Optical Tables, 460 mm (18.1") Thick
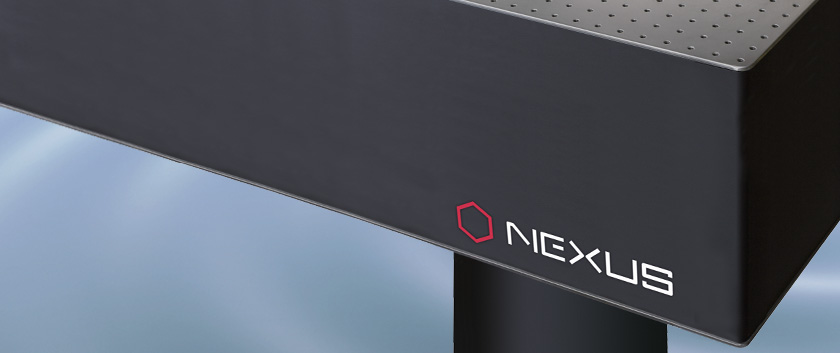
- 460 mm (18.1") Thickness
- Superior Flatness, Compliance, and Construction Quality
- Machined Matte Finish with Holes to Edge of Table
- Each Table Individually Tested
(Table Legs Not Included)

Please Wait
Features
- Thickness: 460 mm (18.1")
- Sizes from 4' x 6' (1.2 m x 2 m) to 4.8' x 14' (1.5 m x 4 m) Available
- Every Table Individually Optimized, Tested, and Shipped with Test Data Certificate
- 1/2" (12.5 mm) Hole Border for Maximum Usable Area
- Top Skin: ±0.1 mm (±0.004") Surface Flatness over any 1 m² (11 ft²) Area
- 5 mm Stainless Steel Top and Bottom Skins with All-Steel Side Panels
- Steel-to-Steel Bonding Throughout Increases Thermal Stability
- For Use with Earthquake Restraints, Custom Order a Modified Table (Contact Tech Support)
Nexus® Optical Tables and Breadboards
One High Quality Level
Nexus is a single high-quality grade of tables and breadboards manufactured in various sizes by Thorlabs. They are suitable for photonics, imaging, and microscopy applications. Each size is individually optimized, and each table ships with a unique test data certificate. See the Table Vibration Isolation and Construction tabs for more details.
Thorlabs' 460 mm (18.1") thick Nexus® Optical Tables are offered in a variety of lengths and widths from 4' x 6' (1.2 m x 2 m) to 4.8' x 14' (1.5 m x 4 m). They feature all-steel construction, excellent thermal stability, and broadband damping optimized for each table size. The 5 mm thick stainless steel top and bottom skins have a matte finish and the top skin is precision-machined with a surface flatness of ±0.1 mm over any 1 m2 area. The table has 1/4"-20 (M6) mounting holes on 1" (25 mm) centers with a 1/2" (12.5 mm) border at the edge of the table.
The sizes listed on this page are built to order and typically available to ship from our UK facility within 4 - 6 weeks of order placement. Custom sizes and options are also available upon request by contacting technical support or filling out our custom optical tables form.
Support Options
Our optical tables require isolating supports (sold separately). We offer rigid table legs as well as legs with either active or passive isolators. Earthquake restraints for lab safety in earthquake zones and a selection of other optical table accessories are also available.
Please note: All tables require modification to accept earthquake restraints prior to shipment. Please contact Tech Support to order an optical table equipped with the necessary alterations. Tables, once they are manufactured and shipped, cannot be retrofitted to accept earthquake restraints.
