Vacuum-Compatible Ø1/2" Post System
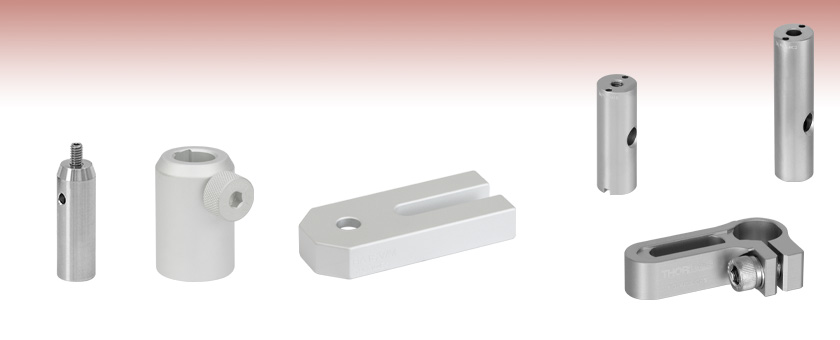
- Ø1/2" Post System Components for Vacuum Use
- All Components are Shipped Double Vacuum Bagged
- Constructed of 303, 316, 304L, and A4 Stainless Steel
and 6061-T6 and 2024-T3 Aluminum
TR2V
Ø1/2" Post,
8-32 Stud
BA1SV
Ø1/2" Post Holder Base
POLARIS-CA5
Non-Bridging Clamping Arm
PH2V
Ø1/2" Post Holder
PLS-H15
Ø1/2" Post, 8-32 Tap &
Alignment Pin Holes
PLS-HC2
Ø1/2" Post,
#8 Counterbore &
Alignment Pin Holes

Please Wait
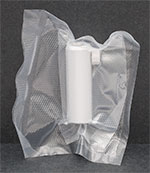
Click to Enlarge
All vacuum-compatible components are packaged inside a double vacuum bag.
Features
- Vacuum-Compatible Versions of Popular Optomechanical Components
- Ø1/2" Post System Includes Posts, Clamping Arms, Post Holders, Post Holder Bases, Thumbscrews, and Cap Screws
- All Components Compatible with 10-5 Torr Environments Directly Out of the Packaging
- Compatible with Lower Pressures with Additional User Processing
- All Components are Shipped Double Vacuum Bagged for Cleanroom Use
This page features vacuum-compatible versions of our most popular optomechanical components. These components are fabricated from specially-selected grades of stainless steel and aluminum for vacuum and cleanroom use. As shown in the photo to the right, all components are packaged in double airtight bags for cleanroom and vacuum chamber applications. We offer cap screws, setscrews, and washers for use with these items.
Additional Vacuum-Compatible Components
Many of our other Optomechanical Components can be special ordered for vacuum use. Contact Tech Support for details.
Vacuum Compatibility Information
Our vacuum-compatible optomechanics are chemically cleaned and prepared for vacuum applications before packaging. They are compatible directly out of the packaging with vacuum environments down to 10-6 Torr (>10-5 Torr for our PLS series posts, as well as our POLARIS-CA5C(/M) and POLARIS-CA5(/M) clamping arms). With additional cleaning and processing, they can be used at even lower pressures, only limited by the outgassing rate of the aluminum or stainless steel. The material properties of the aluminum or stainless steel and the cleaning methods completed by the end user should be used to determine the appropriateness of these products and materials in a specific vacuum system.
We also offer other optomechanical components which may be used in vacuum applications. Many of our Polaris Mirror Mounts are vacuum-compatible. We also offer Unanodized Aluminum Breadboards, which may be used in vacuum applications after undergoing cleaning and processing by the end user.
Vacuum Compatibility Specs
Item | TR Series Ø1/2" Posts | Ø1/2" Post Holders | Post Holder Bases | Thumbscrews | Vented Cap Screws & Washers |
---|---|---|---|---|---|
Vacuum Compatibility as Packageda |
>10-6 Torr | ||||
Materials | 304L Stainless Steel (Post) 316 Stainless Steel (Setscrew) |
6061-T6 Aluminum (Post Holder) 2024-T3 Aluminum (Thumbscrew) 353NDPK Epoxyb Low Vacuum Pressure Grease |
6061-T6 Aluminum | 2024-T3 Aluminum | 316 Stainless Steel (Imperial) A4 Stainless Steel (Metric) |
Preparation and Packaging |
Chemically Cleaned and Double Vacuum Bagged | ||||
Additional Vacuum Compatibility Information |
- | Grease Vapor Pressure: 10-13 Torr at 20 °C 10-5 Torr at 200 °C Epoxy Meets Low Outgassing Standards NASA ASTM E595 and Telcordia GR-1221 |
- | - | - |
Item | PLS Series Ø1/2" Posts | POLARIS-CA5C(/M) Clamping Arm | POLARIS-CA5(/M) Clamping Arm |
---|---|---|---|
Vacuum Compatibility as Packageda |
>10-5 Torr | ||
Materials | 303 Stainless Steel | Arm: 303 Stainless Steel; Screw: 18-8 Stainless Steel | |
Preparation and Packaging |
Chemically Cleaned and Double Vacuum Bagged |
Non-Bridging Clamping Arm Testing
Various tests were conducted to show the performance of our Non-Bridging Clamping Arms. Many of the results were then compared to other industry-standard products that were put to the same test to show the high-quality performance of the non-bridging clamping arms when used with our Ø1" Posts for Polaris Mounts. Similar performance can be expected across the family of Non-Bridging Clamping Arms. Click the links below for more information about a specific test.
- Laser Platform Deformation
- Determine the extent to which an industry-standard clamping fork deforms or permanently damages a stainless steel rigid platform, and whether or not the non-bridging clamping arm improves upon or prevents this damage.
- Post and Platform Mounting Torque
- Determine the ideal amount of clamping torque necessary to (1) securely mount a post within the flexure clamp bore of a non-bridging clamping arm and (2) to secure the clamping arm into a laser system. This data was then compared to the closest competitor's industry-standard clamping fork design.
