Precision Constant Current Laser Drivers
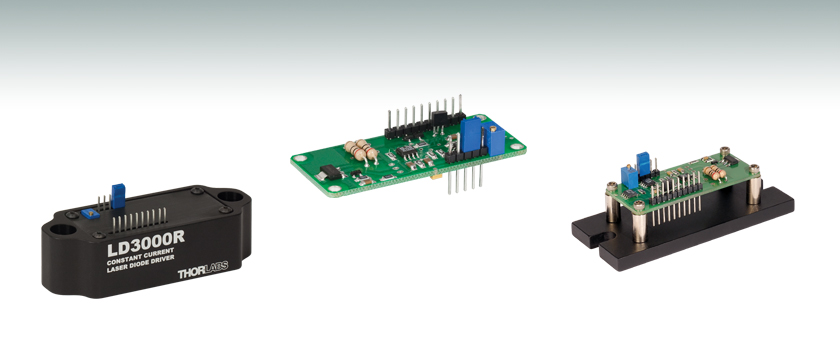
- Zener & Schottky Diode Protection
- 250 mA and 2.5 A Versions
- RoHS Compliant Drivers Available
LD3000R
LD1255R
Application Idea
LD1255R
Mounted on an LD1255P
(Power Supply Not Included)

Please Wait
Item # | LD1255R | LD3000R |
---|---|---|
Operating Current | 0.2 to 250 mA | 0.02 to 2.5 A |
Operating Mode | Constant Current | |
Internal Current Control | 12 Turn Potentiometer (On Board) | |
External Current Control | 0 to 5 Volt Analog Input Voltage | |
Operating Voltage | ±8 to 12 Volts | |
Monitor Photodiode Transimpedance Gain |
1000 V/A |
The LD1255R (250 mA) is a low-noise, highly-stable, constant-current laser diode driver. The LD3000R is a higher-power (2.5 A) version of the LD1255R. These laser drivers are also recommended for driving LEDs. Both laser current drivers fully support the A, D, and E pin configurations (shown in Figures 1.1, 1.2, and 1.3).
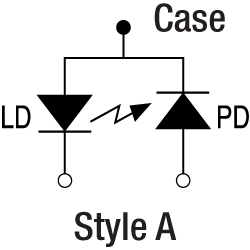
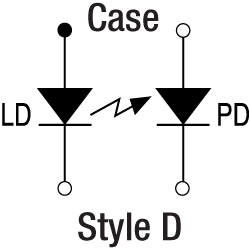
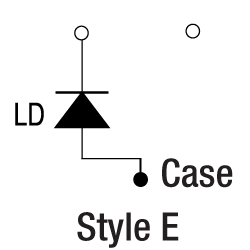
Note: The photodiode monitor circuits of the LD1255R and LD3000R only support lasers that have an isolated photodiode anode (i.e. the photodiode cathode connected to the laser anode). They will not work with common cathode lasers. CONNECTING THE PHOTODIODE OF THESE LASERS TO THE LD1255R or LD3000R WILL DESTROY THE LASER. The LD1255R and LD3000R will operate the laser portion of all common cathode lasers without any problems as long as the photodiode anode is not connected to the driver.
