Motorized Precision Rotation Mount
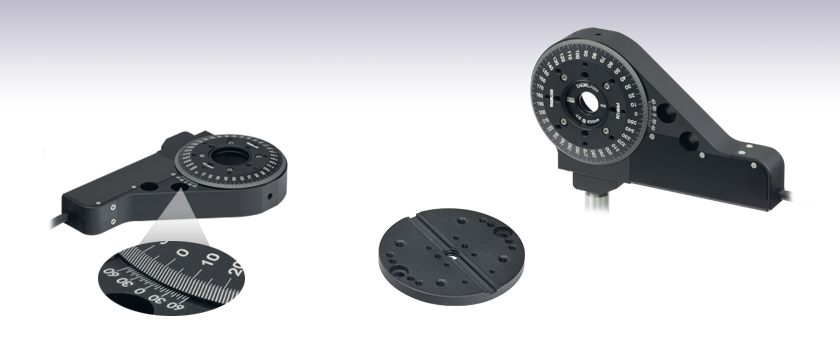
- Continous 360° Motorized Rotation
- 25 arcsec Minimum Incremental Motion
- Rotational Velocity: 25 Degree/Second
- Compatible with Our SM1 Lens Tubes and 30 mm Cage Systems
PRM1Z8
PRM1SP1
PRM1Z8
with a WPMH05M-633 Wave Plate

Please Wait
Key Specificationsa | Value |
---|---|
Bidirectional Repeatability | ±0.1° |
Backlash | ±0.3° |
Max Rotation Velocity | 25 deg/s |
Horizontal On-Axis Load Capacity | 1.5 kg (3.31 lbs) |
Vertical On-Axis Load Capacity | 0.5 kg (1.10 lbs) |
Achievable Incremental Motion (Min) | 25 arcsec |
Repeatable Incremental Motion (Min) | 0.03° |
Percentage Accuracy | 0.1% |
Home Location Accuracy | ±0.2° |
Range | 360° Continuous |
Features
- 1° Graduations on Main Dial
- 25 deg/s Rotation Velocity
- Compact Design is Only 23 mm Thick
- Home Limit Switch
- Post Mountable (See Mounting Tab)
- Compatible with SM1 (1.035"-40) Accessories
- Accepts Ø1" Optics up to 0.50" (12.5 mm) Thick
- Recommended Driver: KDC101 DC Servo Controller
The PRM1Z8 is a small, compact, DC servo motorized 360° rotation mount and stage that accepts Ø1" optics and SM1-threaded components. The user can measure the angular displacement by using the Vernier dial in conjunction with the graduation marks that are marked on the rotating plate in 1° increments. This rotation stage/mount is also equipped with a home limit switch to facilitate automated rotation to the precise 0° position, allowing absolute angular positioning thereafter. The limit switch is designed to allow continuous rotation of the stage over multiple 360° cycles.
The KDC101 DC Servo Controller, sold separately below, is the ideal companion for achieving smooth, continuous motion that can be automated via the software interface. We also offer the KPRM1E(/M) bundle which includes the PRM1(/M)Z8 stage/mount, the KDC101 controller, and KPS101* power supply at a significant savings over ordering these items separately.
The PRM1Z8 is supplied with 19.6" (0.5 m) of cable. An 8 ft (2.5 m) extension cable (PAA632) is available separately.
*This previous-generation item is not available for individual purchase. If a replacement is needed, the KPS201 Power Supply can be used.