- Post Breaking Torque
- Determine the amount of torque needed to break a Ø1" PLS-P150 post loose from a non-bridging clamping arm that was holding it.
- Post Deflection
- Determine how much a post for Polaris mounts will temporarily and permanently deflect when it is mounted within a non-bridging clamping arm and a force is applied.
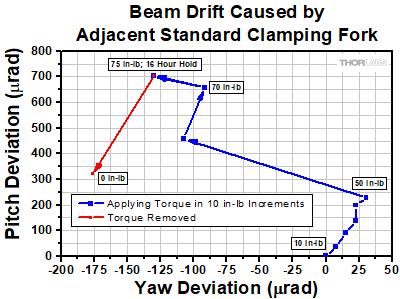
Click to Enlarge
Figure 1: Industry-Standard Clamping Fork Beam Drift
Laser Platform Deformation
Purpose: This testing was performed to determine the extent to which an industry-standard clamping fork deforms or permanently damages a stainless steel rigid platform and whether or not the non-bridging clamping arm improves upon or prevents this damage. The POLARIS-CA1 clamping arm was used for this test; similar results can be expected for all other non-bridging clamping arms. These measurements show that the non-bridging clamping arm significantly reduces temporary deformation to the surface and that no permanent damage was measured during our extensive tests.
Procedure: An industry-standard clamping fork was mounted in close proximity to another optical element that was used for aligning a beam onto a position detector. As the clamping fork was mounted to the platform at various torque values (blue data sets in Figure 1 and Figure 2), the yaw and pitch deviation of the beam was measured at the detector. At 75 in-lb of torque, the fork was left attached to the platform for 16 hours. After the 16 hour period, the fork was released from the table and the final beam deviation was recorded (red data sets in Figure 1 and Figure 2). This procedure was repeated for the POLARIS-CA1 clamping arm. Each test was performed at different regions of the platform. A final deviation of anything but zero indicated that the surface had been permanently deformed.
Results: As can be seen in the plots below and to the right, the industry-standard clamping fork created a yaw and pitch deviation of 131 µrad and 702 µrad, respectively, at 75 in-lb, while the POLARIS-CA1 clamping arm created a yaw and pitch deviation of 12.2 µrad and 61 µrad, respectively, at 75 in-lb. The POLARIS-CA1 also returned the beam to its initial position when released after a 16 hour hold. The industry-standard clamping fork did not return the beam to its original position; the beam stayed at a yaw and pitch deviation of 176 µrad and 321 µrad, respectively. The simulation results shown in Figures 3 and 4 show the amount of deformation created by an industry-standard clamping fork compared to the POLARIS-CA1 clamping arm.
Conclusion: The POLARIS-CA1 clamping arm caused no permanent damage to the optical mounting surface and it significantly minimized the deformation to the platform surface when it was in use (see Figures 3 and 4). The industry-standard clamping fork was shown to permanently damage the laser platform after use, and to create severe deformation to the surface while in use. As a result, the non-bridging clamping arm is ideal for use in systems requiring long term stability and consistent, precision alignments.
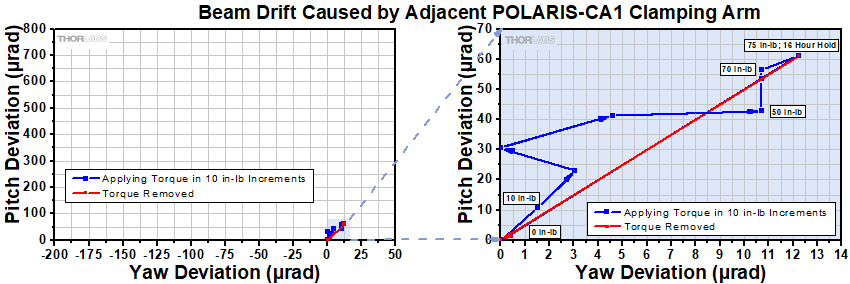
Click for Details
Figure 2: Note that the distortion caused by the non-bridging clamping arm at 75 in-lb is comparable to the distortion caused by the industry-standard clamping fork at 10 in-lb.
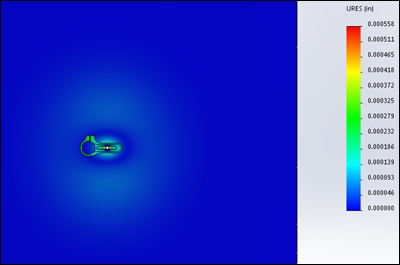
Click to Enlarge
Figure 4: In comparison, the POLARIS-CA1 clamping arm causes minimal deformations around the fork. Note that the scale on this second plot has been magnified by 10X in order to make these minimal deformations visible.
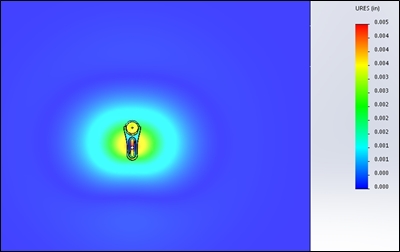
Click to Enlarge
Figure 3: The industry-standard clamping fork causes large deformations over a significant area surrounding the fork.
Mounting Torque
Purpose: This testing was performed to determine the ideal amount of clamping torque necessary to (1) securely mount a Ø1/2" or Ø1" post within the flexure clamp bore of a compatible non-bridging clamping arm and (2) to secure the clamping arm into a laser system. This data was then compared to the closest competitor's industry-standard clamping fork design.
Procedure: The POLARIS-CA1(/M) arm was used to hold a standard Ø1" post and the POLARIS-CA5(/M) arm was used to hold a PLS-Hx series Ø1/2" post. The clamping arm was first bolted to a stainless steel rigid platform, and the 1/4"-20 (M6 x 1.0) screw that controls the flexure clamp was actuated to specific torque values. At each torque value, the post had a rotational torque applied around its axis until it moved within the clamping arm's bore. The torque value at the moment directly before this "movement point" is called the holding torque (see plots below). Using similar methods, a mounting slot test was performed to find the ideal torque needed to secure the clamping arm to the laser platform. The mounting slot test was repeated for the POLARIS-SCA1 to determine if the slot size affects the torque measurements.
