Compact Laser Diode Driver with TEC and Mount for Butterfly Packages
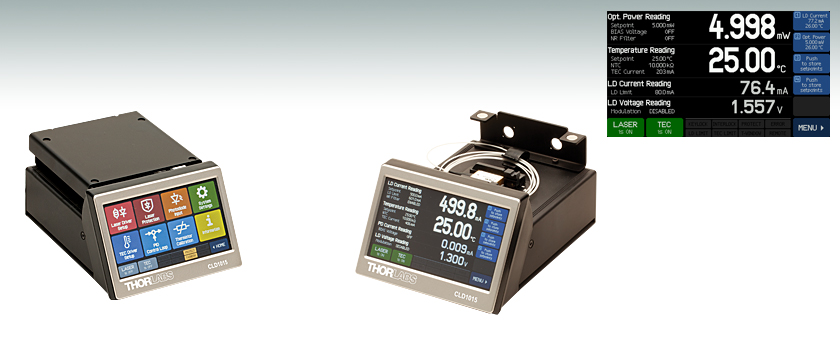
- Compact, All-in-One Current Source, Temperature Controller, and Mount
- Compatible with Thorlabs' Butterfly Lasers
- Touch Screen Controlled and Remotely Programmable
CLD1015
Drives Butterfly
Packaged Laser Diodes
CLD1015
Shown with a
Butterfly Laser
(Not Included)
Main Operation Panel in Constant Power
Operating Mode

Please Wait
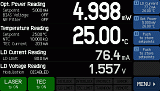
Click to Enlarge
Home Screen
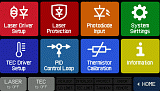
Click to Enlarge
Menu Screen
Features
- Integrated Mount Compatible with Thorlabs' Butterfly Laser Diodes
- Operates in Constant Current or Constant Power Mode
- Controlled Locally with Touch Screen GUI or Remotely over USB
- Supports Laser Diode Drive Currents up to 1.5 A at 4 V
- Provides up to 3.0 A of TEC Current
- Compact Size: 111 mm x 73.5 mm x 169.9 mm (4.37" x 2.9" x 6.69")
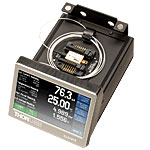
Click to Enlarge
The CLD1015 shown with a butterfly laser installed.
The CLD1015 Laser Diode and Temperature Controller is a complete driver package designed to drive and cool pigtailed butterfly laser diodes (see the Pin Diagram tab for details). It contains a built-in mount for portability and mechanical stability. The CLD1015 accepts fiber-coupled lasers, superluminescent diodes, and laser amplifiers in both type 1 and type 2 butterfly packages. It supplies up to 1.5 A of drive current, making it compatible with Thorlabs' entire family of pigtailed butterfly diode lasers. This all-in-one unit provides a high degree of output stability and maintains the diode temperature with 0.005 °C of stability over 24 hours, prolonging the life of the diode. In addition to a full complement of safety features, such as a soft start mode, current and temperature limits, and external interlock compatibility, the CLD1015 laser diode driver includes a switchable noise reduction filter and a modulation input.
This laser diode driver is controlled with a built-in 4.3" diagonal, color touch screen, making it easy to tune, tweak, and optimize the laser output parameters. Operating parameters are set using the intuitive menu system, and the user is never more than two taps away from the home screen. For screenshots of the interface, please see the Display tab. A mini-USB interface on the rear of the unit enables remote control of all settings using several common programming languages, including LabVIEW™ and the Standard Commands for Programmable Instruments (SCPI) standard. For the full array of options, please refer to the Software tab. When using the CLD1015 to drive a laser, make sure that all of the operating parameters are set within the maximum ratings of your device.
Compact LD Driver, TEC, and Mount Selection Guide | ||
---|---|---|
Item # | Accepted Package Configurations | Max Drive Current |
CLD1015 | Type 1 and Type 2 Butterfly Packages | 1.5 A (@ 4 V) |
CLD1010LP | TO Can Packages with an A, D, E, or G Pin Code | 1.0 A (@ 8 V) |
CLD1011LP | TO Can Packages with a B, C, or H Pin Code | 1.0 A (@ 8 V) |
When fully assembled, this compact device measures just 4.37" x 2.9" x 6.69" (111 mm x 73.5 mm x 169.9 mm), ideal for tightly packed setups. Fiber cables can be fed through the ports on the back of the unit, which are also compatible with Thorlabs' FC-to-FC Mating Sleeves (not included). Two of the holes accept square flange mating sleeves, and two are designed for D-hole mating sleeves. A magnetically sealed lid encloses the laser package in the unit, protecting it from particulates and other lab hazards. Two mounting clips, compatible with 1/4"-20 and M6 bolts, are supplied with the laser diode driver to secure it to a breadboard.
For driver software, as well as programming reference guides for Standard Commands for the Programmable Instruments (SCPI) standard, LabVIEW™, Visual C++, Visual C#, and Visual Basic, please see the Software tab.
Note: This laser diode driver may be controlled locally via the touch screen or remotely over USB. When controlled locally via the touch screen, the resolution of the laser diode driver is limited by the display; the full resolution can be accessed when the device is controlled remotely. The command sets that are accessible over USB - for example, via LabVIEW or the Standard Commands for Programmable Instruments (SCPI) - offer increased resolution, as shown in the table below.