Motor Specifications | |
---|---|
Motor Type | DC Servo |
Nominal Voltage | 6 V |
No Load Speed | 6560 rpm |
No Load Current | 7.43 mA |
Nominal Speed | 1050 rpm |
Nominal Torque (Maximum Continuous Torque) | 1.26 mN•m |
Nominal Current (Maximum Continuous Current) | 0.156 A |
Stall Torque | 1.54 mN•m |
Starting Current | 0.184 A |
Maximum Efficiency | 65% |
Terminal Resistance | 32.7 Ω |
Terminal Inductance | 0.607 mH |
Torque Constant | 8.38 mN•m/A |
Speed Constant | 1140 rpm/V |
Speed / Torque Gradient | 4450 rpm/mN•m |
Mechanical Time Constant | 13.9 ms |
Rotor Inertia | 0.298 g•cm2 |
Stage Specifications | |
---|---|
Translation and Motion Parameters | |
Travel Range | 360° Continuous |
Bidirectional Repeatabilitya | ±0.1° |
Backlashb | ±0.3° |
Max Rotation Velocity | 25 deg/s |
Min Achievable Incremental Motionc | 25 arcsecond |
Min Repeatable Incremental Motiond | 0.03° |
Percentage Accuracy | 0.1% |
Home Location Accuracy | ±0.2° |
Load Capacity | |
Horizontal On-Axis Load Capacity | 1.5 kg (3.3 lbs) |
Vertical On-Axis Load Capacity | 0.5 kg (1.1 lbs) |
Physical | |
Dimensions | 131 mm x 23 mm x 83 mm (5.18" x 0.91" x 3.26") |
Weight | 0.21 kg (0.46 lb) |
Cable Length | 0.5 m (1.6 ft) |
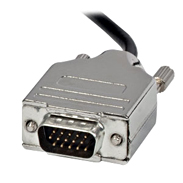
Motor Connector Pin Out
Pin | Description | Pin | Description |
---|---|---|---|
1 | Ground (Limit and Vcc) | 8 | Reserved For Future Use |
2 | Reserved For Future Use | 9 | Ident Resistora |
3 | Limit Switch | 10 | Vcc/Ident Resistor |
4 | Reserved For Future Use | 11 | Encoder Channel B |
5 | Motor (+) | 12 | Reserved For Future Use |
6 | Reserved For Future Use | 13 | Encoder Channel A |
7 | Motor (-) | 14, 15 | Reserved For Future Use |
D-type Male
Post Mounting Options
Normally the PRM1Z8 is mounted horizontally. The stage can be fixed directly to the work surface using the counter-bored 1/4"-20 (M6) holes in the main body. For complete flexibility, the stage/mount can be mounted vertically using the 8-32 (M4) threaded holes in various locations (as shown below), including the option to mount in a vertical inclined orientation. When in the vertical orientation, the reduced thickness of the stage is extremely beneficial for optical path applications where space is limited.
![]() |
![]() |
![]() |
![]() |
Cage System Mounting
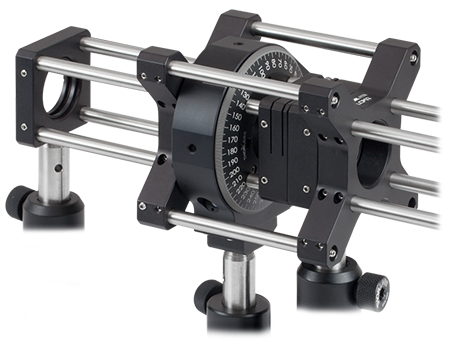
The PRM1Z8 can be aligned within a 30 mm cage system by using two LCP02 30 mm to 60 mm cage plate adapters, a CPU1 rotating cage segment plate, and three ER3 Cage Rods. This creates a motorized rotation mount within a rigid optical assembly. For more details on how these items work together, please see the animation to the right.
Rotation of the cage assembly using the PRM1Z8 can be restricted to a specific segment of the system by using the rotating cage segment plate. For details on how to incorperate the PRM1Z8 within a 30 mm cage system, please see the image to the left.
- KPRM1E: 143768
- KPRM1E/M: 143906
- PRM1Z8: 143086
- PRM1Z8/M: 143681
Software
Kinesis Version 1.14.50
The Kinesis Software Package, which includes a GUI for control of Thorlabs' Kinesis system controllers.
Also Available:
- Communications Protocol
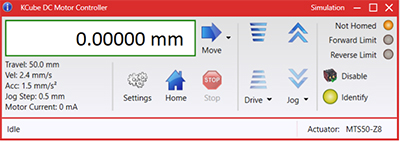
Kinesis GUI Screen
Thorlabs offers the Kinesis® software package to drive our wide range of motion controllers. The software can be used to control devices in the Kinesis family, which covers a wide variety of motion controllers ranging from small, low-powered, single-channel drivers (such as the K-Cubes™) to high-power, multi-channel benchtop units and modular 19" rack nanopositioning systems (the MMR60x Rack System).