Item # | LD1255R |
---|---|
Operating Current | 0.2 to 250 mA |
Operating Mode | Constant Current |
Internal Current Control | 12 Turn Potentiometer (On Board) |
External Current Control | 0 to 5 V Analog Input Voltage |
Output Current Drift | 4.4 μA/°C (Typical) |
Current Noise | <1 μARMS |
Operating Voltage | ±8 to 12 V |
Dimensions | 2.45" x 1.03" (62.2 mm x 25.4 mm) |
LD ESD Protection | Forward Voltage: 160 ms Slow-Start Circuit, 3.3 V Zener Diode, Reverse Voltage: Schottky Diode, LD DISABLE Pin |
Signal Bandwidth | 1.2 kHz |
Monitor Photodiode | |
Transimpedance Gain | 1000 V/A |
Max LD Forward Voltage | 3.3 V |
Operating Temperature | 10 to 30 °C |
Storage Temperature | -20 to 50 °C |
Warm-up Time | 30 Minutes |
Item # | LD3000R |
---|---|
Operating Current | 0.02 to 2.5 A |
Operating Mode | Constant Current |
Internal Current Control | 12 Turn Potentiometer (On Board) |
External Current Control | 0 to 5 V Analog Input Voltage |
Operating Voltage | ±8 to 12 V |
Dimensions | 3.6" x 1.3" (91.4 mm x 33.0 mm) |
Monitor Photodiode | |
Transimpedance Gain | 1000 V/A |
Operating Temperature | 10 to 30 °C |
Storage Temperature | -20 to 50 °C |
Warm-up Time | 30 Minutes |
LD1255R Top View
LD3000R Top View
LD1255R Pin Designations
Pin | Function |
---|---|
J1-1 | +V (+8 to +12 VDC, 10 mA) |
J1-2 | Common |
J1-3 | -V (-8 to -12 VDC, 0.3A) Provides Power to Laser |
J1-4 | External Current Control (0 to +5 V) |
J1-5 | Disable |
J1-6 | Laser Diode Anode |
J1-7 | Laser Diode Cathode |
J1-8 | Monitor Photo Diode Anode (From Laser)a |
J1-9 | Photodiode Monitor Output (-1 V/mA) |
J1-10 | Laser Current Monitor Output (10 mV/mA) |
LD3000R Pin Designations
Pin | Function |
---|---|
J1-1 | +V (+5 to +12 VDC, 50 mA) |
J1-2 | Ground |
J1-3 | -V (-8 to -12 VDC, 2.5A) Provides Power to Laser |
J1-4 | External Current Control (0 to +5 V) |
J1-5 | No Contact (Polarization Key) |
J1-6 | Laser Diode Anode (Internally Connected to Pin 2 Ground) |
J1-7 | Laser Diode Cathode |
J1-8 | Monitor Photo Diode Anode (From Laser)a |
J1-9 | Photodiode Monitor Output (-1 V/mA) |
J1-10 | Laser Current Monitor Output (1 V/A) |
J2 Pins to Jumper | Operating Mode |
---|---|
1 to 2 | Mode 1. COMMON Referenced External Current Control |
2 to 3 | Mode 2. Disable External Current Control |
J2 Pins to Jumper | Operating Mode |
---|---|
2 to 3 | Mode 1. COMMON Referenced External Current Control |
4 to 5 | Mode 2. Disable External Current Control |
IMPORTANT! Do not operate the LD3000R without a jumper installed on J2. Your laser may be overdriven and permanently damaged.
Remaining J2 Pins | Function |
---|---|
1 | No Connection (Leave This Pin Floating) |
5 | -V (May Also Be Used for Monitoring Signals) |
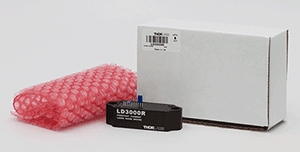
Click to Enlarge
Figure 4.1 LD3000R Packaging
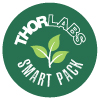
Smart Pack
- Reduce Weight of Packaging
- Increase Usage of Recyclable Materials
- Improve Packing Integrity
- Decrease Shipping Costs
Thorlabs' Smart Pack Initiative is aimed at minimizing waste while providing adequate protection for our products. By eliminating any unnecessary packaging, implementing design changes, and utilizing eco-friendly materials, this initiative seeks to reduce the environmental impact of our product packaging.
The updated LD3000R packaging primarily consists of recycled paper and cardboard and weighs 15.26% less than the original packaging. This weight change results in a 1.32 kg reduction in travel-based CO2 emissions per year, based on typical product sales.
As we move through our product line, we will indicate re-engineered, eco-friendly packaging with our Smart Pack logo.
Posted Comments: | |
Nick Cox
 (posted 2024-08-28 15:01:42.423) Hi,
Can you provide more detail on how to wire the LD3000R for driving an LED? I don't understand why the anode (pin 6) is tied to GND.
