Piezoelectric Gimbal Mount
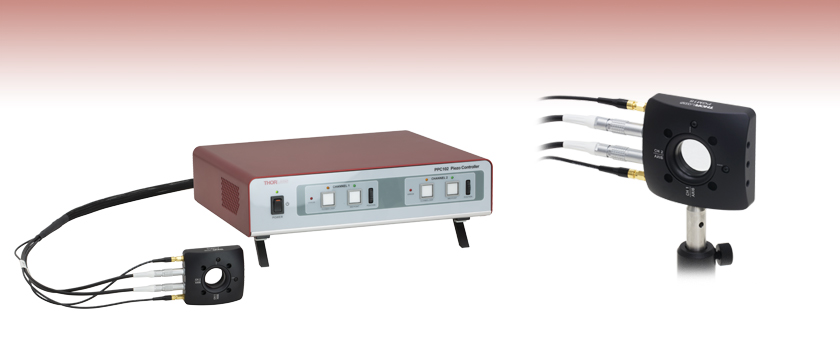
- True Gimbal Rotation with up to 30 mrad Angular Range
- Feedback Sensor Output Enables Closed-Loop Operation
- Angular Resolution: 0.05 μrad (Open Loop) or 0.14 μrad (Closed Loop)
- Operated via Included Controller or PC
PGM1SE
Piezoelectric Gimbal Mount with Included Controller
Piezo Gimbal Mount on Ø1/2" Post

Please Wait
Key Specificationsa | |
---|---|
Piezo Specifications | |
Piezo Angular Range | 30 mrad ± 15% (Open Loop) 20 mrad (Closed Loop) |
Angular Resolution | 0.05 µrad (Open Loop) 0.14 µrad (Closed Loop)b |
Piezo Control Voltage | -25 to 150 V |
Resonant Frequency (7.0 g Load) |
360 Hz ± 15% |
Piezo Drive Connectors | Male SMCc |
Strain Gauge Connectors | Male 7-Pin LEMOc |
Mechanical Specifications | |
Optic Size | Ø1.00" (Ø25.4 mm) |
Optic Thickness | 2 mm (0.08") Min 7.5 mm (0.30") Max |
Post Mounting Features | 8-32 (M4) Mounting Taps |
Cage System Compatibility | Four 4-40 Taps for 30 mm Cage Rods |
Applications
- Automatic Precise Laser Beam Steering
- Laser Scanning Microscopy
- LIDAR
- Optical Testing and Sensor Calibration
- Target Acquisition and Tracking
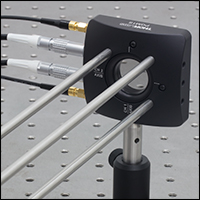
Click to Enlarge
Piezoelectric Gimbal Mount with 30 mm Cage Rods
Features
- True Gimbal Rotation Provides Precise Angle Adjustment without Changing Beam Path Length
- High Angular Range of 30 mrad (Open Loop) or 20 mrad (Closed Loop)
- Angular Resolution of 0.05 µrad (Open Loop) or 0.14 µrad (Closed Loop)
- Strain Gauge Feedback Sensors for Closed-Loop Operation
- Includes Individually Calibrated Controller
- Compact Size: 65.0 mm x 81.7 mm x 21.0 mm (2.56" x 3.22" x 0.83")
- SM1-Threaded (1.035"-40) Optic Bore for Ø1" Optics
- 4-40 Tapped Through Holes for Integration with a 30 mm Cage System
- Minimum Piezo Angular Adjustment: 0.1 arcsec (0.5 µrad)
The PGM1SE(/M) Piezoelectric Gimbal Mount has two axes that each rotate the mounted optic about a gimbal axis, keeping the center of the optic in a fixed position. Each axis is capable of scanning over a high piezoelectric angular range of 30 mrad with a resolution of 0.05 µrad in open-loop mode (20 mrad angular range and 0.14 µrad resolution in closed-loop mode). See the Specs tab for complete specifications.
A Ø1" optic can be mounted in the SM1-threaded optic bore and secured with the included SM1 retaining ring. The mount can hold optics between 2 mm and 7.5 mm thick; the optic is installed via the back of the mount, which keeps the optic surface coincident with the gimbal axes, regardless of the optic thickness. We do not recommend mounting an SM1 lens tube to the threading as it will apply excessive torque to the gimbal element.