Laser Diode Driver Specifications
Via Front Panela | Via Remote Controla | |||
---|---|---|---|---|
Current Control (Constant Current Mode) | ||||
Control Range | 0 to 1.5 A | |||
Compliance Voltage | >4 V | |||
Resolution | 100 µA | 50 µA | ||
Accuracy | ±(0.1% + 500 µA) | |||
Noise and Ripple (Typical; 10 Hz to 10 MHz, RMS; @ 3.3 Ω Load, Current <1.2 A) |
10 µA without Noise Reduction Filter 5 µA with Noise Reduction Filter |
|||
Drift (24 Hours) | <50 µA @ 0 - 10 Hz in Constant Ambient Temperature | |||
Temperature Coefficient | <50 ppm/°C | |||
Current Limit | ||||
Setting Range | 1 mA to 1.5 A | |||
Resolution | 100 µA | 50 µA | ||
Accuracy | ±(0.12% + 800 µA) | |||
Photodiode Input | ||||
Photocurrent Measurement Rangesb | 0 to 2 mA (Low) 2 to 20 mA (High) |
|||
Photocurrent Resolutionb | 100 nA (Low) 1 µA (High) |
70 nA (Low) 700 nA (High) |
||
Photocurrent Accuracyb | ±(0.08% +0.5 µA) (Low) ±(0.08% +5 µA) (High) |
|||
Photodiode Reverse Bias Voltage | 0.1 to 6 V | |||
Photodiode Input Impedance | ~0 Ω (Virtual Ground) | |||
Power Control (Constant Power Mode) | ||||
Photocurrent Control Rangesb | 0 to 2 mA (Low) 0 to 20 mA (High) |
|||
Laser Voltage Measurement | ||||
Resolution | 1 mV | 200 µV | ||
Accuracy | ±(1% + 40 mV) | |||
Laser Overvoltage Protection | ||||
Trip Voltage (Typical) | 4.2 V | |||
Modulation Input | ||||
Input Voltage | ±10 V | |||
Input Impedance | 10 kΩ | |||
3 dB Small Signal Bandwidth (Constant Current Mode) |
DC to 250 kHz without Noise Reduction Filter DC to 7.5 kHz with Noise Reduction Filter |
|||
Modulation Coefficient (Constant Current Mode) |
150 mA/V ± 5% | |||
Modulation Coefficient (Constant Power Mode)c |
200 µA/V ± 5% (Low) 2 mA/V ± 5% (High) |
TEC Specifications
Via Front Panela | Via Remote Controla | |
---|---|---|
TEC Current Output | ||
Control Range | -3.0 to +3.0 A | |
Compliance Voltage | >4.7 V | |
Maximum Output Power | >14.1 W | |
Resolution | 1 mA | 100 µA |
Accuracy | ±(0.2% + 20 mA) | |
TEC Current Limit | ||
Setting Range | 5 mA to 3.0 A | |
Resolution | 1 mA | 100 µA |
Accuracy | ±(0.2% + 20 mA) | |
NTC Thermistor Sensors | ||
Resistance Measurement Range |
300 Ω to 150 kΩ | |
Control Rangeb | -55 °C to +150 °C (Max) | |
Temperature Resolution | 0.01 °C | |
Resistance Resolution | 1 Ω | |
Accuracy | ±(0.1% + 1 Ω) | |
Temperature Stabilityb (24 Hours) |
<0.005 °C (Typical) | |
Temperature Coefficient | <5 mK/°C | |
Temperature Window Protection | ||
Setting Range | 0.01 °C to 100.0 °C | |
Protection Reset Delay | 0 to 600 s |
General Specifications | |
---|---|
Interface | |
USB 2.0 | Compliant with USBTMC/USBTMC USB488 Specification Rev. 1.0 |
Protocol | SCPI-Compliant Command Set |
Supplied Drivers | VISA VXI pnp™, MS Visual Studio™, MS Visual Studio.net™, LabVIEW™, LabWindows/CVI™ |
General Data | |
Safety Features | Interlock, Keylock Switch, Laser Current Limit, Soft Start, Short Circuit when Laser Off, Laser Overvoltage Protection, Over Temperature Protection, Temperature Window Protection |
Display | 4.3" LCD TFT, 480 x 272 Pixels |
Socket for Laser, Photodiode, NTC, TEC | Compatible with Butterfly Type 1 (Pump) and Butterfly Type 2 (Telecom) |
Connector for DC Power Input | 2.0 mm Center Pin Connected to + |
Connector for Modulation Input | SMA |
Connector for Interlock & Laser On Signal | 2.5 mm Mono Phono Jack |
Connector for USB-Interface | USB Type Mini-B |
Chassis Ground Connector | 4 mm Banana Jack |
Desktop Power Supply, Line Voltage, Line Frequency | AC: 100 to 240 V ± 10%, 47 to 63 Hz DC: 12 V ± 5% / 3.5 A |
Maximum Power Consumption | 40 VA |
Operating Temperature | 0 to +40 °C |
Storage Temperature | -40 to +70°C |
Warm-up Time for Rated Accuracy | 30 min |
Weight (with Power Supply) | 1.0 kg |
Weight (without Power Supply) | 0.75 kg |
Dimensions without Operating Elementsa (W x H x D) | 111 mm x 73.5 mm x 153.3 mm (4.37" x 2.9" x 6.04") |
Dimensions with Operating Elementsa (W x H x D) | 111 mm x 73.5 mm x 169.9 mm (4.37" x 2.9" x 6.69") |
Control Interface
The laser controller's interface consists of a flat menu hierarchy that makes it easy to find parameters to adjust.
Home Screen in Constant Current Mode | Home Screen in Constant Power Mode | ||
![]() Click to Enlarge | In Constant Current Mode, the home screen emphasizes the laser diode current and temperature and displays their respective setpoints. The output power, measured by the monitor diode, is also displayed. Up to four setpoint combinations can be stored in memory. | ![]() Click to Enlarge | In Constant Power Mode, the home screen emphasizes the laser output power and diode temperature. The laser diode current is also displayed. |
Setpoint Entry | Menu Screen | ||
![]() Click to Enlarge | Each setpoint is easily modified. Simply tap the value to be changed, and buttons appear on the right that allow the value to be set. The current value of the parameter remains displayed while tweaking. | ![]() Click to Enlarge | The CLD1015 is configured through an intuitive two-level menu structure. All settings related to the laser and the thermoelectric cooler are made here, and several other system settings are provided. |
Software for Laser Diode Controllers
The download button below links to VISA VXI pnp™, MS Visual Studio™, MS Visual Studio.net™, LabVIEW™, and LabWindows/CVI™ drivers, firmware, utilities, and support documentation for Thorlabs' ITC4000 Series laser controllers, LDC4000 Series laser controllers, CLD1000 Series compact laser diode controllers, and TED4000 Series TEC controllers.
The software download page also offers programming reference notes for interfacing with compatible controllers using SCPI, LabVIEW, Visual C++, Visual C#, and Visual Basic. Please see the Programming Reference tab on the software download page for more information and download links.