Thanks. ksosnowski
 (posted 2024-09-04 03:36:14.0) Hello Nick, thanks for reaching out to us. Many laser diodes and LEDs have one of the pins common with the case of the laser. Since mounting the laser often grounds the case of the device, this limits the drive current polarity choice that can be used in some devices. LD3000R can only apply an anode-grounded drive polarity, where it acts as a negative current source at the cathode pin, in order to pull forward current across the diode. Some diodes have their driving pins isolated from the case, in which case either style of driver (cathode- or anode-grounded) can be used as long as the drive pins are connected properly. It is recommended to check the specifications of the diode to see if either the anode or cathode pins are connected to the case. This is commonly denoted as a filled-in circle on the circuit diagram and an open circle commonly denotes a connection point that is isolated from the case. I have reached out directly to discuss this further. user
 (posted 2023-03-28 13:09:00.473) Can I use a connection (relay, limit switch) across J2 pins 4 and 5 to get a 'disable' function with the LD3000R, when using the external current control? ksosnowski
 (posted 2023-04-06 05:11:35.0) Thanks for reaching out to Thorlabs. Unfortunately the LD3000R does not have a full disable function built in. It is not recommended to operate the LD3000R without a jumper on the J2 header to set the control mode. If using a relay to disconnect like mentioned, then in the open state your J2 would have no jumper, which may result in unintentional overdriving of the laser. Note that in external current mode, the total current is the sum of the external current command as well as the potentiometer set current, so it is possible in theory to disable the external control and leave the laser still active. A relay on the negative power line could serve to disable power to the board's laser power since the positive line is used only for biasing a photodiode if connected. Lee Weller
 (posted 2022-12-06 09:07:59.133) Is it possible to run a type C laser diode with the LD1255R. Do I just need to unplug the +12V and photodiode pin or is there anything else I need to disconnect or connect? ksosnowski
 (posted 2022-12-09 02:30:40.0) Thanks for reaching out to Thorlabs. LD1255R is designed for pin styles A, D, and E, all of which feature an Anode grounded laser diode and (for style A/D) an isolated photodiode anode. With a C style laser, you cannot connect the photodiode to the monitor circuit, or it will break the laser, however you can still power the laser portion. The power to LD1255R should be supplied in the same method as normal. This will be similar to running the laser as an E-style diode. Ludo Angot
 (posted 2020-08-19 00:49:32.627) I have a couple of additional questions, this time regarding specifically the LD3000R. 1) is there a disable pin and function as on the LD1255R? If so how to use it? And if not, what is the function of pin 5 on J1 (it's not documented in the user manual)? 2) I've noticed negative transient currents down to -100mA when shutting off the power supply to the LD3000R (using your EC5PS P.S. module) and up to 90mA when interrupting the current on the +/-12V pins on the LD3000R itself, these could damage the L.D. How do you recommend to switch off the driver in order to avoid the transient currents? 3) finally: if my L.D. doesn't include a photodiode or if it does but I don't need it, can the LD3000R be operated with only the negative 12V applied? Or asked in another way, what are the low-power amplifiers (those requiring the +12V bias) used for? asundararaj
 (posted 2020-10-30 08:22:59.0) Thank you for contacting Thorlabs. The LD3000R does not have a disable circuit like the LD1255R. The LD3000R is a similar circuit and PCB as the LD1255 with a few changes in the drive transistor and current set resistor to accommodate the higher current drive.