Results Summary: For optimal performance, the flexure clamping screw of an imperial Ø1" clamping arm should be tightened with 15 to 25 in-lb of torque and the flexure clamping screw of a metric Ø1" or Ø25 mm clamping arm with 1.75 to 3 N•m of torque. When mounting to a table or platform, we recommend using 40 to 65 in-lb of torque for an imperial Ø1" clamping arm and 4.75 to 7 N•m of torque for a metric Ø1" or Ø25 mm clamping arm. The POLARIS-CA5(/M) clamping arm has identical torque parameters of 30 to 40 in-lb (4.0 to 4.5 N•m). Please see below for the detailed results.
Conclusion: The non-bridging clamping arms were shown to be the ideal solution for securely mounting a component to a laser system platform. At only 20 in-lb and 40 in-lb of clamping torque for the flexure clamp and mounting slot respectively, a post mounted in an imperial Ø1" clamping arm can withstand up to 110 in-lb of opposing torque (corresponding torques for a metric Ø1" or Ø25 mm clamping arm are 2.4, 4.8, and 12.4 N•m, respectively). This performance is superior to the closest competitor's industry-standard clamping fork, which needs a clamping torque of 70 in-lb in the closed position to reach a similar value of 100 in-lb. For POLARIS-CA5(/M) clamp test results, please refer to the test results and plot links below. As demonstrated in the Laser Platform Deformation test above, minimizing the amount of torque applied to the mounting surface prevents permanent damage.
Test 1 Results: Flexure Clamp Holding Torque
As can be seen in Figure 6 below, at 20 in-lb of clamping torque, the POLARIS-CA1 provided 110 in-lb of holding torque. For reference, 110 in-lb of torque is enough to damage the threading on a 1/4"-20 stainless steel cap screw. The corresponding torque for the POLARIS-CA1/M is a holding torque of 12.4 N•m at a clamping torque of 2.4 N•m. The torque values for imperial and metric clamps are not a direct conversion due to an efficiency difference between 1/4"-20 and M6 x 1.0 screws. The efficiency of M6 screws is about 5% less than that of 1/4"-20 screws due to differences in diameter and pitch. All imperial Ø1" non-bridging clamping arms will perform similarly to the POLARIS-CA1, while all metric Ø1" or Ø25 mm non-bridging clamping arms will perform similarly to the POLARIS-CA1/M. The POLARIS-CA5(/M) clamping arm needs 40 in-lb (4.5 N•m) to provide 50 in-lb (5.7 N•m) of holding torque. Test results for the POLARIS-CA1/M and POLARIS-CA5(/M) clamps are also available below Figure 6.
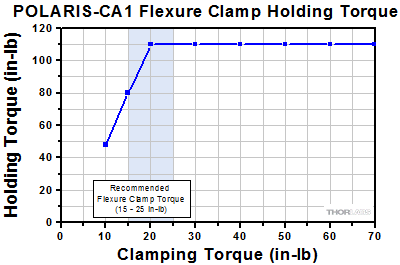
Click to Enlarge
Click for POLARIS-CA1/M Flexure Clamp Holding Torque Results
Click for POLARIS-CA5(/M) Flexure Clamp Holding Torque Results
Figure 6: Results from Test 1. The shaded region indicates the recommended flexure clamp torque. All imperial Ø1" non-bridging clamping arms will perform similarly to the POLARIS-CA1, while all metric Ø1" or Ø25 mm non-bridging clamping arms will perform similarly to the POLARIS-CA1/M.
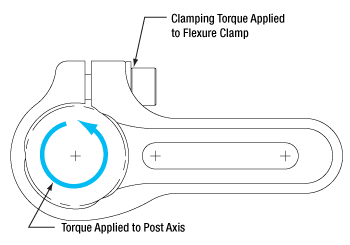
Click to Enlarge
Figure 5: Holding torque is measured at the moment directly before the "movement point" of the post being torqued.
Test 2 Results: Mounting Slot Holding Torque
The recommended torque for the mounting slot varies depending on the position of the 1/4"-20 (M6 x 1.0) cap screw within the slot (i.e. close to the post, midway along the slot, or far from the post). Figure 8 compares the slot holding torque of the POLARIS-SCA1 and POLARIS-CA1, and shows that the slot size does not affect the torque measurements. The recommended slot holding torque is 40 - 65 in-lb for imperial Ø1" clamping arms, while for metric Ø1" or Ø25 mm clamping arms the slot holding torque is 4.75 - 7 N•m. Similar to the Test 1 results, the torque values for imperial and metric clamps are not a direct conversion due to an efficiency difference between 1/4"-20 and M6 screws. The efficiency of M6 screws is about 5% less than that of 1/4"-20 screws due to differences in diameter and pitch. The POLARIS-CA5(/M) clamping arm needs 40 in-lb (4.5 N•m) of clamping torque to provide almost 40 in-lb (4.5 N•m) of holding torque at the close position. Test results for the POLARIS-CA1/M and POLARIS-CA5(/M) clamps are also available below Figure 8.
The performance of the closest competitor's clamping fork also depends on the position of the 1/4"-20 (M6 x 1.0) cap screw in the slot. However, as shown in Figure 9, the performance of the fork degrades sharply at the mid and far positions. At the far position, the best holding torque achieved is 32 in-lb with a clamping torque of 70 in-lb. As shown in Figure 10, at 40 in-lb of clamping torque, the POLARIS-CA1 provided 110 in-lb of holding torque, while at the same clamping torque, the competitor's fork only achieved a holding torque of 38 in-lb.