The software packages support LabVIEW 8.5 and higher. If you are using an earlier version of LabVIEW, please contact Technical Support for assistance.
Butterfly Laser Diodes Compatible with the CLD1015
The CLD1015 Laser Diode Driver and Temperature Controller is compatible with Type 1 Pump Laser Diodes and Type 2 Telecom Laser Diodes. Please use the pin diagrams below to verify compatibility with your specific butterfly package. The interior of the CLD1015 is labeled with the correct installation orientation for Type 1 and Type 2 lasers.
Type 1: Pump Laser Diodes
Pin | Connection | Pin | Connection |
---|---|---|---|
1 | TEC+ (Thermoelectric Cooler) | 8 | Monitor Diode Anodea |
2 | Thermistor | 9 | Laser Diode Cathodeb |
3 | Monitor Diode Anodea | 10 | Laser Diode Anode |
4 | Monitor Diode Cathodea | 11 | Laser Diode Cathodeb |
5 | Thermistor | 12 | No Connection |
6 | No Connection | 13 | Ground |
7 | Monitor Diode Cathodea | 14 | TEC- (Thermoelectric Cooler) |
Type 2: Telecom Laser Diodes
Pin | Connection | Pin | Connection |
---|---|---|---|
1 | Thermistor | 8 | Ground |
2 | Thermistor | 9 | Ground |
3 | Laser Diode Cathode | 10 | No Connection |
4 | Monitor Diode Anode | 11 | Laser Diode Anodea |
5 | Monitor Diode Cathode | 12 | No Connection |
6 | TEC+ (Thermoelectric Cooler) | 13 | Laser Diode Anodea |
7 | TEC- (Thermoelectric Cooler) | 14 | No Connection |
PID Basics
The PID circuit is often utilized as a control loop feedback controller and is commonly used for many forms of servo circuits. The letters making up the acronym PID correspond to Proportional (P), Integral (I), and Derivative (D), which represents the three control settings of a PID circuit. The purpose of any servo circuit is to hold the system at a predetermined value (set point) for long periods of time. The PID circuit actively controls the system so as to hold it at the set point by generating an error signal that is essentially the difference between the set point and the current value. The three controls relate to the time-dependent error signal. At its simplest, this can be thought of as follows: Proportional is dependent upon the present error, Integral is dependent upon the accumulation of past error, and Derivative is the prediction of future error. The results of each of the controls are then fed into a weighted sum, which then adjusts the output of the circuit, u(t). This output is fed into a control device, its value is fed back into the circuit, and the process is allowed to actively stabilize the circuit’s output to reach and hold at the set point value. The block diagram below illustrates the action of a PID circuit. One or more of the controls can be utilized in any servo circuit depending on system demand and requirement (i.e., P, I, PI, PD, or PID).
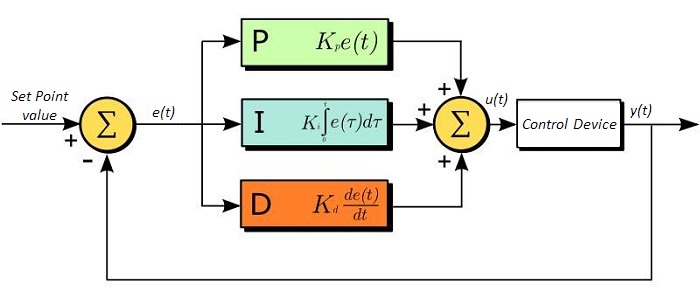
Through proper setting of the controls in a PID circuit, relatively quick response with minimal overshoot (passing the set point value) and ringing (oscillation about the set point value) can be achieved. Let’s take as an example a temperature servo, such as that for temperature stabilization of a laser diode. The PID circuit will ultimately servo the current to a Thermoelectric Cooler (TEC) (often times through control of the gate voltage on an FET). Under this example, the current is referred to as the Manipulated Variable (MV). A thermistor is used to monitor the temperature of the laser diode, and the voltage over the thermistor is used as the Process Variable (PV). The Set Point (SP) voltage is set to correspond to the desired temperature. The error signal, e(t), is then the difference between the SP and PV. A PID controller will generate the error signal and then change the MV to reach the desired result. For example, if e(t) states that the laser diode is too hot, the circuit will allow more current to flow through the TEC (proportional control). Since proportional control is proportional to e(t), it may not cool the laser diode quickly enough. In that event, the circuit will further increase the amount of current through the TEC (integral control) by looking at the previous errors and adjusting the output to reach the desired value. As the SP is reached (e(t) approaches zero), the circuit will decrease the current through the TEC in anticipation of reaching the SP (derivative control).
Please note that a PID circuit will not guarantee optimal control. Improper setting of the PID controls can cause the circuit to oscillate significantly and lead to instability in control. It is up to the user to properly adjust the PID gains to ensure proper performance.
PID Theory
The output of the PID control circuit, u(t), is given as

where
Kp= Proportional Gain
Ki = Integral Gain
Kd = Derivative Gain
e(t) = SP - PV(t)
From here we can define the control units through their mathematical definition and discuss each in a little more detail. Proportional control is proportional to the error signal; as such, it is a direct response to the error signal generated by the circuit:
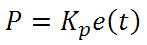
Larger proportional gain results in larger changes in response to the error, and thus affects the speed at which the controller can respond to changes in the system. While a high proportional gain can cause a circuit to respond swiftly, too high a value can cause oscillations about the SP value. Too low a value and the circuit cannot efficiently respond to changes in the system.
Integral control goes a step further than proportional gain, as it is proportional to not just the magnitude of the error signal but also the duration of the error.
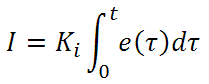
Integral control is highly effective at increasing the response time of a circuit along with eliminating the steady-state error associated with purely proportional control. In essence integral control sums over the previous error, which was not corrected, and then multiplies that error by Ki to produce the integral response. Thus, for even small sustained error, a large aggregated integral response can be realized. However, due to the fast response of integral control, high gain values can cause significant overshoot of the SP value and lead to oscillation and instability. Too low, and the circuit will be significantly slower in responding to changes in the system.
Derivative control attempts to reduce the overshoot and ringing potential from proportional and integral control. It determines how quickly the circuit is changing over time (by looking at the derivative of the error signal) and multiplies it by Kd to produce the derivative response.