It can be operated with the +12V removed however, this will disable the photodiode monitor and external control. If using the onboard pot to adjust current you should be OK. Also note that a floating power supply should be used (i.e. a supply that is not referenced to earth ground) since the drive transistor is directly mounted to the case. The case is anodized and generally is a good insulator unless there is a break in the finish (common at mounting screw point). Ludovic Angot
 (posted 2020-08-14 04:47:41.6) What problem may I face when driving a G pin code LD with either one of these drivers? I've just tried with the LD1255R and it seems to work just fine. Also, on the user manual of the LD1255R, does the figure 2 (Disable Circuit Schematic) refer to the actual internal circuit of the driver or is it a suggestion for an external customer made disable circuit? asundararaj
 (posted 2020-08-26 04:18:09.0) Thank you for contacting Thorlabs. The LD1255R can operate any laser diode as long as it can be wired correctly. It uses a floating power supply when the case is held at a potential other than GND. It does not require the PD for operation since it is a constant current controller without a power feedback loop. There is a PD monitor but it is not required for operation. lmarin
 (posted 2015-09-28 14:20:47.867) IS CONFUSING
Laser Current Monitor:
The laser drive current can be monitored from pin 10 of J1. This output is referenced to the negative supply (J1
Pin 3 or J2 Pin 4) and has the following transfer function:
VPIN10 = -V + ILD * 10
Hint: Using a DVM, the laser current can be read without having to compensate for the -V offset by attaching the
(-) lead to J2 Pin 4 and the (+) lead to J1 Pin 10. jlow
 (posted 2015-10-01 04:47:39.0) Response from Jeremy at Thorlabs: The test point outputs are voltage outputs. Using a voltmeter, a simple to read the output current is to connect the (+) lead to J1 Pin 10 and the (-) lead to J2 Pin 4 and measure the voltage between those two pins. The conversion is 10mV/mA. lmarin
 (posted 2015-09-28 13:23:44.05) I am measuring LED current via pin 10 and pin 4 with DVM, what formula I need to use. Is a direct reading volts to amperes?? user
 (posted 2014-12-08 15:31:19.617) There is a typo in the autocad drawing of the LD1255R. It says "all header posts 0.25" square" but that should probably be 0.025" instead. myanakas
 (posted 2014-12-08 05:12:32.0) Response from Mike at Thorlabs: Thank you for your feedback. You are correct, the dimension should be 0.025" square. We are currently working on updating the support drawing. iain
 (posted 2013-11-01 05:51:17.01) Can the LD1255R be battery-operated? For example, with a pair of lead-acid batteries. cdaly
 (posted 2013-11-07 03:10:11.0) Response from Chris at Thorlabs: As long as you hook up a voltage supply to the J1 connector such that pin 1 is 8-12 volts higher in potential than the pin 2 ground and pin 3 is 8-12 volts lower in potential than the pin 2 ground, it does not really matter what the voltage supply is. As long as it can provide a minmimum of 10mA at these voltages, batteries would be fine. jlow
 (posted 2012-10-10 16:51:00.0) Response from Jeremy at Thorlabs: The LD3000 does not support the TTL feature you mentioned. For a similar OEM driver with at least 2.5A output, maybe the ITC133 (http://www.thorlabs.com/NewGroupPage9.cfm?objectgroup_id=984) might be of more interest to you. I will get in contact with you to discuss about your application. ntrail
 (posted 2012-10-06 10:33:47.0) Hello- Following up on the last comment about TTL, I read the instrution manual but am after a bit more clarification. I would like to have the internal pentiometer to set the current output, and then use the external 0-5V source to turn that current "on" to "off", or pulse it. Will the LD3000 support that type of functionality? I ask this, as it mentions the current can be controlled by the external voltage, but I didn't want the exact voltage to set the current, just to turn it on / off. Thank you. jlow
 (posted 2012-10-04 09:12:00.0) Response from Jeremy at Thorlabs: The current output can be externally controlled by a voltage source applied to J1 pin 4. For example, you could use a DAQ card output (0 to +5V) to do that. Please refer to page 3 of the manual (http://www.thorlabs.com/Thorcat/16500/LD3000R-SpecSheet.pdf) for full details on this feature. Your voltage source would have to be triggered by your camera. sebastien.avila
 (posted 2012-10-04 05:53:00.0) Hello,
How can we pulse the current of the LD3000R?
We want to trigger the laser diode synchronous to a camera @ 100fps (100µs to 3ms pulse time).
Is there a TTL "enable" input?
Thank you very much. tcohen
 (posted 2012-05-10 13:03:00.0) Response from Tim at Thorlabs: Thank you for your feedback! The LD1255R can be used with common cathode diodes as long as the photodiode is not connected. This may work if you are interested in using constant current mode. We also offer the IP250-BV that accommodates common cathode pin-outs and is capable of utilizing the photodiode for both constant current and constant power mode. The IP250-BV also supports analog modulation. amiller
 (posted 2012-05-09 13:32:15.0) Hi,
It would be useful to have a version of the controllers, e.g. the LD1225 for grounded cathode laser diodes. Many antimonide diodes have the polarity reversed, making the use of the existing LD1255 challenging for these devices. A separate current modulation input would also be a nice feature. Thanks. bdada
 (posted 2012-02-24 18:37:00.0) Response from Buki at Thorlabs to przeszla:
LD1255 should have sufficiently low current noise to be considered suitable for a DFB laser diode. However, you have to to be very careful to use the instructions in the manual, as it is not difficult to damage the LD if something is overlooked. For expensive laser diodes we recommend using a more turnkey current controller like the LDC201CU.
