PRO8 Laser Diode Temperature Controller Modules
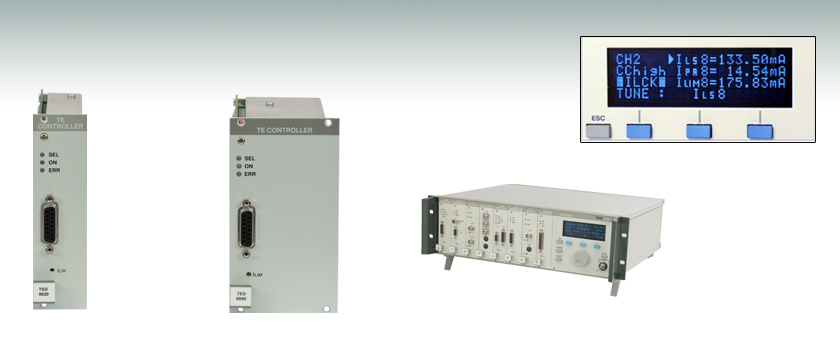
- 3 Current / Power Ranges
- Excellent Temperature Stabilization
- Easy-to-Access PID Adjustments
TED8020 Module
TED8080 Module
PRO8000 8 Slot Chassis with LDC8000,
TED8000, ITC8000, & PDA8000 Modules
Easy to Read Display
No PC Required for Operation

Please Wait
Key Specificationsa | |||
---|---|---|---|
Item # | TEC Current | Max Output Power | Module Width |
TED8020 | ±2 A | 16 W | 1 Slot |
TED8040 | ±4 A | 32 W | |
TED8080 | ±8 A | 64 W | 2 Slots |
PRO8 Series Modulesa | |
---|---|
Laser Diode Current Controllers (Up to 8 A) | ![]() |
TEC Temperature Controllers (Up to 64 W) | |
Combination Laser Diode Current (Up to 1 A) & TEC Temperature Controllers (Up to 16 W) |
|
DWDM DFB Laser Modulesb | |
Optical Switches | |
Photocurrent Measurement Modules |
Features
- Temperature Control Range: -12.375 to 90.000 °C (Semiconductor Sensor)
- Temperature Control Range: 5 Ω to 20 kΩ and 50 Ω to 200 kΩ (Thermistor in 2 Ranges)
- Temperature Stability: <0.002 °C
- TEC Current Ranges: ±2 A and 16 W, ±4 A and 32 W, ±8 A and 64 W
- Supports Thermistors: AD590, AD592, and LM335
- Optional Sensors (Pt 100, Pt 1000 - Replaces AD590/AD592/LM335 Sensors) Upon Request
- Adjustable P, I and D Settings
Introduction
The TED8000 Series Modules are plug-in temperature controllers for our PRO8 Series Chassis. They provide excellent temperature stabilization, typically ±0.001 °C (AD590 sensor), for optimal laser operation and other applications requiring precise thermal control. This facilitates highly stable operation of temperature sensitive components, such as optical nonlinear birefringent crystal, where phase matching requires sensitive control of the crystal’s temperature. Separate adjustment of the P, I and D settings of the temperature control loop enables optimal settling times for different thermal loads. The TED8000 Series of temperature controllers are ideal companions to our LDC8000 Laser Diode Current Controller Modules. When the TED8000 module is used with a laser diode control module in the same PRO8 chassis, the temperature window protection feature switches off the laser diode current if the temperature of the laser exceeds a used-defined temperature window (high and low threshold). The PRO8 Chassis can be ordered with these modules preinstalled; contact Tech Support prior to placing your order.
Thorlabs recommends recalibrating these modules every 24 months and offers a factory recalibration service. To order this service, scroll to the bottom of the page and select Item # CAL-TED8.
High Power Laser Systems
With up to 64 W of cooling power, the TED8080 is well matched to our LDC8080 Laser Diode Control Module that provides 8 A laser drive current.
TEC Safeguards
Damage to the TEC cooler is prevented by setting an adjustable TEC current limit. This can either be set via a recessed potentiometer on the module front panel (hardware limit), via the front panel softkeys or by one of the standard interfaces (software limit).
The TED8000 Series modules meet extremely high standards regarding precision and drift performance and provide a low noise, bipolar output. This enables extremely stable wavelength control and safe thermal load management.
Choice of Temperature Sensors
The TED8000 Series modules can be operated with thermistors, AD590/AD592 IC sensors and LM335 transducers. When operated with a thermistor the thermistor calibration constant can be set so that all applicable settings and displays can be done directly in °C, rather than Ω (ohms). Optionally, the TED8000 Series Controllers can be fitted to ultra-low temperature applications (lead-salt lasers), where heating only is required (KRYO option).