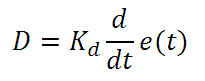
Unlike proportional and integral control, derivative control will slow the response of the circuit. In doing so, it is able to partially compensate for the overshoot as well as damp out any oscillations caused by integral and proportional control. High gain values cause the circuit to respond very slowly and can leave one susceptible to noise and high frequency oscillation (as the circuit becomes too slow to respond quickly). Too low and the circuit is prone to overshooting the SP value. However, in some cases overshooting the SP value by any significant amount must be avoided and thus a higher derivative gain (along with lower proportional gain) can be used. The chart below explains the effects of increasing the gain of any one of the parameters independently.
Parameter Increased | Rise Time | Overshoot | Settling Time | Steady-State Error | Stability |
---|---|---|---|---|---|
Kp | Decrease | Increase | Small Change | Decrease | Degrade |
Ki | Decrease | Increase | Increase | Decrease Significantly | Degrade |
Kd | Minor Decrease | Minor Decrease | Minor Decrease | No Effect | Improve (for small Kd) |
Tuning
In general the gains of P, I, and D will need to be adjusted by the user in order to best servo the system. While there is not a static set of rules for what the values should be for any specific system, following the general procedures should help in tuning a circuit to match one’s system and environment. A PID circuit will typically overshoot the SP value slightly and then quickly damp out to reach the SP value.
Manual tuning of the gain settings is the simplest method for setting the PID controls. However, this procedure is done actively (the PID controller turned on and properly attached to the system) and requires some amount of experience to fully integrate. To tune your PID controller manually, first the integral and derivative gains are set to zero. Increase the proportional gain until you observe oscillation in the output. Your proportional gain should then be set to roughly half this value. After the proportional gain is set, increase the integral gain until any offset is corrected for on a time scale appropriate for your system. If you increase this gain too much, you will observe significant overshoot of the SP value and instability in the circuit. Once the integral gain is set, the derivative gain can then be increased. Derivative gain will reduce overshoot and damp the system quickly to the SP value. If you increase the derivative gain too much, you will see large overshoot (due to the circuit being too slow to respond). By playing with the gain settings, you can maximize the performance of your PID circuit, resulting in a circuit that quickly responds to changes in the system and effectively damps out oscillation about the SP value.
Control Type | Kp | Ki | Kd |
---|---|---|---|
P | 0.50 Ku | - | - |
PI | 0.45 Ku | 1.2 Kp/Pu | - |
PID | 0.60 Ku | 2 Kp/Pu | KpPu/8 |
While manual tuning can be very effective at setting a PID circuit for your specific system, it does require some amount of experience and understanding of PID circuits and response. The Ziegler-Nichols method for PID tuning offers a bit more structured guide to setting PID values. Again, you’ll want to set the integral and derivative gain to zero. Increase the proportional gain until the circuit starts to oscillate. We will call this gain level Ku. The oscillation will have a period of Pu. Gains for various control circuits are then given to the right in the chart.
Note that when using the Ziegler-Nichols tuning method with some devices like the DSC1 digital servo controller, the integral and derivative terms must be normalized by the sample rate. To do this, the integral term determined from the table should be divided by the sample rate in Hertz and the derivative term should be multiplied by the sample rate in Hertz.
Video Insight: Setting Up a Pigtailed Butterfly Laser Diode
A laser diode packaged in a butterfly housing can be precisely controlled, in a compact package, when the laser is installed in a mount such as the CLD1015 that includes thermoelectric cooler (TEC) and current drivers. The mount can make it easier, and safer, to operate the laser, but the procedure for installing the laser in the mount and configuring the settings requires some care. This video provides a step-by-step guide, which begins with an introduction to the different components and concludes with the laser operating under TEC control and with the recommended maximum current limit enabled.
If you would like more information about tips, tricks, and other methods we often use in the lab, we recommend our other Video Insights. In addition, our webinars provide practical and theoretical introductions to our different products.
Posted Comments: | |
user
 (posted 2024-12-04 12:07:37.77) 您好,请问在正常工作状态下,1015型的泵浦突然不出光了,是碟片的问题还是驱动的问题呢,或者说影响的可能性有哪些,应该怎么进行排查? hchow
 (posted 2024-12-05 05:39:10.0) 感谢您联系我们。您当地的技术支持团队成员将直接与您联系以解决您的问题。 Max A
 (posted 2024-09-24 14:06:06.79) Are those CLD1015 compatible with BOA1550P - C-Band Booster Optical Amplifier? fmortaheb
 (posted 2025-03-12 08:45:46.0) Dear Max, Thank you for providing feedback. You can use the CLD1015 with BOA1550P. When using the BOAs with the CLD1015, use the orientation for type 1 pin configurations. D Sahin
 (posted 2024-08-26 10:17:12.48) Hi,
I am using this driver to drive a type-2 butterfly packaged DFB under external modulation and I am observing some exponential dependence on the fall edge of the square pulse. I observed the same issue on the rising edge which I was able to adjust the current to get rid of but I am unable to get rid of the falling edge exponential dependence. It seems to be coming from the driver as whatever frequency I use (500Hz to 1kHz) and various fall edge decay time (0 to 50us), I see the very similar time dependence about ~230 us. Any leads on why I might be seeing that? I already tried enabling. disabling noise reduction filter and has no impact.
Thanks, Dee hkarpenko
 (posted 2024-08-28 10:35:32.0) Dear Dee,
thank you very much for your feedback. Indeed the absolute falltime of the signal can be significantly higher then the rise time. However the 3dB fall and rise times should be in the same range as specified in the data sheet. For troubleshooting I would appreciate if you can share screenshots of your scope with us to have a better understanding of the issue. I will contact you directly to discuss this issue further with you. John Houlihan
 (posted 2024-08-13 16:24:46.857) Hello, my goal is to write custom software for the CLD1015 on a Linux operating system. Do you have Linux drivers that you can provide to me? hkarpenko
 (posted 2024-08-14 09:27:31.0) Dear John,
thank you very much for your feedback.