We have contacted you to provide more information. przeszla
 (posted 2011-10-28 08:27:47.0) Can I use the LD1255 to drive a DFB-Laser (distributed feedback laser) with a specified linewidth < 2MHz? Another manufactor of diode drivers offers an expensive driver with a similar noise and ripple of 2µA, but you have to use another electrical low-noise filter in order to drive the diode. leichner
 (posted 2009-10-19 11:05:56.0) A response from Lou at Thorlabs to tom.hawkins: There is nothing you can do to add additional voltage. The 3.3V is actually the compliance voltage that the driver is regulated to be able to handle. The actual forward voltage is developed by the device, your LED.
If the LED develops a higher forward voltage then you need a different driver. A recommend driver would be the IP250-BV which has a compliance voltage to 8VDC.
http://www.thorlabs.com/NewGroupPage9.cfm?ObjectGroup_ID=1363&pn=IP250-BV&CFID=6061011&CFTOKEN=5737989
The LED may work with the LD1255R but the output will be significantly lower. (LEDs are much more forgiving then laser diodes) tom.hawkins
 (posted 2009-10-19 08:17:49.0) I understand that this product can be used to drive LEDs as well as laser diodes, but what if the forward voltage of the LED is more than 3.3 V? Is there something I could do with an external voltage reference or negative supply rail to extend the drive voltage range? |
Laser Diode Controller Selection Guide
Tables 137A and 137B are designed to give a quick overview of the key specifications for our laser diode controllers and dual diode/temperature controllers. For more details and specifications, or to order a specific item, click on the appropriate item number below.
Table 137A Current Controllers | ||||||
---|---|---|---|---|---|---|
Item # | Drive Current | Compliance Voltage | Constant Current | Constant Power | Modulation | Package |
LDC200CV | 20 mA | 6 V | ![]() |
![]() |
External | Benchtop |
VLDC002 | 25 mA | 5 V | ![]() |
- | Int/Ext | OEM |
LDC201CU | 100 mA | 5 V | ![]() |
![]() |
External | Benchtop |
LD2000R | 100 mA | 3.5 V | - | ![]() |
External | OEM |
EK2000 | 100 mA | 3.5 V | - | ![]() |
External | OEM |
LDC202C | 200 mA | 10 V | ![]() |
![]() |
External | Benchtop |
KLD101 | 230 mA | ≤10 V | ![]() |
![]() |
External | K-Cube® |
IP250-BV | 250 mA | 8 Va | ![]() |
![]() |
External | OEM |
LD1100 | 250 mA | 6.5 Va | - | ![]() |
-- | OEM |
LD1101 | 250 mA | 6.5 Va | - | ![]() |
-- | OEM |
EK1101 | 250 mA | 6.5 Va | - | ![]() |
-- | OEM |
EK1102 | 250 mA | 6.5 Va | - | ![]() |
-- | OEM |
LD1255R | 250 mA | 3.3 V | ![]() |
- | External | OEM |
LDC205C | 500 mA | 10 V | ![]() |
![]() |
External | Benchtop |
IP500 | 500 mA | 3 V | ![]() |
![]() |
External | OEM |
LDC210C | 1 A | 10 V | ![]() |
![]() |
External | Benchtop |
LDC220C | 2 A | 4 V | ![]() |
![]() |
External | Benchtop |
LD3000R | 2.5 A | -- | ![]() |
- | External | OEM |
LDC240C | 4 A | 5 V | ![]() |
![]() |
External | Benchtop |
LDC4005 | 5 A | 12 V | ![]() |
![]() |
Int/Ext | Benchtop |
LDC4020 | 20 A | 11 V | ![]() |
![]() |
Int/Ext | Benchtop |
Table 137B Dual Temperature and Current Controllers | |||||||
---|---|---|---|---|---|---|---|
Item # | Drive Current | Compliance Voltage | TEC Power (Max) | Constant Current | Constant Power | Modulation | Package |
VITC002 | 25 mA | 5 V | >2 W | ![]() |
- | Int/Ext | OEM |
ITC102 | 200 mA | >4 V | 12 W | ![]() |
![]() |
Ext | OEM |
ITC110 | 1 A | >4 V | 12 W | ![]() |
![]() |
Ext | OEM |