Six 8-32 (M4) tapped holes on the optic mount allow it to be mounted on a Ø1/2" post. Additionally, four 4-40 tapped holes around the optic bore on both sides of the mount provide compatibility with 30 mm cage systems.
Each mount is shipped with a piezo controller that has been factory calibrated to the specific mount and supplies a voltage of -25 to +150 VDC. Piezo control is supported through the included Kinesis® and APT™ GUIs, either locally using the paired controller or by using an externally supplied control voltage. See the Software & External Control tab for more details. The controller offers USB and RS-232 interfaces for computer control, a BNC input for the addition of external drive signals, and a BNC output that gives either positioning feedback from the mount’s built-in capacitive sensors or a signal proportional to the piezo drive voltage. In addition, a DB15 connector provides signals that can be used for synchronization with external equipment. A USB 2.0 (A to B) cable is included.
Controller Specifications | |
---|---|
Piezoelectric Output | |
Output Voltage | -30 to 150 VDC |
Output Current | 150 mA |
Voltage Stability | 100 ppm over 24 hoursa |
Noise | <0.5 mV RMS (Bandwidth 20 Hz to 100 kHz) |
Typical Piezo Capacitance | 1 to 10 µF |
External Input (BNC) | |
Input Impedance | 10 kΩ |
Input Voltage | -10 to +10 VDC |
Absolute Maximum Input Voltage | ±20 VDC |
Input Voltage for Full Range | 10 VDC ±2% |
External Output (BNC) | |
Output Voltage Range | 0 to 10 V (Nominal for Full Range)b |
Minimum Recommended Load Impedance | 10 kΩ |
Protection | Protected Against Short Circuit |
Scaling Factor (HV Monitor) | 1/15 (10 V for a Piezo Voltage of 150 V) |
User Input/Output (D-Type 15 Pin Female) | |
4 Digital Inputs | TTL Levels |
4 Digital Outputs | Open Collector |
Trigger Input | TTL |
Trigger Output | TTL, 5 V Logic |
User 5 V | 100 mA Max |
Input Power Requirements (IEC Connector) | |
Voltage | 24 VDC ±5% |
Supply Current | <4 A |
Protection | Internal Fuse, 4 A Slow Blow |
For more information on the controls and connectors on the PPC102 controller, please see the PGM1SE(/M) manual for Kinesis® or APT™.
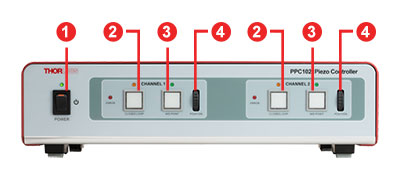
Click to Enlarge
Front Panel of the Piezoelectric Gimbal Mount Controller
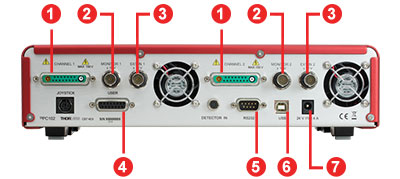
Click to Enlarge
Back Panel of the Piezoelectric Gimbal Mount Controller
Front Panel Controls | ||
---|---|---|
Callout | Label | Description |
1 | Power Button and LED | Applies and Removes Power to the Controller |
2 | Closed Loop Button and LEDa | Switches the Unit to Closed-Loop Operation |
3 | Midpoint Button and LEDa | Moves the Associated Channel to its Midpoint Position Open Loop: Sets Drive Voltage to 60 V Closed Loop: Sets Angular Position to 0 mrad |
4 | Position Wheela | Adjusts the Drive Voltage and/or Angular Position |
Back Panel Controls | ||
---|---|---|
Callout | Label | Description |
1 | Channel 1 / 2 | Provides the Drive Signal to the Piezo Actuator Connected to the Associated Channel |
2 | Monitor 1 / 2 | Used to Monitor the Piezo Actuator on an Oscilloscope or Other Device |
3 | Ext In 1 / 2 | Used to Control the Piezo Mount from an External Source Open Loop: -2 to +10 V gives -25 to 150 V Drive Voltage Closed Loop: 0 to +10 V gives ±10 mrad Adjustment |
4 | User | Contains a Number of Connections for Programmable Logic Linesa |
