They act as markers on the breadboard or optical table in the event that you need to remove a component from your setup. The three white dots engraved on the surface of the retainer mark the three points that contact your part. The two dots near the ends of the outer arms can also be used independently as contacts for posts. For more information on using our anodized aluminum retainers with a post, click here.
The RSPCS(/M) Swivel Retainer features a swivel head for 200° of rotational adjustment. This enables users to save the arbitrary position and angular rotation of squared-off optomechanical components, as shown in Figure G10.1. To achieve this, the component should be independently locked before aligning the three dots on the RSPCS(/M) to the corner of the component. Partially loosen the tension adjuster screw and then mount the retainer to a breadboard tap while maintaining contact with all three points. Lastly, tighten the tension adjuster screw. After this the component can be removed from the setup and then later placed back into the same position.
The RSPC Fixed Retainer is a compact solution for situations where a tapped hole is diagonally positioned from the base, as shown in Figure G10.2. As with the RSPCS, the component should be independently locked before aligning the RSPC retainer. After the retainer is mounted in place, the component can be removed from the setup and then later placed back into the same position. The RSPC Retainer can also be secured to an optical table or breadboard via the CL6 clamp. This clamp is useful in situations where the RSPC cannot be placed directly over a hole in the table.
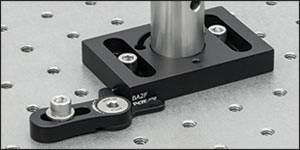
Click to Enlarge Figure G10.1 RSPCS Swiveling Position Retainer
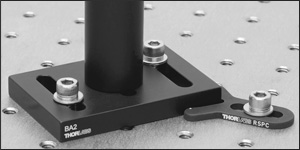
Click to Enlarge Figure G10.2 RSPC Position Retainer