Unfortunately we don´t support linux and cannot provide drivers for it. Thus you would have to work with windows to operate our laser drivers. You can download them directly on our webpage under the tab "Software". Loïc Laplatine
 (posted 2024-07-09 15:28:58.263) Dear Throlabs Team,
When I change the laser diode current limit, most of the time it is not saved after restarting the CLD1015... Is there a trick to save this safety parameter?
Regards, jjadvani
 (posted 2024-07-10 07:13:57.0) Dear Loic, Thank you for your feedback. I will contact you directly to discuss your issue. Gareth Lees
 (posted 2024-01-16 15:16:40.723) It would be a great addition to this product if it could support 10pin mini butterfly packages. A number of pump lasers manufacturers are using these 10pin mini butterfly packages over the 14pin packages.
If this is already an option please let me know.
Best regards
Gareth dpossin
 (posted 2024-01-17 09:08:07.0) Dear Gareth,
Thank you for your feedback and the expressed suggestions. We will take that into our discussion regarding the successor of the CLD1015. Anna Malekmohamadi
 (posted 2023-11-05 11:05:35.413) Daer Thorlabs,
We have one of your CLD1015 driver that unfortunately does not work properly. The problem is, we insert the diode for the very first time in this driver, and after turning on the device and setting the current limit, when we turn on the "laser on" button, the LD voltage reading amount increases continuously and quickly, that in a second driver turns off the laser and shows an error that laser should be off for protection. Could you please help us to know what is the problem with this device?
Deutsches elektronen synchrotron DESY hkarpenko
 (posted 2023-11-08 08:19:30.0) Dear Anna,
thank you for your request.
This issue can have several reasons and depends on the settings made in the software. I will contact you directly to discuss this further with you. Menachem polak
 (posted 2023-01-16 03:44:53.61) Hello,
we are interested in using the CLD1015 with Photodigm's PH852DBR butterfly pigtailed laser diode. https://www.photodigm.com/products/852-nm-laser-diode
so in terms of electrical interfaces, I checked and
it seems to be fully compatible(please correct me if I'm wrong). In terms of mechanical interface the only slight difference I saw in compares to DBR852PN is that the height of the PH852DBR from its baseplate to the butterfly pins is 5 mm versus the DBR852PN's 5.5 mm. and the second mechanical difference is that the height of the PH852DBR from its baseplate to the center of the waveguide is 4.9 mm versus DBR852PN's 6 mm.
will we have problems mechanically wise or is it okay?
Thanks hchow
 (posted 2023-01-17 07:23:39.0) Dear Mr. Polak, thank you for your feedback. I have taken a look at the webpage you posted, however, I was unable to find the dimensions of the Photodigm's PH852DBR. The pins on the ZIF socket, where the butterfly laser diode goes onto can be depressed slightly, definitely more than the 0.5 mm difference between the DBR852PN and the PH852DBR. Which means, our CLD1015 laser driver should theoretically work with the third party butterfly laser diode, PH852DBR. I will contact you personally to provide more information. Thank you. Zihao Wang
 (posted 2022-11-23 14:33:39.843) Hi there,
We are using the CLD1015 model and would like to use it the drive our laser. The problem is our lasers have two sections that need to apply constant current and reverse biased voltage for each part. We tried to use the MPD pin to provide the voltage but we find one of the MPD pins is connected to the anode of the current source. To make things simple, our laser structure is very similar to EML and do not need the RF signal, just need to provide constant current and voltage. Is that possible to do it in CLD1015 modual? wskopalik
 (posted 2022-11-24 04:31:05.0) Thank you very much for your feedback!
The CLD1015 controllers are designed to operate laser diodes with the type 1 and 2 butterfly packages which are shown in the tab “Pin Diagrams”. For other butterfly diode types, we would need to compare the pin configuration to make sure that the diode is compatible.
I will contact you directly to provide further assistance. Jonas M
 (posted 2022-11-11 12:17:16.3) Can I block the operator from changing Laser Diode Current Limit to make sure laser output power is not exceeding a certain value? dpossin
 (posted 2022-11-11 09:29:55.0) Dear Jonas,
Thank you for your feedback! Unfortunately, there is no such function you are looking for. Aleksey Vasilyev
 (posted 2022-10-14 10:47:23.36) We have the problem of connecting more than 3 CDL1015 controllers to the USB hub at the same time. NI MAX became unresponsive and can not detect them.
We did try to use different hubs but the result is always the same. dpossin
 (posted 2022-10-17 09:14:17.0) Dear Aleksey,
Thank you for your feedback. I am reaching out to you in order to discuss possible solutions. user
 (posted 2022-07-12 21:26:22.843) Can I install ADAFCPM2 mating sleeve on the wall of CLD1015 for fiber coupling purposes? fmortaheb
 (posted 2022-07-14 10:21:11.0) Thank you very much for contacting Thorlabs. Yes, you can mount the ADAFCPM2 on the rear panel. Please check the manual, P.74 (https://www.thorlabs.de/_sd.cfm?fileName=21440-D02.pdf&partNumber=CLD1015). user
 (posted 2022-06-20 19:26:44.497) I want to use DBR780PN diode laser which has PM Fiber Output with 2.0 mm Narrow Key FC/APC Connector, with the CLD1015. After connecting it to the mating sleeve to the back of the mount what type of fibre one should connect at the output optical port of the CLD1015? Should it be FC/PC or FC/APC? GBoedecker
 (posted 2022-06-22 04:47:00.0) Thank you for your inquiry! The CLD1015 has no optical input and output port. You can directly connect the connector of the DBR780PN to your further components. user
 (posted 2022-06-15 23:23:04.28) Which model of fibre optic cable of Thorlabs is suitable for taking optical output from the mount CLD1015? wskopalik
 (posted 2022-06-16 09:17:35.0) Thank you very much for your feedback.
The CLD1015 drivers can be used with different butterfly laser diodes. These diodes usually already have a fiber installed. The fiber type depends on the properties of the diode (e.g. wavelength, polarization).
If you want to attach an additional fiber to the fiber of the diode, you would need to match the properties of the two fibers. This way you can achieve the best coupling efficiency.
Unfortunately, you did not leave any contact details so I cannot contact you directly. Please feel to contact your local Thorlabs tech support so we can help you with selecting the best fiber. user
 (posted 2022-06-15 22:41:16.33) Which model of fibre optic cable of Thorlabs is suitable for taking optical output from the mount? wskopalik
 (posted 2022-06-16 09:18:35.0) Thank you very much for your feedback.