5 | RS232 | Provides Connection for Serial Port Communication |
6 | USB | USB Port for PC Operation |
7 | 24 V, 4 A | Power Supply (Included) |
Piezo Mount Pin Diagrams
Piezo Drive
SMC Male

Input Voltage: -25 to +150 V
Strain Gauge Feedback
7-Pin LEMO
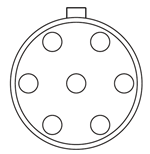
Piezo Controller Pin Diagrams
Channel 1 / Channel 2 Connectors
Pin | Description | Pin | Description |
---|---|---|---|
1 | High Voltage Ground (Return) | 8 | HV Ground (Return) |
2 | Not Used | 9 | Not Used |
3 | Not Used | 10 | Stage IDb |
4 | Sine Wave Excitation Output | 11 | Low Voltage Ground |
5 | Not Used | 12 | Low Voltage Ground |
6 | +15 V (Preamp Supply)a | 13 | Piezo ID (Legacy Stages)b |
7 | Low Voltage Ground | 14 | Position Sense Input (Strain Gauge) |
Coaxial Male |
Position Sense Input (Strain Gauge) |
15 | -15 V (Preamp Supply)a |
Coaxial Female |
HV Output |
User Connectora
Female DB15
Pin | Description | Return | Pin | Description | Return |
---|---|---|---|---|---|
1 | Digital Output 1 | 5, 9, 10 | 9 | Digital Ground | - |
2 | Digital Output 2 | 5, 9, 10 | 10 | Digital Ground | - |
3 | Digital Output 3 | 5, 9, 10 | 11 | For Future Use (Trigger Out) |
5, 9, 10 |
4 | Digital Output 4 | 5, 9, 10 | 12 | For Future Use (Trigger In)b |
5, 9, 10 |
5 | Digital Ground | - | 13 | Digital Input 4 | 5, 9, 10 |
6 | Digital Input 1 | 5, 9, 10 | 14 | 5 V Supply Output | 5, 9, 10 |
7 | Digital Input 2 | 5, 9, 10 | 15 | 5 V Supply Output | 5, 9, 10 |
8 | Digital Input 3 | 5, 9, 10 |
Computer Control via RS-232
Male DB9
Pin | Description | Pin | Description |
---|---|---|---|
1 | Not Connected | 6 | Not Connected |
2 | RX (Controller Input) | 7 | Not Connected |
3 | TX (Controller Output) | 8 | Not Connected |
4 | Not Connected | 9 | Not Connected |
5 | Ground |
Computer Control via USB
Female Type B USB
External Input
BNC Female
Input Voltage: -10 V to +10 V
Input Impedance: 10 kΩ
External Output
BNC Female
Output Voltage: 0 V to +10 V
Output Impedance: 100 Ω
Minimum Recommended
Output Impedance: 10 kΩ
Software
APT Version 3.21.6
The APT Software Package includes a GUI for control of the Piezo Objective Scanner.
Also Available:
- Communications Protocol
Software
Kinesis Version 1.14.47
The Kinesis Software Package includes a GUI for control of the Piezo Objective Scanner.
Also Available:
- Communications Protocol
Click to Enlarge
Graphical View of Piezo Operation in the Kinesis® GUI
The gimbal mount can be driven using the included standalone Kinesis® GUI, the legacy APT™ GUI, or an externally supplied control voltage. Complete details on control are available in the manuals for Kinesis and APT (PDF links).
Open-Loop Operation vs. Closed-Loop Operation
There are two operating modes for the mount: open loop and closed loop. In open-loop operation, which supports an adjustment range of 30 mrad ± 15%, the user controls the piezo drive voltage (in V). The applied drive voltage corresponds to some amount of angular adjustment. For piezoelectric materials, this displacement does not depend linearly on the applied voltage: it exhibits nonlinearity and hysteresis. It is therefore not straightforward to adjust the mount by choosing the drive voltage. The scanner's built-in capacitive feedback sensors measure the angular position with 0.05 µrad resolution in open-loop operation.