Nexus Optical Tables Selection Guide | |
---|---|
All Nexus Breadboards | |
Optical Table and Leg Kits | |
210 mm (8.3") Thick Tables | |
Unsealed Mounting Holes | Sealed Mounting Holes |
Two Through Ports | 304L Non-Magnetic Steel |
310 mm (12.2") Thick Tables | |
Unsealed Mounting Holes | Sealed Mounting Holes |
460 mm (18.1") Thick Tables | |
Unsealed Mounting Holes | Sealed Mounting Holes |
Specifications | ||
---|---|---|
Construction | ||
Table Thickness | 460 mm (18.1") | |
Flatness of Top Skin | ±0.1 mm (±0.004") Over Any 1 m2 | |
Construction | Symmetrical Isotropic Construction in All Axes | |
Top and Bottom Plates | 5 mm (0.20") Thick Ferromagnetic Stainless Steel | |
Core Construction | High-Density Plated Steel Honeycomb, 0.26 mm Thick | |
Damping | Proprietary Optimized Broadband Damping | |
Side Panels | Rigid Steel Box Section | |
Side Trim Finish | Matte Black Linoleum, 2 mm Inset from Table Surface | |
Top Surface Finish | Machined Matte Finish | |
Compatible Mounting Legs | Rigid Legs, Passive Isolators, Active Isolators | |
Mounting Holes | Imperial | Metric |
Threads and Spacing | 1/4"-20 Tapped Holes on 1" Centers | M6 Tapped Holes on 25 mm Centers |
Distance from Edge to First Holes | 0.5" from Table Edge on all Sides | 12.5 mm from Table Edge on all Sides |
Maximum Screw Depth | 455 mm (23.5 mm for Outer Border Holes) | |
Performancea | ||
Maximum Dynamic Deflection Coefficientb | <0.4 x 10-3 | |
Maximum Relative Tabletop Motionb | <0.14 nm (5.5 x 10-9 in.) | |
Deflection Under Load (Stiffness)b | <1.7 μm for a 150 kg (330 lb) Load |
Imperial Table Dimensions & Weight
Item # | Dimensions (W x L x H) |
Unpacked Weight |
Packed Weight |
Packed Dimensions |
---|---|---|---|---|
T46K | 4' x 6' x 18.1" | 1018.98 lbs | 1316.60 lbs | 4.5' x 6.3' x 30" |
T48K | 4' x 8' x 18.1" | 1316.82 lbs | 1684.99 lbs | 4.5' x 8.3' x 30" |
T58K | 4.8' x 8' x 18.1" | 1557.56 lbs | 1954.40 lbs | 5.2' x 8.3' x 30" |
T510K | 4.8' x 10' x 18.1" | 1903.25 lbs | 2358.95 lbs | 5.6' x 10.5' x 30" |
T514K | 4.8' x 14' x 18.1" | 2738.14 lbs | 3399.53 lbs | 5.6' x 14.5' x 30" |
Metric Table Dimensions & Mass
Item # | Dimensions (W x L x H) |
Unpacked Mass |
Packed Mass |
Packed Dimensions |
---|---|---|---|---|
T1220E | 1.2 m x 2 m x 460 mm | 496.90 kg | 644.90 kg | 1.3 m x 2.1 m x 750 mm |
T1225E | 1.2 m x 2.5 m x 460 mm | 607.00 kg | 777.00 kg | 1.3 m x 1.6 m x 750 mm |
T1525E | 1.5 m x 2.5 m x 460 mm | 740.30 kg | 940.30 kg | 1.6 m x 2.6 m x 750 mm |
T1530E | 1.5 m x 3 m x 460 mm | 871.40 kg | 1077.99 kg | 1.6 m x 3.1 m x 750 mm |
T1540E | 1.5 m x 4 m x 460 mm | 1179.30 kg | 1470.00 kg | 1.6 m x 4.1 m x 750 mm |
Dynamic Deflection Coefficient
The dynamic deflection coefficient is a figure of merit for optical tables that is derived from the measurement of the optical table's compliance. Physically, the dynamic deflection coefficient can be interpreted as a measure of the table's motion when subjected to vibrations.
where Q is the amplification of the tables response to a vibrational source at a specific frequency (f) of the optic table. Q is calculated by dividing the compliance at the optical table resonance frequency by the theoretical compliance of an ideal rigid body. The maximum dynamic deflection coefficient is usually due to the response of the optical table at its first natural resonance frequency. Nexus® optical tables feature proprietary optimized damping mechanisms to limit the value of Q at the table's natural resonances.
Relative Tabletop Motion
The relative tabletop motion is the relative displacement of any two points on the optical table surface due to environmental vibrations transmitted through the optical table supports. The maximum relative tabletop motion is the worst case relative displacement; for a rectangular optical table, the two points that produce the worst case results are generally located at the corners of the optical table. The measurement reported in the specifications table was taken in a quiet laboratory environment (PSD <10-9 g2/Hz). The optical table supports used to support the optical table had a transmissibility less than 0.01 for frequencies greater than 10 Hz.
Deflection Under Load
The deflection under load is a measure of the stiffness of the optical table. The stiffness of an optical table can be quantified by placing a load at the center of the optical table and measuring the deflection of the optical table surface, which will have a parabolic shape. The specification reported in the table is the relative vertical displacement between the center and edge of the optical table.