Adjustable PID Control Loop
For optimization of laser temperature settling time the P-, I- and D- settings of the temperature control loop can be set via menu-driven softkeys or via one of the remote interfaces.
User-Friendly Controls
The PRO8 display menu allows configuration of any module in the chassis. The operational parameters are easily accessed using mnemonic symbols and simple prompts for user-friendly operations. All settings are retained in memory and automatically recalled upon powering on the mainframe, as long as modules are not being moved to a different slot.
Connection Cables
A CAB420-15 cable is required to connect the TED8000 Series Modules to a Thorlabs' Laser Diode Mount. This cable can be ordered separately. It has a length of 1.5 m, PIN Diagrams are shown below.
For further information, please contact Tech Support.
Item # | TED8020 | TED8040 | TED8080 |
---|---|---|---|
TEC Current Control Range | -2 to +2 A | -4 to +4 A | -8 to +8 A |
Compliance Voltage | >8 V | ||
Maximum Output Power | 16 W | 32 W | 64 W |
Measurement Resolution TEC Current | 0.07 mA | 0.15 mA | 0.3 mA |
Measurement Accuracy TEC Current | ±10 mA | ±20 mA | ± 50 mA |
Measurement Resolution TEC Voltage | 0.3 mV | ||
Measurement Accuracy TEC Voltage | ±20 mV | ||
Noise & Ripple (Typical) | <1 mA | <2 mA | <4 mA |
TEC Current Limit | |||
Setting Range (20-Turn Pot) | 0 to ≥2 A | 0 to ≥4 A | 0 to ≥8 A |
Resolution D/A Converter | 0.5 mA | 1 mA | 2 mA |
Accuracy | ±20 mA | ±40 mA | ±80 mA |
Temperature Sensors: Thermistor (TED80X0 & TED80X0PT) | |||
Control Range | 5 Ω to 20 kΩ and 50 Ω to 200 kΩ (Switchable) | ||
Calibration | Exponential Form, Steinhart-Hart | ||
Resolution | 0.3 Ω/3 Ω | ||
Accuracy | ±2.5 Ω/±25 Ω | ||
Stability (24h), Typical | <0.5 Ω/<5 Ω | ||
Temperature Sensor: IC-Sensors (AD590 / AD592 / LM335) (TED80X0) | |||
Control Range | -12.375 to +90 °C | ||
Calibration | 2-Point Linearization | ||
Resolution | 0.0015 °C | ||
Accuracy | ±0.1 °C | ||
Setting Resolution | 0.025 °C | ||
Stability (24 hr), Typical | < 0.001 °C | ||
Temperature Sensor Pt100 Platinum: Optional Feature (PT) for TED80X0a | |||
Control Range | -12.375 to +90°C | ||
Resolution | 0.0015 °C | ||
Accuracy | ±0.3 °C | ||
Stability (24 hr), Typical | <0.005 °C | ||
Temperature Sensor Pt1000 KRYO: Optional Feature (KRYO) for TED80x0; Heating Onlya | |||
Measurement Current | 1 mA / 400 μA | ||
Control Range | 20 to 310 K | ||
Resolution | 2 mK (Within Temp Range of 20 to 155 K) | ||
Accuracy | ±2 K (Within Temp Range of 20 to 155 K) | ||
Stability (24 hr), Typical | 0.005 K (Within Temp Range of 20 to 155 K) |
TEC and Temperature Sensor Connector
TED8xxx Series
Pin | Connection |
---|---|
1 | Status-LED Anode |
2 | Voltage Detector TEC Element + |
3 | Thermistor (-), Ground |
4 | Thermistor (+) |
5 | TEC Element (+) |
6 | TEC Element (+) |
7 | TEC Element (+) |
8 | Status -LED Cathode (Ground) |
9 | Voltage Detector TEC Element (-) |
10 | AD590 - |
11 | AD590 + |
12 | Leave Open |
13 | TEC Element (-), Ground |
14 | TEC Element (-), Ground |
15 | TEC Element (-), Ground |
TED8xxx-PT Series
Pin | Connection |
---|---|
1 | Status-LED Anode |
2 | Voltage Detector TEC Element + |
3 | PT-100 Current Source (-), Ground |
4 | PT-100 Current Source (+) |
5 | TEC Element (+) |
6 | TEC Element (+) |
7 | TEC Element (+) |
8 | Status -LED Cathode (Ground) |
9 | Voltage Detector TEC Element (-) |
10 | Voltage Measurement Input (-) |
11 | Voltage Measurement Input (+) |
12 | Leave Open |
13 | TEC Element (-), Ground |
14 | TEC Element (-), Ground |
15 | TEC Element (-), Ground |
PID Basics
The PID circuit is often utilized as a control loop feedback controller and is commonly used for many forms of servo circuits. The letters making up the acronym PID correspond to Proportional (P), Integral (I), and Derivative (D), which represents the three control settings of a PID circuit. The purpose of any servo circuit is to hold the system at a predetermined value (set point) for long periods of time. The PID circuit actively controls the system so as to hold it at the set point by generating an error signal that is essentially the difference between the set point and the current value. The three controls relate to the time-dependent error signal. At its simplest, this can be thought of as follows: Proportional is dependent upon the present error, Integral is dependent upon the accumulation of past error, and Derivative is the prediction of future error. The results of each of the controls are then fed into a weighted sum, which then adjusts the output of the circuit, u(t). This output is fed into a control device, its value is fed back into the circuit, and the process is allowed to actively stabilize the circuit’s output to reach and hold at the set point value. The block diagram below illustrates the action of a PID circuit. One or more of the controls can be utilized in any servo circuit depending on system demand and requirement (i.e., P, I, PI, PD, or PID).