ITC4001 | 1 A | 11 V | >96 W | ![]() |
![]() |
Int/Ext | Benchtop |
CLD1010LPa | 1.0 A | >8 V | >14.1 W | ![]() |
![]() |
Ext | Benchtop |
CLD1011LPb | 1.0 A | >8 V | >14.1 W | ![]() |
![]() |
Ext | Benchtop |
CLD1015c | 1.5 A | >4 V | >14.1 W | ![]() |
![]() |
Ext | Benchtop |
ITC4002QCLd | 2 A | 17 V | >225 W | ![]() |
![]() |
Int/Ext | Benchtop |
ITC133 | 3 A | >4 V | 18 W | ![]() |
![]() |
Ext | OEM |
ITC4005 | 5 A | 12 V | >225 W | ![]() |
![]() |
Int/Ext | Benchtop |
ITC4005QCLd | 5 A | 20 V | >225 W | ![]() |
![]() |
Int/Ext | Benchtop |
ITC4020 | 20 A | 11 V | >225 W | ![]() |
![]() |
Int/Ext | Benchtop |
We also offer a variety of OEM and rack-mounted laser diode current & temperature controllers (OEM Modules, PRO8 Current Control Rack Modules, and PRO8 Current and Temperature Control Rack Modules).

- Laser Disable Pin
- Slow-Start Circuit for Laser Protection
- LD1255P Allows Mounting to an Optical Table or Breadboard
- Size: 2.45" x 1.03" (62.2 mm x 25.4 mm)
- RoHS-Compliant
- Low Current Noise (<1 μARMS)
- Low Temperature Drift
- On-Board 12-Turn Laser Current Control
- External Input for Laser Current Control
- Monitor Output for Laser Current and Photodiode Current
The LD1255R is a low-noise, ultra-stable, constant-current laser diode driver. It supplies up to 250 mA of drive current, supports laser pin configurations A, D, and E, and is ideally suited for demanding diode laser applications such as operating a laser diode in an external cavity tunable laser. This second-generation laser diode driver includes on-board Zener and Schottky diode protection as well as a disable pin. The op-amp and voltage reference design enables more precise laser current control. The LD1255P Mounting Plate, which features 8-32 and M4 taps for post mounting, allows the LD1255R to be secured to a breadboard or optical table. A power supply and cable compatible with the LD1255R laser diode driver are also offered separately below.

- Low Noise 2.5 A Drive Current
- Slow-Start Circuit for Laser Protection
- RoHS-Compliant
- Low Noise 12 µARMS at 1.0 A
- On-Board 12-Turn Potentiometer Current Control
- External Input for Current Control
- Monitor Outputs for Diode and Photodiode Current
The LD3000R driver is a higher-power version of Thorlabs' popular LD1255R ultra-stable, low-noise laser diode driver featured above. It utilizes high-current components, supplies 2.5 A, and supports pin configurations A, D, and E. The aluminum housing allows additional heat sinking, which results in a highly stable laser diode driver in a relatively small package. This device can operate both LEDs and laser diodes.

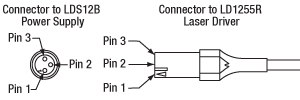
Click to Enlarge
Pin Diagram for the Included Cable
Pin # | Assignment |
---|---|
1 | +12 V |
2 | GND |
3 | -12 V |
- Power Supply (Item # LDS12B) and Cable for Use with the
LD1255R Driver - 3 Pin Cable Output Connects to Driver
- ±12 VDC Output
- Switchable Input Voltage: 100 V, 120 V, or 230 V
The LD1255-SUPPLY Bundle includes the LDS12B Power Supply and the appropriate cable to connect to the LD1255R Laser Diode Driver (available above). A switch on the power supply box enables the user to choose a 100 V, 120 V, or 230 V input voltage. The cable is able to transmit ±12 VDC from the power supply to the LD1255R laser diode driver; it is not compatible with the LD3000R Laser Diode Driver. The included cable can be ordered separately from the power supply by contacting Tech Support.