The CLD1015 drivers can be used with different butterfly laser diodes. These diodes usually already have a fiber installed. The fiber type depends on the properties of the diode (e.g. wavelength, polarization).
If you want to attach an additional fiber to the fiber of the diode, you would need to match the properties of the two fibers. This way you can achieve the best coupling efficiency.
Unfortunately, you did not leave any contact details so I cannot contact you directly. Please feel to contact your local Thorlabs tech support so we can help you with selecting the best fiber. user
 (posted 2022-05-18 19:09:49.807) what is the bandwidth of CLD1015 if one wants to operate the butterfly laser diode in constant power mode? dpossin
 (posted 2022-05-20 02:52:52.0) Dear customer,
The modulation bandwidth in constant power mode depends on the fall/rise time of the feedback photodiode in your butterfly laser and the temperature you would like to operate the same at. Therefore we can´t give any specifications on that just for the laser driver. Philip Skochinski
 (posted 2021-10-29 08:01:57.96) Hi,
Is a modification available to drive a DIL packaged laser diode?
Thanks,
Phil soswald
 (posted 2021-11-03 11:56:54.0) Dear Phil,
thank you for your feedback. I have contacted you directly to discuss your application in more detail. Chia-Chi Liu
 (posted 2021-04-29 12:59:55.903) Hi team Thorlabs,
We had purchased several CLD1015 for our butterfly lasers years ago, and things go really well with them.
However, we got a new type 2 butterfly laser recently, which comes with wider pin width (width = 0.75 cm).
Is it possible that we could order an extra ZIF socket (as described in the manual, page 11) with a wider pin sockets?
Thanks! MKiess
 (posted 2021-05-04 10:12:32.0) Dear Chia-Chi Liu, thank you very much for your inquiry.
The manual describes how to install the included ZIF socket to use the CLD1015 with either a type 1 pump laser diode or a type 2 DFB laser diode, starting on page 11. It is not recommended to simply install an arbitrary ZIF Socket.
I have contacted you directly for a possible conversion or corresponding custom designs. Y BoH
 (posted 2020-12-11 21:33:03.507) It would be very useful to have a version with lower current output (300mA to 500mA will be sufficient) and much better current noise and temperature stability performance. People can use that for driving butterfly DBR/DFB laser diodes for high power fiber amplifier seeding purpose. MKiess
 (posted 2020-12-15 06:00:10.0) Thank you very much for this feedback. This helps us to continuously develop and improve our products.
Better temperature stability and current noise can also be achieved with the combination of ITC4001 and the LM14S2 Butterfly Laser Diode Mount. 李 亮
 (posted 2020-12-01 10:24:52.983) I bought a DBR795 laser from your company,now I want to modulate it,make a continuous laser to a pulsed laser,I can't do it,looking forward to your reply. wskopalik
 (posted 2020-12-01 05:52:14.0) Thank you very much for your inquiry!
The CLD1015 has a modulation input on the back which can be used to apply an external modulation signal to the driving current. The modulation signal can e.g. be created using a signal generator. To enable the modulation input, you need to go to the "Laser Driver Setup" menu and enable the input. Depending on the modulation frequency you can also disable the noise reduction filter in this menu.
I will contact you directly to provide further assistance. YJ Hu
 (posted 2020-08-18 17:39:00.47) I want to use constant power mode, it is originally constant current mode. But after I switch to CP mode, both current and power are zero. The laser cannot be turned on. what should I do to set it to CP mode? MKiess
 (posted 2020-08-18 09:08:07.0) Hello, thank you very much for your inquiry. When all parameters, corresponding to your laser diode with integrated photodiode, have been entered in the controller settings, you can easily modify the power set point as desired. For this you have to tap on the value to be changed at the home screen an set the desired value.
I have contacted you directly to discuss further details. user
 (posted 2020-05-28 03:56:54.75) I would like to drive a superluminescent diode (SLD) in constant current mode (NOT constant power) whilst monitoring its PD current (it has a back facet monitor diode). The reason why I want to see the PD current is because it is proportional to the output power of the SLD and also because it indicates if there are backreflections into the SLD. However, in your screenshots of the LCD of the CLD1015 in constant current mode, there is no display of the PD current.
Is there a way to get the LCD to show the PD current ? wskopalik
 (posted 2020-06-02 10:56:23.0) This is a response from Wolfgang at Thorlabs. Thank you very much for your inquiry!
It is possible to display the PD current in constant current mode as well. There is a setting "Use Optical Power for Display" in the "Photodiode Input" menu. If this setting is enabled, you will see the optical power in the display. If it is disabled, you will see the PD current.
I will contact you directly to provide further assistance. Peter Yun
 (posted 2020-05-22 10:47:20.6) What is the maxium smapling rate when I use the remote control to read the temperature displayed by the CLD1015?
Thanks in advance! dpossin
 (posted 2020-06-02 07:57:56.0) Dear Customer! Thank you for your Feedback. In general the sample rate is limited to the maximum usb data transfer speeds and packages. The sample rate of the thermistor temperature depends on the oscillation period set in the PID CONTROL LOOP panel (depends on the used mount) and is calculated by 64 / oscillation period. So for example the maximum sample rate of the TEC temperature is 320 (at an oscillation period of about 0.2 s). Y Yang
 (posted 2020-01-10 11:36:44.853) Can CLD 1015 generate constant current square wave signal by connecting signal generator dpossin
 (posted 2020-01-13 07:13:42.0) Dear Customer,
Thank you for your feedback. The CLD1015 can be modulated externally via square wave signals. Just note that the maximum bandwith in the specification refers to sinusoidal modulation thus, the maximum bandwidth for square waves is around 10% of the specified bandwidth. M10619007
 (posted 2018-12-05 16:30:05.713) I want to know the full width at half maximum of this light source? wskopalik
 (posted 2018-12-06 04:25:03.0) This is a response from Wolfgang at Thorlabs. Thank you very much for your inquiry!
The CLD1015 is only the driver needed to run a laser diode, i.e. it supplies the laser diode and also its TEC element with current. You can install different butterfly laser diodes in the CLD1015, but these are not included. The full width at half maximum e.g. of the emitted spectrum depends on the installed laser diode.