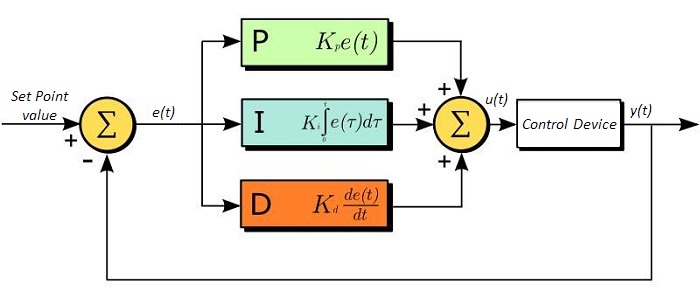
Through proper setting of the controls in a PID circuit, relatively quick response with minimal overshoot (passing the set point value) and ringing (oscillation about the set point value) can be achieved. Let’s take as an example a temperature servo, such as that for temperature stabilization of a laser diode. The PID circuit will ultimately servo the current to a Thermoelectric Cooler (TEC) (often times through control of the gate voltage on an FET). Under this example, the current is referred to as the Manipulated Variable (MV). A thermistor is used to monitor the temperature of the laser diode, and the voltage over the thermistor is used as the Process Variable (PV). The Set Point (SP) voltage is set to correspond to the desired temperature. The error signal, e(t), is then the difference between the SP and PV. A PID controller will generate the error signal and then change the MV to reach the desired result. For example, if e(t) states that the laser diode is too hot, the circuit will allow more current to flow through the TEC (proportional control). Since proportional control is proportional to e(t), it may not cool the laser diode quickly enough. In that event, the circuit will further increase the amount of current through the TEC (integral control) by looking at the previous errors and adjusting the output to reach the desired value. As the SP is reached (e(t) approaches zero), the circuit will decrease the current through the TEC in anticipation of reaching the SP (derivative control).
Please note that a PID circuit will not guarantee optimal control. Improper setting of the PID controls can cause the circuit to oscillate significantly and lead to instability in control. It is up to the user to properly adjust the PID gains to ensure proper performance.
PID Theory
The output of the PID control circuit, u(t), is given as

where
Kp= Proportional Gain
Ki = Integral Gain
Kd = Derivative Gain
e(t) = SP - PV(t)
From here we can define the control units through their mathematical definition and discuss each in a little more detail. Proportional control is proportional to the error signal; as such, it is a direct response to the error signal generated by the circuit:
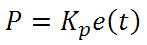
Larger proportional gain results in larger changes in response to the error, and thus affects the speed at which the controller can respond to changes in the system. While a high proportional gain can cause a circuit to respond swiftly, too high a value can cause oscillations about the SP value. Too low a value and the circuit cannot efficiently respond to changes in the system.
Integral control goes a step further than proportional gain, as it is proportional to not just the magnitude of the error signal but also the duration of the error.
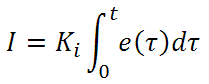
Integral control is highly effective at increasing the response time of a circuit along with eliminating the steady-state error associated with purely proportional control. In essence integral control sums over the previous error, which was not corrected, and then multiplies that error by Ki to produce the integral response. Thus, for even small sustained error, a large aggregated integral response can be realized. However, due to the fast response of integral control, high gain values can cause significant overshoot of the SP value and lead to oscillation and instability. Too low, and the circuit will be significantly slower in responding to changes in the system.