The Kinesis Software features .NET controls which can be used by 3rd party developers working in the latest C#, Visual Basic, LabVIEW™, or any .NET compatible languages to create custom applications. Low-level DLL libraries are included for applications not expected to use the .NET framework and APIs are included with each install. A Central Sequence Manager supports integration and synchronization of all Thorlabs motion control hardware.
By providing this common software platform, Thorlabs has ensured that users can mix and match any of our motion control devices in a single application, while only having to learn a single set of software tools. In this way, it is perfectly feasible to combine any of the controllers from single-axis to multi-axis systems and control all from a single, PC-based unified software interface.
The software package allows two methods of usage: graphical user interface (GUI) utilities for direct interaction with and control of the controllers 'out of the box', and a set of programming interfaces that allow custom-integrated positioning and alignment solutions to be easily programmed in the development language of choice.
Legacy Software
Select products are still capable of running the legacy APT™ software package. Information on software compatibility can be found in the product documentation (), and additional details about the APT software can be found here.
Thorlabs' Kinesis® software features new .NET controls which can be used by third-party developers working in the latest C#, Visual Basic, LabVIEW™, or any .NET compatible languages to create custom applications.
C#
This programming language is designed to allow multiple programming paradigms, or languages, to be used, thus allowing for complex problems to be solved in an easy or efficient manner. It encompasses typing, imperative, declarative, functional, generic, object-oriented, and component-oriented programming. By providing functionality with this common software platform, Thorlabs has ensured that users can easily mix and match any of the Kinesis controllers in a single application, while only having to learn a single set of software tools. In this way, it is perfectly feasible to combine any of the controllers from the low-powered, single-axis to the high-powered, multi-axis systems and control all from a single, PC-based unified software interface.
The Kinesis System Software allows two methods of usage: graphical user interface (GUI) utilities for direct interaction and control of the controllers 'out of the box', and a set of programming interfaces that allow custom-integrated positioning and alignment solutions to be easily programmed in the development language of choice.
For a collection of example projects that can be compiled and run to demonstrate the different ways in which developers can build on the Kinesis motion control libraries, click on the links below. Please note that a separate integrated development environment (IDE) (e.g., Microsoft Visual Studio) will be required to execute the Quick Start examples. The C# example projects can be executed using the included .NET controls in the Kinesis software package (see the Kinesis Software tab for details).
![]() |
Click Here for the Kinesis with C# Quick Start Guide Click Here for C# Example Projects Click Here for Quick Start Device Control Examples |
![]() |
LabVIEW
LabVIEW can be used to communicate with any Kinesis- or APT-based controller via .NET controls. In LabVIEW, you build a user interface, known as a front panel, with a set of tools and objects and then add code using graphical representations of functions to control the front panel objects. The LabVIEW tutorial, provided below, provides some information on using the .NET controls to create control GUIs for Kinesis- and APT-driven devices within LabVIEW. It includes an overview with basic information about using controllers in LabVIEW and explains the setup procedure that needs to be completed before using a LabVIEW GUI to operate a device.
![]() |
Click Here to View the LabVIEW Guide Click Here to View the Kinesis with LabVIEW Overview Page |
![]() |
Reading a Vernier Scale on a Linear Main Scale
Vernier scales are typically used to add precision to standard, evenly divided scales (such as the scales on Thorlabs' rotation, goniometric, or translation mounts). A vernier scale has found common use in many precision measurement instruments, the most common being calipers and micrometers. The vernier scale uses two scales side-by-side: the main scale and the vernier scale. The direct vernier scale has a slightly smaller spacing between its tick marks owing to the vernier scale having N ticks for every N - 1 ticks on the main scale. Hence, the lines on the main scale will not line up with all the lines on the vernier scale. Only one line from the vernier scale will match well with one line of the main scale, and that is the trick to reading a vernier scale.