Optimized Damping
Broadband Damping
The most important feature of an optical table or breadboard is its resonant frequency. Since resonant frequency and vibration amplitude are inversely related, the resonant frequency should be as high as possible to minimize vibration intensity. Nexus tables and breadboards are broadband damped over a specific range of frequencies. For improved performance, the damping is optimized for each size of table and breadboard offered.
We have performed extensive testing to optimize the thickness/size ratio of our tables. Larger sized tables (at least 10' or 3 m long) are offered with a standard 12.2" (310 mm) or 18.1" (460 mm) thickness for stability. Smaller sizes are available in both 8.3" (210 mm) and 12.2" (310 mm) thicknesses; they can be custom ordered in larger sizes.
Compliance
The most widely used transfer function for the vibrational response of an optical table is compliance. In the case of a constant (static) force, compliance is defined as the ratio of the linear or angular displacement to the magnitude of the applied force. In the case of a dynamically varying force (vibration), compliance is defined as the ratio of the excited vibrational amplitude (angular or linear displacement) to the amplitude of the force causing the vibration. Any deflection of the tabletop is evident by the change in relative position of the components mounted on the table surface. Therefore, by definition, the lower the compliance value is, the closer the optical table is to meeting the primary goal of optical table design: minimized deflection. Compliance is frequency dependent and is measured in units of displacement per unit force (meters per newton).

Click to Enlarge
Figure 118A Compliance Test Schematic
See the Vibration Isolation Tutorial for more information on compliance.
Compliance Measurement Procedure
An impulse hammer is used to apply a measured force to the top surface of the table or breadboard, and transducers attached to the surface detect the resultant vibrations (see Figure 118A). The signals from the transducers are interpreted by the analyzer and used to produce a frequency response spectrum (i.e., a compliance curve). During the development phase of an optical table, compliance curves are recorded at many points on the tabletop; however, the compliance is always greatest at the corners. The compliance curves and data published by Thorlabs are taken with the sensor located approximately 6" (150 mm) from the corner of the tabletop (closer to the edge for small breadboards), with the point of impact just inboard of the sensor. This test location represents the worst case data.
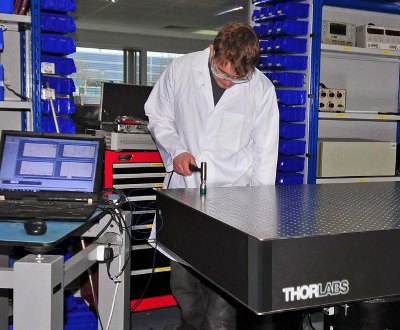
Click to Enlarge
Figure 118B Nexus Table Compliance Testing
Test Results
Video 27A Simplified Nexus Table Construction
Note: For Illustrative Purposes Only. Not a Representation of the Nexus Tables Construction Sequence
Nexus® Optical Tables and Breadboard Manufacturing
- Experienced In-House Design Engineers Create Models and Production Drawings
- Dedicated Tables Manufacturing Facilities for Repeatable and Consistent Production
- In-House Vibration Transmissibility and Compliance Testing
- In-House Welding and Fabrication
- Custom Design Capabilities for Unique Optical Table and Breadboard Solutions
- Lean Manufacturing:
- Cross-Training Allows Staff to Meet Production Demands
- Use of Current Technology Leads to Increased Quality
- Efficient Organization Leads to Time Savings for Customers
Our team has over 25 years of experience designing optical tables, breadboards, and related accessories. We leverage this experience to ensure that our Nexus® honeycomb optical tables and breadboards always meet two basic design goals: the natural resonances of the table should be as high as possible (well above the frequency of ambient environmental vibrations) and the table should be well damped (to quickly damp vibrations caused by equipment on the surface). To meet these goals, our engineers use a variety of tools to refine their designs, such as finite element analysis (FEA) and SolidWorks. FEA allows our engineers to evaluate various materials and to identify possible unwanted material stresses. SolidWorks is employed to build 3D models of every design.