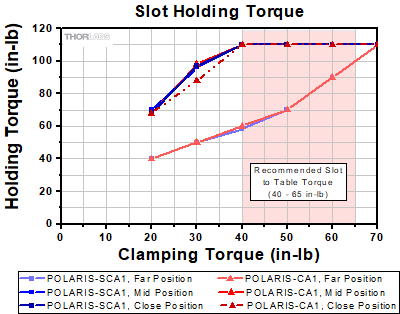
Click to Enlarge
Click for POLARIS-CA1/M Slot Holding Torque Results
Click for POLARIS-CA5(/M) Slot Holding Torque Results
Figure 8: Results from Test 2. The shaded region indicates the recommended torque to secure the clamping arm to the optical table. This comparison between the POLARIS-SCA1 and POLARIS-CA1 shows that the slot size does not affect the slot holding torque. All imperial Ø1" non-bridging clamping arms will perform similarly to the POLARIS-CA1, while all metric Ø1" or Ø25 mm non-bridging clamping arms will perform similarly to the POLARIS-CA1/M.
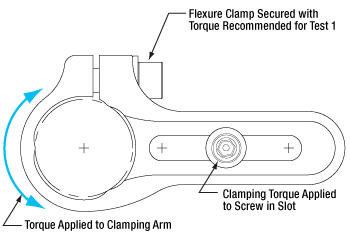
Click to Enlarge
Figure 7: Holding torque is measured at the moment directly before the "movement point" of the clamping arm being torqued.
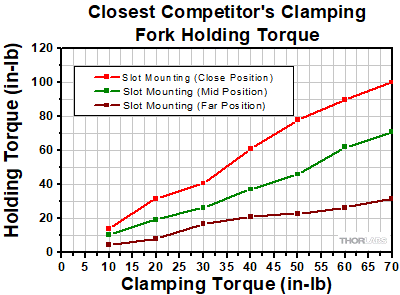
Click to Enlarge
Figure 9: Results from Test 2 on a competitor's Ø1" clamping fork. See Figure 8 for results from POLARIS-CA1(/M).
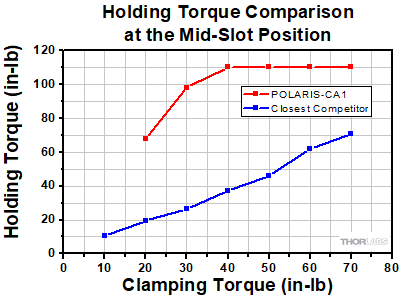
Click to Enlarge
Figure 10: Comparison of Test 2 results for POLARIS-CA1 and a competitor's Ø1" clamping fork, both at the middle position in the mounting slot.
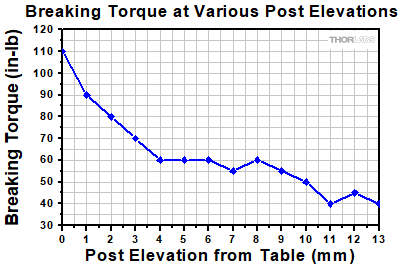
Click to Enlarge
Figure 12: Breaking force recorded with the post mounted at 14 different heights above the platform. This shows that upwards of 110 in-lb of torque is required to loosen the PLS-P150 post from the clamping arm when the post is in contact with the work surface.
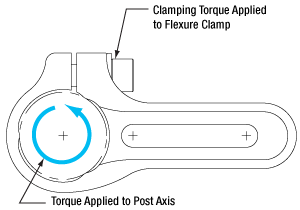
Click to Enlarge
Figure 11: Breaking torque is defined as the moment directly after the "movement point" of the post being torqued.
Breaking Torque
Purpose: This test was performed to determine the amount of torque needed to break a Ø1" PLS-P150 post loose from a non-bridging clamping arm. The POLARIS-CA1 clamping arm was used for this test; similar results can be expected for all other non-bridging clamping arms for Ø1" and Ø25 mm posts.
This test was repeated at various heights above the work surface.
Procedure: A PLS-P150 1.5" long, Ø1" post was secured with 25 in-lb of torque at various heights within a POLARIS-CA1 clamping arm, which was then secured to a custom laser platform. As shown in Figure 11, torque was then applied to the post axis until it reached its "movement point." This torque was recorded as the breaking torque.
Results: As can be seen in Figure 12, upwards of 110 in-lb (12.4 N•m) of torque is required to loosen the PLS-P150 post from the non-bridging clamping arm. When the post was raised off of the platform by 13 mm, a torque of about 40 in-lb (4.5 N•m) was still required to loosen the post. It is important to note here that the clamping arm is only 15.2 mm (0.60") thick.
Conclusion: The PLS-P150 post and clamping arm create an extremely stable system that is resistant to large forces acting upon it, even when the post is raised off of the platform by 13 mm. This is ideal for any custom or OEM system that requires components to stay aligned when faced with vibrations caused by shipping and installation.
Post Deflection
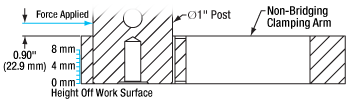
Click to Enlarge
Figure 13: A force was applied to the PLS-P150 post 0.90" (22.9 mm) above the edge of the clamping arm with the post mounted at nine different heights off of the mounting surface. At each mounting height, the post deflection was measured during and after the application of the force.
Purpose: This test was performed to determine the amount of temporary and permanent deflection of a Ø1" post for Polaris mirror mounts secured in a non-bridging clamping arm when a force is applied. The POLARIS-CA1 clamping arm was used for this test; similar results can be expected for all other non-bridging clamping arms for Ø1" and Ø25 mm posts. For Ø1/2" clamping arms, we recommend a post-to-mounting-surface distance of 1 mm or less to prevent permanent deflection when a ≤45 N force is applied.
Procedure: A PLS-P150 1.5" long, Ø1" post was secured with 25 in-lb of torque at various heights within a POLARIS-CA1 clamping arm, which was then secured to a custom laser platform. A force was then applied to the center of the post, 0.90" (22.9 mm) above the top edge of the clamping arm (see Figure 13 for details). This test was conducted with the post mounted at nine different heights off of the platform, ranging from 0 mm to 8 mm. The amount of deflection was measured while the force was being applied (Figure 14) and after the force was removed (Figure 15).