In closed-loop operation, which supports an adjustment range of 20 mrad, the user directly controls the angular position (in mrad). The built-in capacitive feedback sensors measure the objective displacement with 0.14 µrad resolution and automatically adjust the drive voltage in order to correct for inaccuracies in closed-loop operation.
Standalone Kinesis and APT GUIs
The Kinesis and APT GUIs support both open- and closed-loop operation. The piezo drive voltage or angular position can be directly typed in, changed by dragging the output knob (APT only), or incremented or decremented in fixed, user-defined amounts.
Click to Enlarge
Kinesis® GUI Panel During Open-Loop Operation
Click to Enlarge
Kinesis® GUI Panel During Closed-Loop Operation
In addition, the GUIs enable software-based PID loop tuning. The default settings are designed to provide stable operation in most applications, but fine tuning the PID loop helps account for the specific optics installed in the mount, reducing positional overshoots and ringing about the commanded angular position.
Externally Supplied Control Voltage
An external voltage can be applied using the external input BNC connector on the controller. In open-loop operation, the input voltage range of -2 V to +10 V corresponds to a drive voltage range of -25 V to +150 V, while in closed-loop operation, a the input voltage range from 0 V to +10 V corresponds to ±10 mrad angular adjustment.
DB15 Connector
The DB15 connector on the controller provides several electrical signals that can be used to synchronize the movement of the piezo stage with other equipment. Details on this connector are available in Appendix A.2 of the Kinesis and APT manuals (PDF links).
Thorlabs' Kinesis® software features new .NET controls which can be used by third-party developers working in the latest C#, Visual Basic, LabVIEW™, or any .NET compatible languages to create custom applications.
C#
This programming language is designed to allow multiple programming paradigms, or languages, to be used, thus allowing for complex problems to be solved in an easy or efficient manner. It encompasses typing, imperative, declarative, functional, generic, object-oriented, and component-oriented programming. By providing functionality with this common software platform, Thorlabs has ensured that users can easily mix and match any of the Kinesis controllers in a single application, while only having to learn a single set of software tools. In this way, it is perfectly feasible to combine any of the controllers from the low-powered, single-axis to the high-powered, multi-axis systems and control all from a single, PC-based unified software interface.
The Kinesis System Software allows two methods of usage: graphical user interface (GUI) utilities for direct interaction and control of the controllers 'out of the box', and a set of programming interfaces that allow custom-integrated positioning and alignment solutions to be easily programmed in the development language of choice.
For a collection of example projects that can be compiled and run to demonstrate the different ways in which developers can build on the Kinesis motion control libraries, click on the links below. Please note that a separate integrated development environment (IDE) (e.g., Microsoft Visual Studio) will be required to execute the Quick Start examples. The C# example projects can be executed using the included .NET controls in the Kinesis software package (see the Kinesis Software tab for details).
![]() |
Click Here for the Kinesis with C# Quick Start Guide Click Here for C# Example Projects Click Here for Quick Start Device Control Examples |
![]() |
LabVIEW
LabVIEW can be used to communicate with any Kinesis- or APT-based controller via .NET controls. In LabVIEW, you build a user interface, known as a front panel, with a set of tools and objects and then add code using graphical representations of functions to control the front panel objects. The LabVIEW tutorial, provided below, provides some information on using the .NET controls to create control GUIs for Kinesis- and APT-driven devices within LabVIEW. It includes an overview with basic information about using controllers in LabVIEW and explains the setup procedure that needs to be completed before using a LabVIEW GUI to operate a device.
![]() |
Click Here to View the LabVIEW Guide Click Here to View the Kinesis with LabVIEW Overview Page |
![]() |
The APT video tutorials available here fall into two main groups - one group covers using the supplied APT utilities and the second group covers programming the APT System using a selection of different programming environments.
Disclaimer: The videos below were originally produced in Adobe Flash. Following the discontinuation of Flash after 2020, these tutorials were re-recorded for future use. The Flash Player controls still appear in the bottom of each video, but they are not functional.
Every APT controller is supplied with the utilities APTUser and APTConfig. APTUser provides a quick and easy way of interacting with the APT control hardware using intuitive graphical control panels. APTConfig is an 'off-line' utility that allows various system wide settings to be made such as pre-selecting mechanical stage types and associating them with specific motion controllers.