Derivative control attempts to reduce the overshoot and ringing potential from proportional and integral control. It determines how quickly the circuit is changing over time (by looking at the derivative of the error signal) and multiplies it by Kd to produce the derivative response.
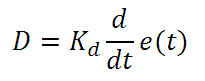
Unlike proportional and integral control, derivative control will slow the response of the circuit. In doing so, it is able to partially compensate for the overshoot as well as damp out any oscillations caused by integral and proportional control. High gain values cause the circuit to respond very slowly and can leave one susceptible to noise and high frequency oscillation (as the circuit becomes too slow to respond quickly). Too low and the circuit is prone to overshooting the SP value. However, in some cases overshooting the SP value by any significant amount must be avoided and thus a higher derivative gain (along with lower proportional gain) can be used. The chart below explains the effects of increasing the gain of any one of the parameters independently.
Parameter Increased | Rise Time | Overshoot | Settling Time | Steady-State Error | Stability |
---|---|---|---|---|---|
Kp | Decrease | Increase | Small Change | Decrease | Degrade |
Ki | Decrease | Increase | Increase | Decrease Significantly | Degrade |
Kd | Minor Decrease | Minor Decrease | Minor Decrease | No Effect | Improve (for small Kd) |
Tuning
In general the gains of P, I, and D will need to be adjusted by the user in order to best servo the system. While there is not a static set of rules for what the values should be for any specific system, following the general procedures should help in tuning a circuit to match one’s system and environment. A PID circuit will typically overshoot the SP value slightly and then quickly damp out to reach the SP value.
Manual tuning of the gain settings is the simplest method for setting the PID controls. However, this procedure is done actively (the PID controller turned on and properly attached to the system) and requires some amount of experience to fully integrate. To tune your PID controller manually, first the integral and derivative gains are set to zero. Increase the proportional gain until you observe oscillation in the output. Your proportional gain should then be set to roughly half this value. After the proportional gain is set, increase the integral gain until any offset is corrected for on a time scale appropriate for your system. If you increase this gain too much, you will observe significant overshoot of the SP value and instability in the circuit. Once the integral gain is set, the derivative gain can then be increased. Derivative gain will reduce overshoot and damp the system quickly to the SP value. If you increase the derivative gain too much, you will see large overshoot (due to the circuit being too slow to respond). By playing with the gain settings, you can maximize the performance of your PID circuit, resulting in a circuit that quickly responds to changes in the system and effectively damps out oscillation about the SP value.
Control Type | Kp | Ki | Kd |
---|---|---|---|
P | 0.50 Ku | - | - |
PI | 0.45 Ku | 1.2 Kp/Pu | - |
PID | 0.60 Ku | 2 Kp/Pu | KpPu/8 |
While manual tuning can be very effective at setting a PID circuit for your specific system, it does require some amount of experience and understanding of PID circuits and response. The Ziegler-Nichols method for PID tuning offers a bit more structured guide to setting PID values. Again, you’ll want to set the integral and derivative gain to zero. Increase the proportional gain until the circuit starts to oscillate. We will call this gain level Ku. The oscillation will have a period of Pu. Gains for various control circuits are then given to the right in the chart.
Note that when using the Ziegler-Nichols tuning method with some devices like the DSC1 digital servo controller, the integral and derivative terms must be normalized by the sample rate. To do this, the integral term determined from the table should be divided by the sample rate in Hertz and the derivative term should be multiplied by the sample rate in Hertz.
Posted Comments: | |
Jasper F.
 (posted 2023-11-29 09:54:28.89) Dear Thorlabs-Team, our institute uses multiple PRO8 TEC Controller Cards TED8040. They work great but do not support PT100 sensors. Is there a possibility to upgrade this functionality? Thanks for your feedback. hkarpenko
 (posted 2023-12-01 05:32:21.0) Dear Jasper,
thank you for your feedback.