Results: Figure 14 shows that the PLS-P150 post will deflect by <0.01 mm as a force of ≤40 N is applied for any post height ≤8 mm, and by <0.17 mm as a force of ≤133 N is applied for any post height ≤8 mm. These values show the temporary deflection of the post while the force is being applied. For all of the post mounting heights tested (0 to 8 mm), an applied force ≤35 N caused a permanent deflection of the post smaller than 0.005 mm, measured after the force was removed. For the two lowest mounting heights, 0 and 2 mm, no permanent deflection was measured for applied forces of 45 N or less. At 133 N, the maximum force applied, permanent deflection for all tested mounting heights remained below 0.07 mm. For Ø1/2" clamping arms, we recommend a post-to-mounting-surface distance of 1 mm or less to prevent permanent deflection when a ≤45 N force is applied.
Conclusion: Our Ø1" posts and POLARIS-CA1 clamping arm create an extremely stable system that is able to resist large forces acting upon it. This is ideal for any custom or OEM system that requires components to stay aligned when faced with vibrations caused by shipping and installation.
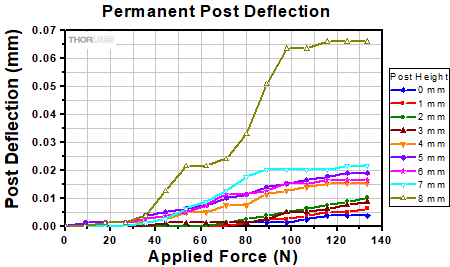
Click to Enlarge
Figure 15: Post deflection measured after the applied force was removed. The measurement was repeated with the bottom of the post positioned 0 to 8 mm above of the mounting surface (see the Procedure section for details). For Ø1" post-to-mounting-surface distances of 2 mm or less, no permanent deflection was measured if the force was ≤45 N. For Ø1/2" clamping arms, we recommend a post-to-mounting-surface distance of 1 mm or less to prevent permanent deflection when a ≤45 N force is applied.
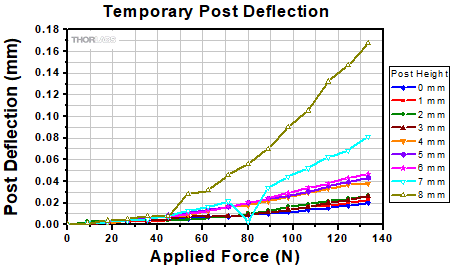
Click to Enlarge
Figure 14: Post deflection measured while a force was applied to the post. The measurement was repeated with the bottom of the post positioned 0 to 8 mm above of the mounting surface (see the Procedure section for details).
Insights into Best Lab Practices
Scroll down to read about a few things we consider when setting up lab equipment.
- Washers: Using Them with Optomech
- Bases: For Stability Orient the Side with the Undercut Down
Click here for more insights into lab practices and equipment.
Washers: Using Them with Optomech
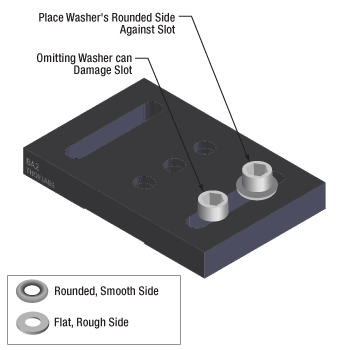
Click to Enlarge
Figure 174B Install washers before inserting bolts into slots to protect the slot from damage. The rounded, smooth side of the washer should be placed against the slot, and the rough, flat side should be in contact with the bolt head. The smooth surface is designed to translate easily across the anodized surface, without harming it. The BA2 base is illustrated.
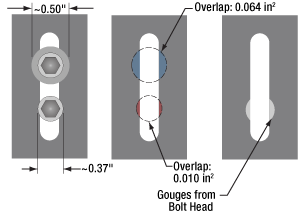
Click to Enlarge
Figure 174A The diameter of the washer is 35% larger than that of the bolt head. This results in over a six fold increase in overlap area with the slot of a BA2 base. By distributing the force of the bolt over a larger area, the washer help prevent gouging of the slot.
The head of a standard cap screw is not much larger than the major diameter of the thread (Figure 174A). For example, a 1/4"-20 screw has a head diameter between 0.365" and 0.375" and the clearance hole diameter for the threads is 0.264".
When the screw is tightened directly through the clearance hole to secure the device, the force is applied to the edge of the through hole, often cutting into the material (Figure 174A).
Once the material is permanently deformed, the screw head will want to fall back into the gouged groove, thereby moving the device back to that location when attempting to make fine adjustments.
A device with a circular through hole is not meant to translate around the screw thread so the deformation is not expected to be a problem.
However, a slot should provide the ability to secure the device anywhere along the length for the lifetime of the part. Using a washer distributes the force away from the slot edge to decrease the chance of deforming the slot and extending the lifetime of the part. Figure 174A illustrates the difference a washer can make. The contact area between the slot of a BA2 base and a 0.27" diameter cap screw is 0.010 in2. When a 0.5" diameter washer is used the contact area is 0.064 in2, which is over six times larger.
When using a Thorlabs washer, there are two distinct sides (Figure 174B). One side is flat and rough and the other is curved and polished. The curved and polished side should be placed against the device, which has an anodized surface.
As the screw tightens, the screw head can force the washer to spin against the anodized coating.
If the flat side is pressed down against the anodization, the friction created by the rough flat side can scratch the anodized aluminum. However, if the curved side is facing down, the smooth surface has less friction leading to less scratches and extending the visual appearance of the device.
Date of Last Edit: Dec. 4, 2019
Bases: For Stability Orient the Side with the Undercut Down
An undercut is machined into the bottom surface of bases like the BA2 (Figures 174C and 174D). The undercut creates feet, which are called pads. For maximum stability, the base should be oriented with its pads in contact with the table or breadboard.
The top surface of the base does not have an undercut and is the intended mounting surface for components.
Mounting the base upside down could result in the base rocking on the table or breadboard, or the base may exhibit other mechanical instability.
The Pads are Flatter than the Top Surface
The undercut is key to the flatness of the pads. The pads are machined flat after the undercut is made.