APT User Utility
The first video below gives an overview of using the APTUser Utility. The OptoDriver single channel controller products can be operated via their front panel controls in the absence of a control PC. The stored settings relating to the operation of these front panel controls can be changed using the APTUser utility. The second video illustrates this process.
APT Config Utility
There are various APT system-wide settings that can be made using the APT Config utility, including setting up a simulated hardware configuration and associating mechanical stages with specific motor drive channels. The first video presents a brief overview of the APT Config application. More details on creating a simulated hardware configuration and making stage associations are present in the next two videos.
APT Programming
The APT Software System is implemented as a collection of ActiveX Controls. ActiveX Controls are language-independant software modules that provide both a graphical user interface and a programming interface. There is an ActiveX Control type for each type of hardware unit, e.g. a Motor ActiveX Control covers operation with any type of APT motor controller (DC or stepper). Many Windows software development environments and languages directly support ActiveX Controls, and, once such a Control is embedded into a custom application, all of the functionality it contains is immediately available to the application for automated operation. The videos below illustrate the basics of using the APT ActiveX Controls with LabVIEW, Visual Basic, and Visual C++. Note that many other languages support ActiveX including LabWindows CVI, C++ Builder, VB.NET, C#.NET, Office VBA, Matlab, HPVEE etc. Although these environments are not covered specifically by the tutorial videos, many of the ideas shown will still be relevant to using these other languages.
Visual Basic
Part 1 illustrates how to get an APT ActiveX Control running within Visual Basic, and Part 2 goes on to show how to program a custom positioning sequence.
LabVIEW
Full Active support is provided by LabVIEW and the series of tutorial videos below illustrate the basic building blocks in creating a custom APT motion control sequence. We start by showing how to call up the Thorlabs-supplied online help during software development. Part 2 illustrates how to create an APT ActiveX Control. ActiveX Controls provide both Methods (i.e. Functions) and Properties (i.e. Value Settings). Parts 3 and 4 show how to create and wire up both the methods and properties exposed by an ActiveX Control. Finally, in Part 5, we pull everything together and show a completed LabVIEW example program that demonstrates a custom move sequence.
Part 1: Accessing Online Help
Part 2: Creating an ActiveX Control
Part 3: Create an ActiveX Method
Part 4: Create an ActiveX Property
Part 5: How to Start an ActiveX Control
The following tutorial videos illustrate alternative ways of creating Method and Property nodes:
Create an ActiveX Method (Alternative)
Create an ActiveX Property (Alternative)
Visual C++
Part 1 illustrates how to get an APT ActiveX Control running within Visual C++, and Part 2 goes on to show how to program a custom positioning sequence.
MATLAB
For assistance when using MATLAB and ActiveX controls with the Thorlabs APT positioners, click here.
To further assist programmers, a guide to programming the APT software in LabVIEW is also available here.
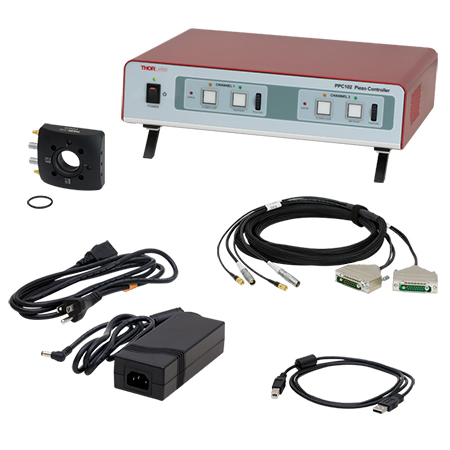
Click to Enlarge
Items Included with PGM1SE(/M) (North American Power Cord Shown)
Item # PGM1SE(/M) consists of the following:
- PGM1S(/M) Piezoelectric Gimbal Mount
- PPC102 Piezo Controller
- Dual-Channel Piezo Drive and Strain Gauge Feedback Cable Bundle
- USB 2.0 A-to-B Cable
- Power Supply and Region-Specific Power Cord
Posted Comments: | |
No Comments Posted |