In-House Anodization
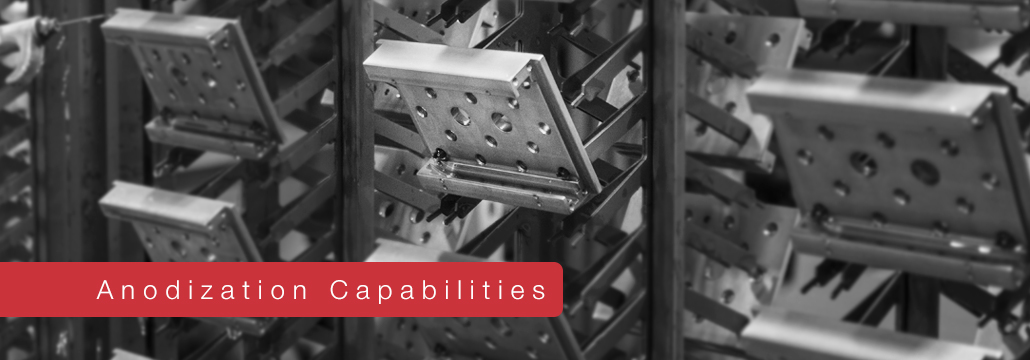

Please Wait
Completed in 2020, Thorlabs' modular, in-house metal finishing line was purpose-built to ensure quality, consistency, and speed in producing portfolio parts and OEM orders.
In-House Anodization Features
- Aluminum – The anodization line is capable of anodizing aluminum including 2000, 6000, and 7000 series alloys.
- Total Line Automation - The entire metal finishing process is automated, which produces consistent coat quality, thickness, and color.
- Chemical Consistency - The same chemicals are always stored in the same tanks. We only run our own parts to avoid contamination and reduce variables that could introduce errors.
- Type II and III Anodization - The line is outfitted to run both types of anodization, depending on the coating required.
- Custom Titanium Racking - This minimizes racking marks on parts and saves production time since we don't need to strip racks between anodizing runs.
- Volume Orders – The automated line is designed to optimize throughput and includes inline storage capacity for flight bars so that it can be run lights out on high volume jobs.
Anodization is an electrochemical process that converts a metal surface into a hard, corrosion-resistant finish. In Aluminum the anodized surface can be dyed and then sealed to have a color. The anodized surface doesn’t chip or flake, allows for the part to retain the tight dimensional tolerances need in the photonics industry, and is easily engraved.
Environmental and Safety Considerations
Our water filtration system recycles the rinse water used during the process, halving the water waste compared to other metal finishing systems. Several features were also added to the anodization line to considerably reduce the fumes released by the chemical tanks. Covers on each tank drastically cut the amount of vapor that escapes into the room and make it easier to maintain the tank’s temperature, lowering power consumption. A fume-scrubbing exhaust system pulls any additional vapor that may have leaked and pushes it through a water curtain, removing the particulates in the air. This air purification creates a safer work environment for our employees.
The Anodization Process

Before the anodization process can begin, our machined parts are placed on electrically conducting racks. The electricity that then flows through the aluminum parts chemically prepares them for anodization. These racks also double as a storage queue, allowing multiple batches of parts to be
processed by our automated facility overnight. Our operators choose which baths to apply, set soak time, and set current and voltage.

Moving from the storage rack, the parts enter an alkaline cleaner bath to remove any unwanted particles from the surface. An acid etching dissolves a thin layer on the surface of the aluminum to create a uniform finish. The parts are rinsed twice before moving to an anodization tank.

In the anodization tank, a current creates the anodic oxide that makes the aluminum surface hard and corrosion resistant. Thorlabs’ anodization facility has three anodization tanks, including tanks for Type II and Type III anodization. Type II anodization is the type of coating on most of Thorlabs’ current anodized product lines. It creates a thinner coat on the aluminum and does not need to be chilled during production. Type III anodization creates a thicker, harder anodization coat but requires a specialized tank capable of maintaining low temperatures. We can precisely control the coating thickness to achieve the high dimensional tolerances needed for high performance optomechanics.

The anodization process leaves the surface of the product porous, allowing us to dye the parts. After a rinse, the anodized parts are moved to one of three dye tanks: clear (no dye), black, or red. Black dye in the anodized surface reduces scattered light, ideal for lab components. Finally, a seal coat keeps the dye from bleeding, and the parts move to a rack for drying.
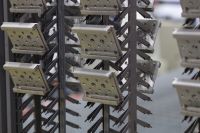

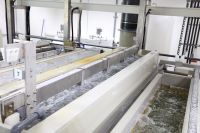

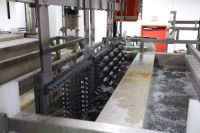

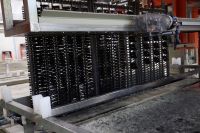

Contact Us for Your OEM Anodization Project
Every custom order, even single components, is treated as high priority at our anodization facility. We offer Type II and Type III anodization as well as red, black, and clear coating colors. Our team provides fast, high-quality service to get your application up and running quickly. Let us anodize your OEM components that will be used in finished goods, manufacturing tools, or pieces of testing equipment. Contact techsales@thorlabs.com or click the "Contact an OEM Specialist" button to start the process!
Posted Comments: | |
Samuel Lin
 (posted 2024-08-22 11:31:42.033) Hello
I have observed that Thorlabs' different anodized aluminums have different damage thresholds.
Can you tell me why there is such a difference?
For example:
Magnetic Laser Safety Screens TPSM1 and Beam Traps (BT600/M)
Why is the Max Energy Density of the two so different? jdelia
 (posted 2024-08-30 08:35:06.0) Thank you for contacting Thorlabs. Since the BT600(/M) is prone to backscattering, the max energy density is more so referring to the point at which the level of backscattered light becomes higher than we recommend. On the other hand, the max energy density for something like a laser safety screen will be the point at which the anodization layer becomes physically damaged. Vyshaali Jagadeesan
 (posted 2024-01-05 12:35:40.757) Hi,
Im interested in your anodization capabilities for custom parts. What black dye options do you offer? What are the different sealing options?
Thank you,
Vyshaali jpolaris
 (posted 2024-01-09 05:48:47.0) Thank you for contacting Thorlabs. I have reached out to you directly with some technical data on the black dye and sealant that we use. |