Friction heats the pads during the processing step that provides them with a maximally flat profile. By reducing the surface area of the pads, the undercut reduces the amount of heat generated during this step.
It is beneficial to minimize the heat generated during machining. Metal expands when heated, and the uneven heating that occurs during machining can distort the dimensions of the part. If the dimensions of the part are distorted during machining, the part can be left with high spots and other undesirable features after it cools. This can cause instability and misalignment when using the part.
Precision Instruments and Devices have Pads
Another example of a component with pads is the LX10 linear stage shown in Figure 174E.
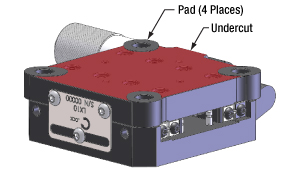
Click to Enlarge
Figure 174E Pads machined into Thorlabs' devices improve their stability when bolted in place. The pads are highly flat and project above the undercut region, which is highlighted red. The undercut limits the contact area with the table or breadboard.
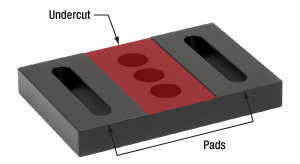
Click to Enlarge
Figure 174D This view of the bottom shows the undercut highlighted in red. By removing this material, the pads can be made maximally flat.
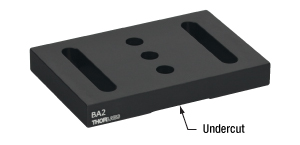
Click to Enlarge
Figure 174C For optimal stability, the base should be mounted with the undercut facing the optical table or breadboard.
Date of Last Edit: Dec. 9, 2019
Posted Comments: | |
No Comments Posted |

Vacuum Compatibility Specifications | |
---|---|
Vacuum Compatibility as Packageda |
>10-6 Torr |
Materials | 304L Stainless Steel (Post) 316 Stainless Steel (Setscrew) |
Preparation and Packaging |
Chemically Cleaned and Double Vacuum Bagged |
- Constructed of 304L and 316 Stainless Steel for Vacuum Applications
- One 8-32 (M4) Tapped Hole on Top and One 1/4"-20 (M6) Tapped Hole at Base
- Removable 8-32 (M4) Threaded Setscrew
- Available in Lengths Ranging from 3/4" to 3" (20 mm to 75 mm)
- We Also Offer a Complete Line of Standard Ø1/2" Posts
These non-magnetic, vacuum-compatible stainless steel posts are precision ground to Ø1/2" (Ø12.7 mm). One end has a 1/4"-20 (M6) tapped hole, while the other end has a removable, 8-32 (M4) threaded setscrew (5/64" [2 mm] hex). A side-located Ø0.13" (Ø3.1 mm) hole is bored straight through the post; a balldriver can be inserted through the hole to provide extra leverage when tightening mounted components. This hole also serves to vent the 8-32 (M4) threaded hole. The 1/4"-20 (M6) hole in the bottom of the post is not vented, so we recommend using a vented cap screw.

Vacuum Compatibility Specifications | |
---|---|
Vacuum Compatibilitya | 10-9 Torr at 25 °C with Proper Bake Out 10-5 Torr at 25 °C without Bake Out |
Materials | 303 Stainless Steel |
Preparation and Packaging | Chemically Cleaned and Double Vacuum Bagged |

Click to Enlarge
Directly attach a Polaris mount via a top-located 8-32 (M4) mounting hole without the need for a thread adapter. Dowel pins (not included) provide precision mounting.
OEM Solutions and Volume Orders
Thorlabs manufactures custom and high-volume Polaris products for use in custom and OEM systems. For pricing information on high-volume orders of our standard posts, please contact OEM Sales.
- Designed to Mount Polaris Mounts Up to Ø2"
- One Top-Located 8-32 (M4 x 0.7) Mounting Hole
- One Bottom-Located 1/4"-20 (M6 x 1.0) Mounting Hole
- Two Ø2 mm Alignment Pin Holes Around Each Mounting Hole for Precision Mounting (Dowel Pins Not Included)
- Vacuum Compatible to 10-9 Torr at 25 °C with Proper Bake Out
- 303 Stainless Steel Heat-Treated to Remove Internal Stresses for Increased System Stability
These Ø1/2" (Ø12.7 mm) posts feature one top-located 8-32 (M4 x 0.7) mounting hole and one bottom-located 1/4"-20 (M6 x 1.0) mounting hole. They are designed to mount Polaris mirror mounts up to Ø2"; see the table below for the resulting optic axis heights when used with each mount size. Each end of the post has two Ø2 mm alignment pin holes, which are located on either side of the mounting hole. Dowel pins are not included.
These posts are designed to mount to an optical surface using our POLARIS-CA5C(/M) or POLARIS-CA5(/M) non-bridging clamping arms for Ø1/2" posts or other comparable optomechanical components.
A Ø6 mm alignment bore is located 20 mm from the base and can be used in combination with our cage rods for the alignment of multiple mounts along a common optical axis or for fine angle tuning. Note that the alignment bore does not go completely through the PLS-H1 and PLS-H246/M posts. Instead, these posts contain two bores on opposite sides, within ±0.3°, that are 0.15" (3.8 mm) deep. Given their shorter length, a through bore would interfere with the mounting threads and prevent components from being securely attached to the post.