Figures 1 through 3 show a linear vernier scale system for three different situations. In each case, the scale on the left is the main scale, while the small scale on the right is the vernier scale. When reading a vernier scale, the main scale is used for the gross number, and the vernier scale gives the precision value. In this manner, a standard ruler or micrometer can become a precision instrument.
The 0 on the vernier scale is the "pointer" (marked by a red arrow in Figures 1 - 5) and will indicate the main scale reading. In Figure 1 we see the pointer is lined up directly with the 75.6 line. Notice that the only other vernier scale tick mark that lines up well with the main scale is 10. Since the pointer lines up with the main scale’s 75.6, the reading from Figure 1 is 75.60 (in whatever units the instrument measures).
That is essentially all there is to reading a vernier scale. It's a very straightforward way of increasing the precision of a measurement instrument. To expound, let’s look at Figure 2. Here we see that the pointer is no longer aligned with a line on the main scale, but instead it is slightly above 75.6 and below 75.7; thus, the gross measurement is 75.6. The first vernier line that coincides with a main scale line is the 5, shown with a blue arrow. The vernier scale gives the final digit of precision; since the 5 is aligned to the main scale, the precision measurement for Figure 2 is 75.65.
Since this vernier scale is 10% smaller than the main scale, moving the vernier scale by 1/10 of the main scale will align the next vernier marking. This asks the obvious question: what if the measurement is within the 1/10 precision of the vernier scale? Figure 3 shows just this. Again, the pointer line is in between 75.6 and 75.7, yielding the gross measurement of 75.6. If we look closely, we see that the vernier scale 7 (marked with a blue arrow) is very closely aligned to the main scale, giving a precision measurement of 75.67. However, the vernier scale 7 is very slightly above the main scale mark, and we can see that the vernier scale 8 (directly above 7) is slightly below its corresponding main scale mark. Hence, the scale on Figure 3 could be read as 75.673 ± 0.002. A reading error of about 0.002 would be appropriate for
this instrument.

Click to Enlarge
Figure 1: An example of how to read a vernier scale. The red arrow indicates what is known as the pointer. Since the tick mark labeled 10 on the vernier scale aligns with one of the tick marks on the main scale, this vernier scale is reading 75.60 (in whatever units the instrument measures).
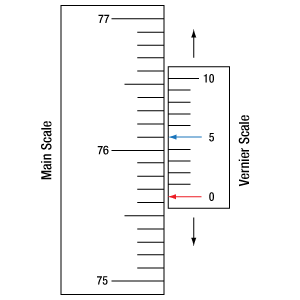
Click to Enlarge
Figure 2: The red arrow indicates the pointer and the blue arrow indicates the vernier line that matches the main scale. This scale reads 75.65.
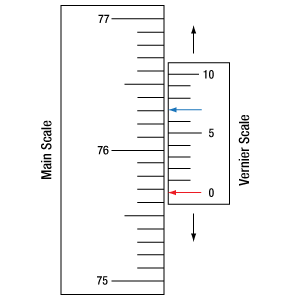
Click to Enlarge
Figure 3: The red arrow indicates the pointer, and the blue arrow indicates the vernier line that matches the main scale. This scale reads 75.67 but can be accurately read as
75.673 ± 0.002.
Reading a Vernier Scale on a Rotating Main Scale
The vernier scale may also be used on rotating scales where the main scale and vernier scale do not share units. Figures 4 and 5 show a vernier scale system for two different situations where the main scale is given in degrees and the vernier scale has ticks every 5 arcmin (60 arcmin = 1°). In each case, the scale on the top is the main scale, while the small scale on the bottom is the vernier scale.
In Figure 4 we see the pointer is lined up directly with the 341° line. Notice that the only other vernier scale tick marks that line up well with the main scale are ±60 arcmin. Since the pointer lines up with the main scale at 341°, the reading from Figure 4 is 341.00°.
There are two ways to determine the reading if the zero on the vernier scale line is between two lines of the main scale. For the first method, take the line on the left side of the pointer on the vernier scale and subtract that value (in arcmin) from the value on the main scale that is to the right on the main scale. As an example, in Figure 5 the vernier pointer is between 342° and 343°; using the left blue arrow of the vernier scale results in
As we've seen here, vernier scales add precision to a standard scale measurement. While it takes a bit of getting used to, with a little practice, reading these scales is fairly straightforward. Vernier scales, whether they are direct or retrograde*, are read in the same fashion.