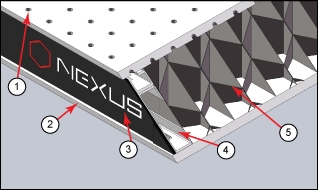
Click to Enlarge
Figure 27C Nexus Table / Breadboard Cross Section, showing the (1) Top Skin, (2) Bottom Skin, (3) Side Panels, (4) Side Rails, and (5) Honeycomb Core
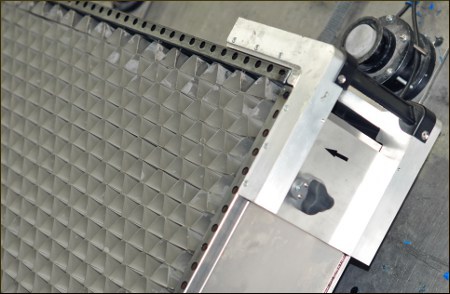
Click to Enlarge
Figure 27B Honeycomb Core of a Nexus Table During Manufacturing
Every Nexus optical table and breadboard is designed to be isotropic and symetrical in X, Y, and Z. For optimal thermal stability, only steel components are used in construction; no wood or plastic is used. Each table includes precision machined top and bottom mounting skins, an uninterrupted honeycomb core, and four side panels with finishing trim. See Video 27A for a simplified illustration of how our tables are assembled. For more details on each step in the process, read this tab.
Precision Steel Construction for Thermal Stability
Thorlabs' Nexus tables and breadboards feature all-steel construction, including 5 mm thick top and bottom skins and a 0.26 mm thick precision formed and welded steel honeycomb core. The core is geometrically formed using accurate pressing tools, and geometric pitch is retained by using welded flat shims. The honeycomb core in our Nexus tables and breadboards extends from the top skin to the bottom skin without intermediate layers, leading to a stiffer, more thermally stable product.
The key aspect of the thermally stable Nexus design is symmetrical isotropic steel construction in all axes. Steel components expand and contract similarly, maintaining flatness during changes in temperature. The steel core extends from top to bottom skin without intermediate plastic or aluminum spill management structures that reduce the overall stiffness of the product and introduce a higher coefficient of thermal expansion. Steel side panels are used rather than wood, which can introduce environmental instability due to susceptibility to moisture.
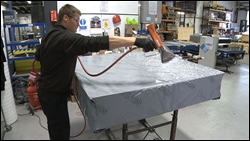
Click to Enlarge
Figure 27D Heat-Shrink Packaging Being Applied Over a Nexus Optical Table Prior to Shipment
Machined Finish with Minimized Contamination Packaging
Automated Finishing Process
Our Nexus tables and breadboards feature an automated orbital machined matte finish that is significantly smoother and flatter than our previous product line. The improved surface finish achieves ±0.1 mm (±0.004") flatness over any 600 mm x 600 mm area. Large radius corners are incorporated into the design, resulting in less pointed edges for lab safety.
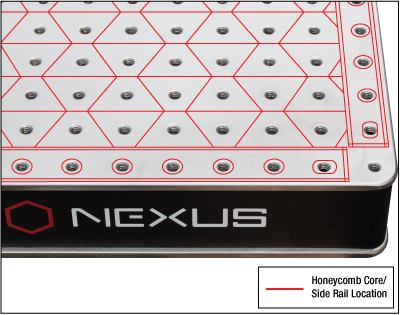
Click to Enlarge
Figure 27E Diagram showing the location of the honeycomb core and side panels, which do not intersect with any screw holes.
Sealed Edges with Anti-Static Packaging
All optical tables ship with a heat-shrink film that protects the table from most contaminants, such as dust, from entering the product during shipment. For additional protection, we offer an optional finishing and packaging service that is suitable for customers that want to minimize the presence of airborne contaminants on the interior and exterior surfaces of the table or breadboard. This includes anti-static packaging, which has a metallic foil inner layer protected by a heat shrink film outer cover, and gap-free edge panel construction to reduce static charge and prevent dust from entering the product.
Mounting Hole Options and Pattern
Individually Tapped, Countersunk Mounting Holes
Prior to bonding the components of the table, each mounting hole in the top surface is tapped and slightly countersunk to ensure that components mounted to the table sit flat. The mounting holes are then cleaned and sealed on the bottom with vinyl film discs (non-sealed models) or sealing cups (sealed hole models, see the Sealed Mounting Holes section). The vinyl film is easily punctured when using a hole for the first time. Cap screws can be finger tightened into the mounting holes of all Nexus tables and breadboards.
Reduced Hole Pattern Border
Our top surface hole patterns extend to the edge of the table or breadboard with only a 12.5 mm (0.5”) border, equal to half of a hole-to-hole spacing. This increases the usable area of the table and improves mounting option flexibility.