Polaris® Mount and Post Interoperabilitya | |||||||
---|---|---|---|---|---|---|---|
Item # | Post Length (L) |
Resulting Optical Axis Height (Optic Center) | |||||
Ø1/2" Mountsb |
POLARIS-K05P2 Ø1/2" Mount |
Kinematic |
Ø1.5 mm Mount & Ø2" Fixed Mount |
Ø2" Kinematic Mounts |
|||
1.00" | 1.50" | 1.62" | 1.75" | 2.00" | 2.25" | 2.40" | |
1.50" | 2.00" | 2.12" | 2.25" | 2.50" | 2.75" | 2.90" | |
PLS-H2 | 2.00" | 2.50" | 2.62" | 2.75" | 3.00" | 3.25" | 3.40" |
24.6 mm | 37.3 mm | 40.3 mm | 43.7 mm | 50.0 mm | 56.4 mm | 60.2 mm | |
37.3 mm | 50.0 mm | 53.0 mm | 56.4 mm | 62.7 mm | 69.1 mm | 72.9 mm | |
PLS-H496/M | 49.6 mm | 62.3 mm | 65.3 mm | 68.7 mm | 75.0 mm | 81.4 mm | 85.2 mm |

Vacuum Compatibility Specifications | |
---|---|
Vacuum Compatibilitya | 10-9 Torr at 25 °C with Proper Bake Out 10-5 Torr at 25 °C without Bake Out |
Materials | 303 Stainless Steel |
Preparation and Packaging | Chemically Cleaned and Double Vacuum Bagged |
- Compatible with Mounts with Threaded Mounting Holes
- Counterbore Hole for #8 (M4) Mounting Screw
- Two Ø2 mm Alignment Pin Holes for Precision Mounting (Dowel Pins Not Included)
- Vacuum Compatible to 10-9 Torr at 25 °C with Proper Bake Out
- 303 Stainless Steel Heat-Treated to Remove Internal Stresses for Increased System Stability
These Ø1/2" (Ø12.7 mm) posts feature a #8 (M4) counterbore hole for compatibility with mounts with threaded mounting holes, such as our KM05(/M) mirror mount. The top of the posts have two Ø2 mm alignment pin holes, which are located on either side of the counterbore hole. Dowel pins are not included. These posts are designed to mount to an optical surface using our POLARIS-CA5C(/M) or POLARIS-CA5(/M) non-bridging clamping arms for Ø1/2" posts or other comparable optomechanical components.
A Ø6 mm alignment bore is located 20 mm from the base and can be used in combination with our cage rods for the alignment of multiple mounts along a common optical axis or for fine angle tuning. Note that the alignment bore does not go completely through the PLS-HC1 and PLS-HC246/M posts. Instead, these posts contain two bores on opposite sides, within ±0.3°, that are 0.08" (2.0 mm) deep. Given their shorter length, a through bore would interfere with the counterbore and prevent components from being securely attached to the post.
Popular post lengths are available from stock; custom lengths can be requested by contacting Tech Support. Since the counterbore posts require clamping arms for Ø1/2" posts or other optomechanical components for mounting to an optical surface, the minimum length for custom posts should not be less than the height of the mounting component, which is 0.45" (11.4 mm) for these non-bridging clamping arms.

Vacuum Compatibility Specifications | |
---|---|
Vacuum Compatibility as Packageda |
10-9 Torr at 25 °C with Proper Bake Out 10-5 Torr at 25 °C without Bake Out |
Materials | Arm: 303 Stainless Steel Screw & Washer: 18-8 Stainless Steel |
Preparation and Packaging |
Chemically Cleaned and Double Vacuum Bagged |
Additional Vacuum Compatibility Information |
Grease Vapor Pressure: 10-13 Torr at 20 °C , 10-5 Torr at 200 °C |
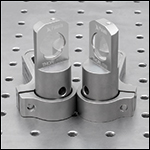
Click to Enlarge
The arm can be mounted with either flat surface in contact with the table, allowing for compact setups.
(POLARIS-CA1 Shown)
- Vacuum Compatible to 10-9 Torr at 25 °C with Proper Bake Out
- 3-Point Contact Bore with Flexure Clamping Mechanism
- Side-Located Screw Actuates Clamping Bore
- Allows Posts to be Rotated 360°
- Heat-Treated, Stress-Relieved Stainless Steel Provides Large Clamping Force
- Design Supports Left- and Right-Handed Orientations (See Lower Left Image)
- High Stability Ideal for Use with Our Kinematic Polaris Mirror Mounts
- ±0.001" (±0.02 mm) Surface Flatness
- Compact Clamping Arms for Space Limited Applications Also Available
The Non-Bridging Clamping Arms are the ideal solution for stably mounting our Ø1/2" Posts for Polaris Mounts or Ø1/2" posts with #8 (M4) counterbores. Each clamping arm, which is machined from heat-treated, stress-relieved stainless steel bar stock, provides extremely high holding forces with minimal torquing of the mounting screws. See the Clamping Arm Data tab for holding torque results and test details.
Non-Bridging Design: Industry Standard Clamping Fork
vs. Thorlabs' Non-Bridging Clamping Arm
Industry standard clamping forks are designed with a bridge, as shown in Figure 1, for clamping to pedestal-style posts or post holders. This design will slightly damage the laser platform during each use by pulling up the part of the platform located under the bridge. The non-bridging clamping arm, as shown in Figure 2, is designed with a flat top and bottom to eliminate this problem.
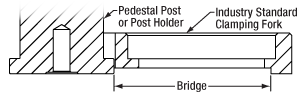
Click to Enlarge
Figure 1: A bridge is created when an industry standard clamping fork is used with a pedestal post.
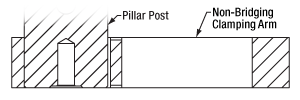
Click to Enlarge
Figure 2: The non-bridging clamping arm eliminates the bridge created by an industry standard clamping fork.
The flat, non-bridging top and bottom surfaces of each clamping arm allow it to be used with either side in contact with an optical table or other mounting surface. This feature allows the clamp to be positioned in left- or right-handed orientations and optical components to be placed in near contact to one another while minimizing the footprint (see the image to the left). Keep mounting screw torque below 40 in-lb (4.5 N•m) to protect the ±0.001" (±0.02 mm) flat mounting surface from marring due to the screw and washer.
The flexure clamp is actuated using a side-located 9/64" (M3) or 1/4"-20 (M6 x 1.0) cap screw and allows a post to be rotated 360° about its center. As the flexure clamp and mounting slot are secured with separate screws, the position of the arm and the rotational alignment of the post can be adjusted independently. Best performance is achieved with full post engagement.
The non-bridging clamping arm design has undergone extensive testing to ensure high-quality performance; see the Clamping Arm Data tab. For optimal performance, we recommend tightening the flexure clamping screw with 30 to 40 in-lb (4.0 to 4.5 N•m) of torque. We recommend using the same torque when mounting the clamp to a table or platform. These torque values can be dialed in using a torque driver.