*A retrograde vernier scale has a larger spacing between its tick marks with N ticks for every N + 1 ticks on the main scale.
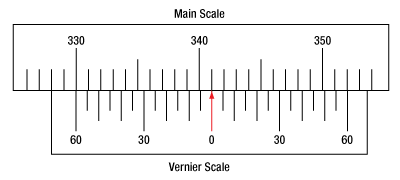
Click to Enlarge
Figure 4: An example of a vernier scale where the main scale and the vernier scale are in different units (degrees and arcmins, respectively). The red arrow indicates the pointer. This scale reads 341.00°.
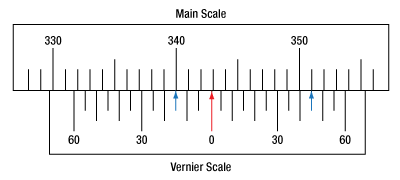
Click to Enlarge
Figure 5: The red arrow indicates the pointer and the blue arrows give the precision value from the vernier scale.
This scale reads 342.75°.
Posted Comments: | |
user
 (posted 2024-08-07 01:38:54.947) Hello,
I would like to know if it is possible to use the PRM1Z8 without the KDC101 controller. I need the PRM1Z8 to rotate uniformly and continuously through 360 degrees. Can this be achieved using only the PRM1Z8?
Thank you. do'neill
 (posted 2024-08-09 04:32:13.0) Thank you for reaching out. The motor will need a controller of some kind to control it. In addition, as the PRM1Z8 was designed with the KDC101 and other controllers are outside our control, we can not off much direct support when using 3rd party controllers so we would recommend using the KDC101 to control this stage. I will reach out to you directly to discuss your application with you. user
 (posted 2024-05-13 14:20:17.347) Hello, I am a user using a PRM1Z8. It shows continuously "Error Code - 35002" and "Error Message - Motor Overcurrent". Please let me know how can I solve this errror. spolineni
 (posted 2024-05-17 09:10:06.0) Thank you for your enquiry. Few factors can cause an overcurrent error due to the motor drawing high current. I will reach out to you personally to provide further assistance in troubleshooting. Benjamin Zhang
 (posted 2024-05-10 04:20:41.657) 你好,请问想要执行这个棱镜的定时旋转或者持续旋转是选哪几个参数来执行呢,我有找到一个叫CC_StartPolling的参数,但是好像实现不了,在python里面执行哈,谢谢 do'neill
 (posted 2024-05-22 08:07:14.0) Thank you for your feedback. An example for running the KDC101 in Python can be found here - https://github.com/Thorlabs/Motion_Control_Examples/blob/main/Python/KCube/KDC101/kdc101_pythonnet.py
I will reach out to you directly to discuss you application. Gülçin Ş. Aşkın
 (posted 2024-01-29 21:20:53.767) Hello. I have two MTS25/M-Z8. One of them shows "Motor overcurrent" error in Home command. (Error code: 35002). Please let me know what can I check to resolve this issue. lijiong shen
 (posted 2023-06-22 21:03:44.16) can I use python serial commands in Linux system to control this device? do'neill
 (posted 2023-06-29 10:37:05.0) Response from Daniel at Thorlabs. Our software is not designed to be used with Linux. I will reach out to you directly to discuss your application. Andrew C
 (posted 2023-06-07 14:43:54.427) Hi, I keep getting overload errors when I am using the PRM1Z8 rotation stage. These errors occur whether I am using the Kinesis or APT software. Is there a remedy for this? Thanks. Guseon Kang
 (posted 2023-05-07 19:33:02.647) Hello. I am a user using two PRM1/M-Z8.
Either one shows "Motor overcurrent" error in Home command. (Error code: 35002).