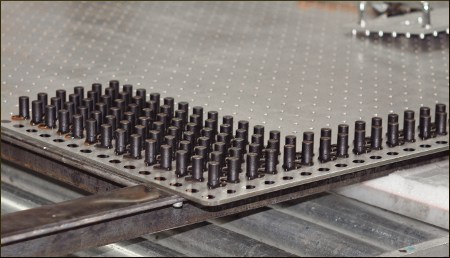
Click to Enlarge
Figure 27F Nylon Sealing Cups Installation During Manufacturing
Increased Screw Depth and Optional Sealed Holes
Our custom-designed core maker produces precision formed and welded honeycomb core strips. The core is shaped and installed so that it does not intersect with any screw holes (see Figure 27E), allowing screws to be inserted far into the table, all the way to the bottom skin (for non-sealed-hole models). See the Specs tab for specific screw depth specifications, including outer border holes.
Sealed Mounting Holes
Tables and breadboards can be manufactured with nylon sealing cups glued to the underside of the top skin (see Figure 27F) for liquid spill management. Sealed hole tables are available in all sizes and thicknesses, and the maximum screw depth is 1" (25.4 mm).
Mounting Holes on the Bottom Skin
Our breadboards feature at least four mounting holes in the base skin, permitting the secure attachment of standard or vibration isolating feet and allowing more flexibility for integrating breadboards onto tables or into setups in addition to using breadboard stands.
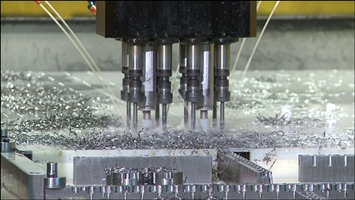
Click to Enlarge
Figure 27G Optical tables and breadboards are tapped using a high-speed drilling machine.
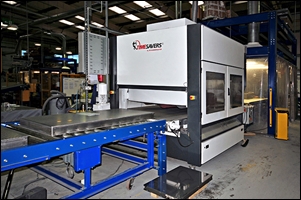
Click to Enlarge
Figure 27H The surfaces of our tables and breadboards are sanded in our finishing machine.
Posted Comments: | |
Travis Briles
 (posted 2024-09-04 15:39:05.45) Hi-
The compliance plots for the 460 mm thick tables appear to have an error. The left and right axes have the same numerical value for plots mm/N (left) and in/lb (right). This doesn't make sense. Could you send the compliance curve for T48K that has correct units? user
 (posted 2023-07-17 15:51:11.12) If we compare the compliance curves between 1.5mx2.5m, 460 nm Thick and 1.5mx2.5m, 310 nm Thick, I expect the 460nm thick will have a lower compliance, but the curves show opposite. I assume that for the same size (width and length) table, a thicker one will have a lower compliance, is that right? Lukas Bruder
 (posted 2023-01-30 12:01:22.903) In the complience measurement for the 460mm-thick table there is a problem with the axis units. Left-hand axis is given in in/lbf, right hand axis in mm/N. Yet. both axis are identical. There must be something wrong. I believe the left axis in units in/lbf is the correct one. Please confirm.
Thanks,
Lukas fguzman
 (posted 2023-01-31 06:46:34.0) Thanks for contacting Thorlabs. Thank you for pointing this out, the T510K/T510X and T1530E/T1530R plots have the correct axes and units. We will work in correcting the others. Thank you for your feedback. user
 (posted 2020-06-07 23:24:30.71) If we compare the Compliance Curves in this page between 460 mm thick tables and 310 mm thick tables for the ideal rigid bodies, it seems that the 310 mm tables are better than the 460 mm tables. Why? The 460 mm tables are heavier than the 310 mm tables. So, I expected that the ideal rigid body compliance curves for the 460 mm thick tables should be lower than the 310 mm tables. But the data shown in this page indicates that the opposite is the case. Am I missing something? cwright
 (posted 2020-06-09 08:54:38.0) Response from Charles at Thorlabs: Thank you for your query and for bringing this to our attention. It appears that the uploaded graphs may be incorrect. Certainly I can see that many of the graphs for the 460 mm tables have equivalent metric and imperial scales which is not correct. The 460 mm thick tables should indeed have a lower compliance curve and we will upload graphs with the correct information as soon as possible.
We do measure a compliance curve for every Nexus table we make so if you need a couple for comparison then we may be able to provide these in the mean time. I will ask a colleague at your local office to reach out to you about this. Sambit Mitra
 (posted 2019-11-18 12:26:43.057) Hello,
I would like to know if you also have a way or sell some parts to connect two optical tables?
Best Regards,
Sambit cwright
 (posted 2019-11-21 07:36:54.0) Response from Charles at Thorlabs: Hello Sambit, thank you for your query. We can join tables together but the method of doing so requires we build custom tables and fit the requisite hardware during their production. Technical support will reach out to you directly to discuss your needs. |