Item # | Compatible Post Size |
Clamping Screw |
Slot Length | Footprint |
---|---|---|---|---|
POLARIS-CA5C | Ø1/2" (Ø12.7 mm) |
8-32 (9/64" Hex) |
0.29" (7.4 mm) |
1.52" x 0.89" (38.7 mm x 22.6 mm) |
POLARIS-CA5 | 1/4"-20 (3/16" Hex) |
0.60" (15.2 mm) |
1.87" x 1.00" (47.6 mm x 25.4 mm) |
|
POLARIS-CA5C/M | M4 x 0.7 (3 mm Hex) |
0.29" (7.4 mm) |
1.52" x 0.89" (38.7 mm x 22.6 mm) |
|
POLARIS-CA5/M | M6 x 1.0 (5 mm Hex) |
0.60" (15.2 mm) |
1.87" x 1.00" (47.6 mm x 25.4 mm) |

Vacuum Compatibility Specifications | |
---|---|
Vacuum Compatibility as Packageda |
>10-6 Torr |
Materials | 6061-T6 and 2024-T3 Aluminum 353NDPK Epoxyb Low Vacuum Pressure Grease |
Preparation and Packaging | Chemically Cleaned and Double Vacuum Bagged |
Additional Vacuum Compatibility Information |
Grease Vapor Pressure: 10-13 Torr at 20 °C, 10-5 Torr at 200 °C Epoxy Meets Low Outgassing Standards NASA ASTM E595 and Telcordia GR-1221 |
- Vacuum-Compatible, Unanodized Design (>10-6 Torr)
- Double Vacuum Bagged for Cleanroom Environments
- Extra Wide Relief Cut Provides a Two-Line Stable Contact for Post
- 1/4"-20 (M6) Tapped Hole on Bottom
- We Also Offer a Complete Line of Standard Ø1/2" Post Holders
These vacuum-compatible post holders are constructed from 6061-T6 and 2024-T3 aluminum and are designed with a wide, square relief cut that provides two lines of contact for highly stable post mounting. The imperial and metric post holders are equipped with our 3/16" (TS25HV) and 5 mm (TS6HV/M) vacuum-compatible hex-locking thumbscrews, respectively (also available separately below).
Please note that we do not recommend using an L wrench to tighten the thumbscrews included with these post holders, as this may break off the screw head. The recommended maximum torque is 28 in·lbs (3.2 N·m).

- Mount Ø1/2" Post Holders and Other Components to an Optical Table or Breadboard
- Vacuum-Compatible Design (>10-6 Torr)
- Double Vacuum Bagged for Cleanroom Environments
- Same Stability and Footprint as Our Standard Mounting Bases
These vacuum-compatible bases are similar to our standard mounting bases, which allow post holders to be secured to an optical table in a variety of position. A 3/8" (10 mm) long 1/4"-20 (M6) vented cap screw (SH25S038V for imperial or SH6MS10V for metric) is recommended for attaching post holders to our mounting bases.

Specifications | |
---|---|
Vacuum Compatibility as Packageda |
>10-6 Torr |
Materials | 2024-T3 Aluminum |
Preparation and Packaging |
Chemically Cleaned and Double Vacuum Bagged |
Maximum Torque | 28 in·lbs (3.2 N·m) |
The TS25HV and TS6HV/M are 1/4"-20 or M6 x 1.0-threaded for compatibility with our imperial or metric Vacuum-Compatible Ø1/2" Post Holders, respectively. Please note that we do not recommend using an L wrench hex key to tighten these thumbscrews, as this may break off the screw head. The recommended maximum torque is 28 in·lbs (3.2 N·m). We also offer standard spring-loaded thumbscrews.
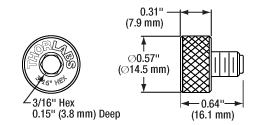
TS25HV Drawing

Vacuum Compatibility Specifications | |
---|---|
Vacuum Compatibility as Packageda |
>10-6 Torr |
Materials | 316 Stainless Steel (Imperial) A4 Stainless Steel (Metric) |
Preparation and Packaging |
Chemically Cleaned and Double Vacuum Bagged |
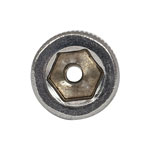
Click to Enlarge
These cap screws have a central Ø0.0625" (Ø1.6 mm) vent.
- 1/4"-20 and M6 x 1.0 Cap Screws with Vents for Vacuum Applications
- 1/4" (M6) Vacuum-Compatible Washers
- Constructed of 316 or A4 Stainless Steel
- Vacuum-Compatible Design (>10-6 Torr)
- Double Vacuum Bagged for Cleanroom Environments
- We Also Offer Standard Cap Screws in a Variety of Sizes
These cap screws and washers are constructed from 316 or A4 stainless steel. They have a central Ø0.0625" (Ø1.6 mm) hole through the body of the screw to serve as a vent, allowing trapped gas to escape from a blind hole when a vacuum chamber is pumped down.
Item # | Length | Hex | Material | Quantity |
---|---|---|---|---|
SH25S038V | 3/8" (9.5 mm) | 3/16" | 316 Stainless Steel | 5 |
SH25S050V | 1/2" (12.7 mm) | 5 | ||
SH25S063V | 5/8" (15.9 mm) | 5 | ||
SH25S075V | 3/4" (19.1 mm) | 5 | ||
SH25S100V | 1" (25.4 mm) | 5 | ||
SH6MS10V | 10 mm (0.39") | 5 mm | A4 Stainless Steel | 5 |
SH6MS12V | 12 mm (0.47") | 5 | ||
SH6MS16V | 16 mm (0.63") | 5 | ||
SH6MS20V | 20 mm (0.79") | 5 | ||
SH6MS25V | 25 mm (0.98") | 5 | ||
W25S050V | 1/4" Washer (M6 Compatible) | 316 Stainless Steel | 25 |