I will contact you directly so we can talk about the laser diode in question. v.t.tenner
 (posted 2018-11-29 16:08:48.963) Does this driver contains a fan? wskopalik
 (posted 2018-12-06 04:12:06.0) This is a response from Wolfgang at Thorlabs. Thank you very much for your inquiry!
Yes, this driver contains a fan to prevent overheating of the components inside.
I will contact you directly to discuss your requirements in further detail. alexey.kokhanovskiy
 (posted 2018-09-19 06:33:17.02) Dear Sir/Mme
1) Is CLD1010LP or CLD1011LP fits TO-56 package? I attached example:
http://www.optilab.com/devices/category/laser_diode/SM_1550_nm_VCSEL_pigtail_with_2.5_Gbps/
2) Is it possible to change a mount for TO package to mount for butterfly package?
With respect,
Alexey Kokhanovskiy nreusch
 (posted 2018-09-21 09:10:59.0) This is a response from Nicola at Thorlabs. Thank you very much for your inquiry. Yes, CLD1010LP and CLD1011LP are suitable for TO-56 packages. Unfortunately, we cannot offer to modify CLD1010LP or CLD1011LP to be compatible with butterfly packages as the changes would be too large. michael.woods
 (posted 2018-05-25 23:34:01.41) Where is the windows based program for controlling this unit over usb? YLohia
 (posted 2018-05-29 09:00:57.0) Hello, unfortunately, we do not currently provide a GUI software for controlling this unit. We do, however, provide drivers and references for controlling this via SCPI commands and LabVIEW/C++/C#/Visual Basic here: https://www.thorlabs.com/software_pages/viewsoftwarepage.cfm?code=4000_Series jsauls
 (posted 2016-03-24 13:30:55.593) It is possible to modulate a laser diode with this controller via the USB connection and the provided LabView driver VI's, bypassing the external SMA modulation input? besembeson
 (posted 2016-03-25 09:35:01.0) Response from Bweh at Thorlabs USA: You may be able to turn the modulation input on or off, but you will not be able to modulate the laser amplitude. This can only be done through the SMA modulation input. With a different controller such as the ITC4001 (http://www.thorlabs.us/newgrouppage9.cfm?objectgroup_id=4052&pn=ITC4001#4054), and suitable mount (http://www.thorlabs.us/navigation.cfm?guide_ID=35), this will be possible. sascha.liehr
 (posted 2015-09-09 11:58:23.017) I like to buy new laser current dirvers and TEC drivers and saw the new CLD1015 system.
My questions is: Is the CLD1015 more stable/precise than an equivalent combination of your LDC220C / TED200C controllers? Did you get any feedabck or have recommendations?
I need to ensure lowest possible temperatue and current drift!
Thank you and best regards
Sascha Liehr shallwig
 (posted 2015-09-11 01:51:35.0) This is a response from Stefan at Thorlabs. Thank you very much for your inquiry. For the CLD1015 we specify for the laser diode current driver an accuracy of ±(0.1% + 500 µA) and a drift (24 hours) <50 µA @ 0 - 10 Hz in Constant Ambient Temperature.
For the TEC driver the accuracy is specified with ±(0.2% + 20 mA) and the temperature stability over 24 hours is typically <0.005 °C.
Please note the temperature control range and thermal stability depend upon the physical parameters of the thermistor and the operating temperature, respectively.
For the Benchtop devices we specify following:
LDC220C:
Accuracy: ±2.0 mA
Drift, 24hours: <2 mA @ 0 - 10 Hz typ., at constant ambient temperature
TED200C:
Accuracy: ±10 mA
Temperature Stability: ? 0.002 °C
So the laser diode current driver part of the CLD1015 provides more stable results than the LDC220C but the built in TEC driver has slightly worse specifications. I will contact you directly to discuss in more detail which devices are more suitable for your application. user
 (posted 2015-02-12 13:32:54.423) CLD1015: Is it possible to modulate optical output power with frequencies up to 20 MHz? The CLD1011LP seems to have this option via a bias tee interface but the CLD1015 seems only to have a modulation input for frequencies in the kHz range. tschalk
 (posted 2015-02-16 12:14:17.0) This is a response from Thomas at Thorlabs. The CLD1015 is not equipped with an additional bias-t like the CLD1010. The laser mount LM14S2 can be used with a bias-t adapter to modulate the diode up to 500MHz. Please contact me at europe@thorlabs.com if you need any further assistance. 1982ariel
 (posted 2015-01-11 12:37:29.643) Thorlabs hello,
Please specify if this is a current source or voltage source
Ariel shallwig
 (posted 2015-01-12 07:00:35.0) This is a response from Stefan at Thorlabs. Thank you very much for your inquiry.The CLD1015 is like all our laser diode controllers a current source. You set the current to a fixed value within the control range and depending on the laser diode (load resistance) the driver sets the compliance voltage automatically. To make sure a laser diode can be driven by a controller the specified operating voltage has to match with the controllers compliance voltage specifications as well as with the current control range. I will contact you directly to discuss your needs in detail. neil.troy
 (posted 2014-03-23 06:16:26.72) Can the display be turned off when controlling remotely? The light from the display will saturate our sensitive measurement. tschalk
 (posted 2014-03-25 12:00:26.0) This is a response from Thomas at Thorlabs. Thank you very much for your inquiry. In the System Settings (described in the manual at section 2.5.9 System Settings) you can enable the Auto Dimming function. After 30 sec the display ceases and reactivates with a touch to the panel. doug
 (posted 2013-02-12 14:40:11.153) The CLD 1015 would be very attractive if I could re-configure the pin-out, and also remove one side of the zero-force pin holder.