Indeed, the standard TED8040 controller does only support thermistors AD590, AD592, and LM335. An upgrade for compatibility with PT100 and PT1000 is possible on request. I will contact you directly to discuss this further with you. Alastair Curnock
 (posted 2023-04-12 15:09:43.273) Hi
What is the maximum voltage that the TED 8080 can supply? Does it depend on what current limit is used? eg 8V@8A (64W), but 16V@4A (64W)
Thanks hkarpenko
 (posted 2023-04-14 08:30:09.0) Dear Customer,
thank you for your feedback. The compliance voltage for each of these three devices is ~8V. The provided current for the devices differs, thus the maximum output power is different. I contact you directly to discuss this issue further with you. cblakesa47
 (posted 2015-02-23 13:01:55.347) Hello - I am wondering if it is possible to use the TED8020 with the PRO8000 chassis to control temperature in a heating-only configuration (using a resistive heater such as HT10K, for example, with an AD590 temperature Transducer). Thanks for your help. tschalk
 (posted 2015-02-26 11:52:14.0) This is a response from Thomas at Thorlabs. Thank you very much for your inquiry. It is possible to use the TED in a heating-only configuration. Normally the device is used with a Peltier (TEC) element where current in one direction cools while current in the other direction heats the device. You have to make sure that current can only flow in one direction through the resistive heater. Therefore you can use two diodes to prevent the device from continuously heating up by just changing the current flow direction. I will contact you directly with detailed information. sharrell
 (posted 2012-05-21 12:05:00.0) Response from Sean at Thorlabs: I am sorry that you had difficulty finding the CAB420-15 on our website. We have updated the link, but unfortunately this change will happen this evening when our website runs automatic updates. In the meantime, the cable may be found using this link: http://www.thorlabs.com/NewGroupPage9.cfm?ObjectGroup_ID=307.
Thank you for your patience as we fix this link. busko
 (posted 2012-05-21 11:13:01.0) I can't find CAB420-15 cable for temperature control unit. The link in description on this page just reload the current page.. Only TED modules are visible. |

The pin descriptions shown in Tables 381A and 381B denote the typical pin assignments used by Thorlabs' family of laser diode temperature controllers and laser diode mounts. Table 381C gives the physical pin connections between the 15-pin and 9-pin sides of the CAB420-15 cable.
Table 381A Male 15-Pin Connector | |
---|---|
![]() |
|
1 | Status LED (+) (for TEC On/Off Indication)a |
2 | TEC Voltage Measurementb |
3 | Thermistor (-), Ground |
4 | Thermistor (+) |
5 | TEC (+) |
6 | TEC (+) |
7 | TEC (+) |
8 | LM 135/335 (-), Grounda |
9 | TEC Voltage Measurementb |
10 | Transducer AD 590/592 (-), LM 135/335 (+) |
11 | Transducer AD 590/592 (+), LM 135/335 (+) |
12 | No Connection |
13 | TEC (-), Status LED (-) |
14 | TEC (-), Status LED (-) |
15 | TEC (-), Status LED (-) |
Table 381B Female 9-Pin Connector | |
---|---|
![]() |
|
1 | Status LED (+) (for TEC On/Off Indication)a |
2 | Thermistor (+) |
3 | Thermistor (-), Ground |
4 | TEC (+) |
5 | TEC (-), Status LED (-) |
6 | No Connection |
7 | Transducer AD 590/592 (-), LM 135/335 (+) |
8 | LM 135/335 (-), Grounda |
9 | Transducer AD 590/592 (+), LM 135/335 (+) |
Table 381C Pin Connections | |
---|---|
15-Pin Side | 9-Pin Side |
1 | 1 |
2 | 4 |
3 | 3 |
4 | 2 |
5 | 4 |
6 | 4 |
7 | No Connection |
8 | 8 |
9 | 5 |
10 | 7 |
11 | 9 |
12 | No Connection |
13 | 5 |
14 | 5 |
15 | No Connection |

Table G3.1 CAL-TED8 Recalibration Service | |
---|---|
Calibration Service Item # | Compatible Modules |
CAL-TED8 | TED8020, TED8040, TED8080 |
Thorlabs offers a recalibration service for the TED8000 Series Laser Diode Temperature Controller Modules. To ensure accurate measurements, we recommend recalibrating the devices every 24 months. Table G3.1 lists the modules for which the CAL-TED8 recalibration service is available.
Requesting a Calibration
Thorlabs provides two options for requesting a calibration:
- Complete the Returns Material Authorization (RMA) form. When completing the RMA form, please enter your name, contact information, the Part #, and the Serial # of the item being returned for calibration; in the Reason for Return field, select "I would like an item to be calibrated." All other fields are optional. Once the form has been submitted, a member of our RMA team will reach out to provide an RMA Number, return instructions, and to verify billing and payment information.
- Enter the Part # and Serial # of the item that requires recalibration below and then Add to Cart. A member of our RMA team will reach out to coordinate return of the item for calibration. Should you have other items in your cart, note that the calibration request will be split off from your order for RMA processing.
Please Note: To ensure your item being returned for calibration is routed appropriately once it arrives at our facility, please do not ship it prior to being provided an RMA Number and return instructions by a member of our team.