Please let me know what can I check to resolve this issue. do'neill
 (posted 2023-05-09 07:42:41.0) Response from Daniel at Thorlabs. I will reach out to you directly to discuss this with you. Lionel Windels
 (posted 2023-03-22 13:46:03.607) I'm getting really upset with this PRM1Z8 device. Always getting soon or later the overload message. With no load, with load, with labview program, with Kinesis program... what is going wrong. For such an expensive device, it is seriously problematic such a sensitive situation. It also can't handle precise steps, after 60°jog at 5° angle it moved down to 59.8, then overload. JReeder
 (posted 2023-03-24 11:47:03.0) Thanks for your enquiry. I am sorry to hear that you are experiencing some issues with your PRM1Z8. I am reaching out to you to assist you with this and to help with troubleshooting Dima Cheskis
 (posted 2023-01-18 00:41:21.293) Dear Sir/Madam,
I'm writing a PRM1/MZ8 rotation mount software tool using the KDC101 brushed motor controller. I succeeded in rotating the mount, but I didn't find a command to change the direction of movement. I'm using APT software.
Could you help me with this problem?
Best, Dima Cheskis.
Dr. Dima Cheskis
Physics Department
Ariel University DJayasuriya
 (posted 2023-01-18 06:50:50.0) Thank you for your enquiry. With APT you are able to change the 'wheel settings' that would change the directional sense. We have go in touch with you directly to troubleshoot your issue. Jong-ryul Choi
 (posted 2022-07-12 19:14:13.67) Dear engineer in Thorlabs,
Hello!
Actually, I need to connect two rotation stages (PRM1/MZ8E) orthogonally (90 degrees). Using this, I want to create a sample stage that moves in two dimensions by driving two rotation stages simultaneously through a computer. For this, please tell me the parts that can connect the two rotation stages (PRM1/MZ8E) at 90 degrees. cwright
 (posted 2022-07-15 06:58:37.0) Response from Charles at Thorlabs: Thank you for your query. The easiest way to do this would be to us an M6 to M4 adapter such as AP6M4M and the PRM1SP1 mounting plate adapter. Jaume Meseguer Sánchez
 (posted 2022-06-29 15:37:49.45) Good afternoon,
I wanted to get the position of the rotator using labview by dividing the encoder count by 34,555, which is the value you specify for linear motors in the labview Kinesis guide. However, it seems that it does not work for rotators. Which is the number which I have to divide the encoder counter?
Thank you very much in advance!
Best,
Jaume DJayasuriya
 (posted 2022-06-30 10:50:17.0) Thank you for your inquiry. For the PRM1-Z8 encoder count per deg. is 1919.6418578623391. You would be able to find this in our com. protocol : https://www.thorlabs.com/Software/Motion%20Control/APT_Communications_Protocol.pdf Sylvain M
 (posted 2021-11-23 11:25:47.637) Hello,
I am experiencing trouble with the motorized precision rotation mount PRM1/MZ8 connected with the controller KDC101.
Yesterday I tried to connect it with the software Kinesis, downloaded from your website. No matter if I asked for a given position or a pitch, the rotation mount would turn indefinitely until I disconnect the device with the function
"Disable' on Kinesis.
I tried to use it again today, but since then, the device is not responding, neither with Kenesis nor manually. It looks stuck and cannot be moved. I also tried to connect it with another power supply (TDC001) but it didn't move either.
What could be the origin of this problem and how could I fix it?
Thanks in advance YLohia
 (posted 2021-12-23 11:56:08.0) Thank you for your feedback. To clarify, are you unable to get the PRM working using Kinesis or the KDC controller? Could you please email us a photo/video of the PRM and how it behaves when connecting to the cube using Kinesis and manually using the controller KDC? It may be that the lead screw of the PRM might need some grease if its stuck. We have reached out to you directly to troubleshoot further. George Brown
 (posted 2021-09-11 18:31:20.787) In an earlier feedback, you state that the encoder calibration for the PRM1Z8 is 1919.64 steps per degree. Can you explain how this strange number is derived from the mechanical parameters of the stage and encoder? cwright
 (posted 2021-09-14 03:45:47.0) Response from Charles at Thorlabs: Thank you for your query. The encoder for the Z8 motor counts the rotation of the motor itself. There are 512 counts to this encoder. There follows a gearbox after. This then connects to a worm drive and a wormwheel which rotates the moving world. The relationship is then: EncCounts/degree = (EncCounts * Gearbox_ratio) / (360°/wheel_teeth/worm_threads)). I will email you to discuss this further. ilya r
 (posted 2021-03-25 11:24:46.1) Hello, Could you, please, explain your definition of Minimum vs Repeatable Incremental Motion? Let's say, I am measuring an angular dependence of something by doing unidirectional rotation with minimum steps. On the plot that I obtain, will the angular positions have error of 0.03 degree or 25 arcsec? Or should I rather look at bidirectional repeatability?