I am using a 7-pin butterfly (i.e. one-sided) with a high-speed modulation K-connector on the other side. So, the fixed pin-out of the current product prevents me from using it. jvigroux
 (posted 2012-09-12 13:12:00.0) A reposne from Julien at Thorlabs: Thank you for your feedback! We are really glad we could develop a device that triggered such a positive response! We did put a lot of effort into trying to make this device as versatile as possible as the number of potential applications is very large. The switching noise is indeed the main limitation, which was unfortunately not possible to completely eliminate without compromising the output current. scoleman
 (posted 2012-09-11 11:32:30.0) I have had the opportunity to use this device for several weeks now and I am very pleased with it. The interface is the best I have used on any laser controller (in 15 years in this business) and provides a great deal of confidence-inspiring information, at a glance. Nothing is extraneous, the home "page" is wonderful. Error handling is great, changing pinouts is very convenient, and the current source and TEC controller are very powerful, especially considering the size of the unit. For applications requiring modulation/pulsing the unit has significantly more bandwidth than similar controllers. The versatility of this little unit is really impressive and all of the features are intuitive to access. It was clearly designed by people very familiar with operating lasers in real-world situations.
The only limitation I have encountered with it thus far is that some switching noise is evident when making sensitive (DFB phase noise/RIN) measurements. . .but in my opinion this is a reasonable trade given the amount of current the current source can provide in such a small package. This noise is reduced at increased drive current. Also, FYI the mounting screws are metric and wrenches are provided.
All in all I highly recommend this device. jvigroux
 (posted 2012-09-05 13:07:00.0) A response form Julien at Thorlabs: Thank you for your feedback! We did try to create device that was at the same time as versatile and easy to use as possible as well as compact, which might lead to the impression that the display is cluttered when one only sees screenshots. We will address this point and replace the pictures in order to give a more accurate feeling about the ease of use of the CLD1015, as Sean already wrote. We would also be happy to send you a loan unit so that you can try it out and hopefully change your mind about the ease of use of this device. sharrell
 (posted 2012-09-05 10:25:00.0) Response from Sean at Thorlabs: Thank you for taking the time to share your thoughts on our new butterfly laser diode mount and controller. Based on your feedback, we will be taking new photos of the device which will better show its intended function. This device was created after many discussions with customers who were looking for a compact, easy-to-use unit with advanced control features not available on our other mounts. cbrideau
 (posted 2012-09-04 14:29:43.0) When I saw the picture for this I thought Thor was selling a kitchen scale. The screen seems overly complex compared to a simple temperature and current readout and a couple knobs but I suppose there are applications where you want to be able to set every tiny detail relatively quickly. |
Laser Diode Controller Selection Guide
Tables 137A and 137B are designed to give a quick overview of the key specifications for our laser diode controllers and dual diode/temperature controllers. For more details and specifications, or to order a specific item, click on the appropriate item number below.
Table 137A Current Controllers | ||||||
---|---|---|---|---|---|---|
Item # | Drive Current | Compliance Voltage | Constant Current | Constant Power | Modulation | Package |
LDC200CV | 20 mA | 6 V | ![]() |
![]() |
External | Benchtop |
VLDC002 | 25 mA | 5 V | ![]() |
- | Int/Ext | OEM |
LDC201CU | 100 mA | 5 V | ![]() |
![]() |
External | Benchtop |
LD2000R | 100 mA | 3.5 V | - | ![]() |
External | OEM |
EK2000 | 100 mA | 3.5 V | - | ![]() |
External | OEM |
LDC202C | 200 mA | 10 V | ![]() |
![]() |
External | Benchtop |
KLD101 | 230 mA | ≤10 V | ![]() |
![]() |
External | K-Cube® |
IP250-BV | 250 mA | 8 Va | ![]() |
![]() |
External | OEM |
LD1100 | 250 mA | 6.5 Va | - | ![]() |
-- | OEM |
LD1101 | 250 mA | 6.5 Va | - | ![]() |
-- | OEM |
EK1101 | 250 mA | 6.5 Va | - | ![]() |
-- | OEM |
EK1102 | 250 mA | 6.5 Va | - | ![]() |
-- | OEM |
LD1255R | 250 mA | 3.3 V | ![]() |
- | External | OEM |
LDC205C | 500 mA | 10 V | ![]() |
![]() |
External | Benchtop |
IP500 | 500 mA | 3 V | ![]() |
![]() |
External | OEM |
LDC210C | 1 A | 10 V | ![]() |
![]() |
External | Benchtop |
LDC220C | 2 A | 4 V | ![]() |
![]() |
External | Benchtop |
LD3000R | 2.5 A | -- | ![]() |
- | External | OEM |
LDC240C | 4 A | 5 V | ![]() |
![]() |
External | Benchtop |
LDC4005 | 5 A | 12 V | ![]() |
![]() |
Int/Ext | Benchtop |
LDC4020 | 20 A | 11 V | ![]() |
![]() |
Int/Ext | Benchtop |
Table 137B Dual Temperature and Current Controllers | |||||||
---|---|---|---|---|---|---|---|
Item # | Drive Current | Compliance Voltage | TEC Power (Max) | Constant Current | Constant Power | Modulation | Package |
VITC002 | 25 mA | 5 V | >2 W | ![]() |
- | Int/Ext | OEM |
ITC102 | 200 mA | >4 V | 12 W | ![]() |
![]() |
Ext | OEM |
ITC110 | 1 A | >4 V | 12 W | ![]() |
![]() |
Ext | OEM |
ITC4001 | 1 A | 11 V | >96 W | ![]() |
![]() |
Int/Ext | Benchtop |
CLD1010LPa | 1.0 A | >8 V | >14.1 W | ![]() |
![]() |
Ext | Benchtop |
CLD1011LPb | 1.0 A | >8 V | >14.1 W | ![]() |
![]() |
Ext | Benchtop |
CLD1015c | 1.5 A | >4 V | >14.1 W | ![]() |
![]() |
Ext | Benchtop |
ITC4002QCLd | 2 A | 17 V | >225 W | ![]() |
![]() |
Int/Ext | Benchtop |
ITC133 | 3 A | >4 V | 18 W | ![]() |
![]() |
Ext | OEM |
ITC4005 | 5 A | 12 V | >225 W | ![]() |
![]() |
Int/Ext | Benchtop |
ITC4005QCLd | 5 A | 20 V | >225 W | ![]() |
![]() |
Int/Ext | Benchtop |
ITC4020 | 20 A | 11 V | >225 W | ![]() |
![]() |
Int/Ext | Benchtop |
We also offer a variety of OEM and rack-mounted laser diode current & temperature controllers (OEM Modules, PRO8 Current Control Rack Modules, and PRO8 Current and Temperature Control Rack Modules).