Also, when the step is completed, is the stage completely motionless, or it could experience rotational vibrations due to, for example, electrical noise in the servo motor? In the latter case, what it the range of those oscillations? cwright
 (posted 2021-03-26 11:50:40.0) Response from Charles at Thorlabs: Hello and thank you for your query. The minimum incremental motion is the measured minimum incremental motion that the stage can achieve. It does not mean it is repeatable. This may be more useful when aligning a component as the smallest move that can be made is desirable regardless of repeatability. The repeatable incremental motion is the minimum incremental motion repeatedly achieved within the standard error and is more useful for applications such as such as scanning where you would need a uniform step size. I will reach out to you to discuss your application and determine which specifications are most relevant. Huang LongCheng
 (posted 2020-12-25 02:56:59.427) Hello there,
Here is an issue about trouble shooting of PRM1Z8 rotation motor.
I found that when set the position by APT or Kinesis software, the real position is incorrect. For example, if i set
the position to 25 degrees, the panel on software does show 25 degrees, but in fact the scale on the motor shows its position is at 20 degrees.
Here are two points I'm looking for some helps:
1. How do I fix these problem in software or hardware?
2. Why is the motor behave like these, is there any comment? DJayasuriya
 (posted 2021-01-07 05:37:07.0) Thank you for your inquiry. I have contacted you directly to get this issue resolved. Xiaoguang Sun
 (posted 2020-08-24 11:04:38.397) I have PRM1/M-Z8 with KDC001, do you have Labview VIs and examples? cwright
 (posted 2020-08-27 05:37:30.0) Response from Charles at Thorlabs: Hello Xiaoguang, we do have examples available which can be downloaded from the website at the following link: https://www.thorlabs.com/newgrouppage9.cfm?objectgroup_id=12675&tabname=Example%20VIs.
You may be particularly interested in Kinesis - KDC101 - Move Absolute and Kinesis - KDC101 - No Front Panel. You just have to enter the details of your controller, such as the serial number. If you have any issues with these your local technical support team will be happy to help. user
 (posted 2020-03-25 12:18:07.457) Hello,
i have few PRM1/M-Z8 and MTS50/M-Z8, controlled by TDC001 and KDC001.
until now, we used them with Labview, but we would like to use Python 3.x.
Do you have basic examples or procedure on how to do it, or how to start ?
Regards, DJayasuriya
 (posted 2020-03-26 08:17:31.0) Response from Dinuka at Thorlabs: Thank you for your query. We will get in touch directly to get more information about your issue. user
 (posted 2020-03-03 03:21:44.85) Hello, we have three PRM1/MZ8 that we are having problem with. One of them is mechanically not functioning and two of them has encoder issues. Could you reach us through my e-mail, thank you. DJayasuriya
 (posted 2020-03-03 05:44:47.0) Response from Dinuka at Thorlabs: Thanks for your query. We will get in touch directly to get more information about your issue. Diane R
 (posted 2020-01-28 05:53:53.57) Hi, I am looking to control the PRM1/MZ8 with a TDC001 using Python. Would you have any short example to provide? Thanks a lot. AManickavasagam
 (posted 2020-01-28 07:54:10.0) Response from Arunthathi at Thorlabs: Unfortunately, we do not offer a documentation for the use of the TDC with Python. However, we have some examples for its superseded version that are based on the C API and .NET API that are included in the Kinesis software package. I have contacted you directly with the available examples. user
 (posted 2019-11-14 06:05:47.017) Hi,
Is it possible to control the PRM1/MZ8 with the controllor KDC101 using Linux (Ubuntu/Debian) through Matlab? ActiveX is just for Windows and it should in principle work through serial. Do you have a wrapper for that?
Thanks! cwright
 (posted 2019-11-21 08:53:25.0) Response from Charles at Thorlabs: Hello and thank you for contacting us. We do have a short example for using serial commands with Matlab and I will reach out to you directly about this. abhishek akn
 (posted 2019-11-06 02:49:16.683) What is the 'minimum speed (in deg/sec)' for PRM1/MZ8? Unlike the stepper motor rotation stage, we don't see this parameter in the specs tab... cwright
 (posted 2019-11-07 10:17:34.0) Response from Charles at Thorlabs: Hello Abhishek, unfortunately we do not have a minimum velocity specification for this stage. Such a specification is typically hard to pin down as the minimum achievable velocity for a stage can be significantly affected by the velocity fluctuations resulting from the PID loop and at very low speeds any imperfection in the lead screw or even build up of grease can affect the reliability of this velocity. For the stepper motor this is easier to specify given the capability of the controller. Typically however, at very low speeds, the slower you go the more unstable your movement. norihiro matsusaka
 (posted 2019-10-19 13:41:08.143) Hi
”OVER LOAD” appears on the digital display. What does it mean? AManickavasagam
 (posted 2019-10-22 06:43:33.0) Response from Arunthathi at Thorlabs: Thanks for your query. This would be associated with the input drive current. I have contacted you directly to troubleshoot and resolve this issue you have. AManickavasagam
 (posted 2019-10-22 06:43:33.0) Response from Arunthathi at Thorlabs: Thanks for your query. This would be associated with the input drive current. I have contacted you directly to troubleshoot and resolve this issue you have. andrey
 (posted 2018-07-18 12:30:20.847) What is this device accuracy? Specs says that bidirectional repeatability, backlash, home location accuracy are 0.1, 0.3 and 0.2 degrees? Is this true? How do you achieve 25 arcsecond (=0.007 deg) incremental motion precision with that repeatability? Did you mean 0.1, 0.3, 0.2 mdeg? What is the encoder accuracy? bhallewell
 (posted 2018-07-19 07:05:11.0) Response from Ben at Thorlabs: Thank you for your question. The Minimum Achievable Motion is not a repeatable value - this spec would instead be the Minimum Repeatable Incremental Motion which is specced as 0.03°. The Minimum Achievable Incremental Motion will be the smallest possible jog that could be achieved being the a description of the possible lower limit of incremental motion. The calculated resolution based on the encoder resolution is 2 arcsec based on the encoder resolution which will output 1919.64 EncCounts/degree. f..e.jones-16
 (posted 2017-08-22 14:02:35.067) Dear Thorlabs
I am having difficulty with selecting the motor in the activeX control icon, when i select it and get the list of options, the selection for the motor is not there. I've attempted all varieties of the software and none of them allow me to select the motor controller option. I'm running the 32-bit LabVIEW on a 64-bit computer. bhallewell
 (posted 2017-08-23 09:21:22.0) Response from Ben at Thorlabs: This will likely be due to an incompatibility between the version of APT you've downloaded & the version of your OS or LabVIEW. I would recommend an uninstall of your current software & instead installing the 'APT 32-bit Software for 64-bit Windows' option from the 'APT Software' tab in the link below.
https://www.thorlabs.com/software_pages/ViewSoftwarePage.cfm?Code=Motion_Control
Please contact techsupport.uk@thorlabs.com if the problem persists. dolerite
 (posted 2017-05-25 17:33:27.63) Dear Manager, After Installed APT Software. I tried to Active X of APT to make a program with Visual C++ to control KDC101. But It is impossible to insert "Active X" in the dialogue box because "MGMotor Control" is not listed in the list of Active X. Please let me know how to insert "Active X" supplied by APT software in the Visual C++ program. tcampbell
 (posted 2017-06-05 10:35:54.0) You can find our video tutorials in the following link to clarify the steps for inserting the ActiveX control in your Visual C++ project.
https://www.thorlabs.com/tutorials/APTProgramming.cfm
If the Active X control doesn't exist in this, this may be due to installing a version of APT which isn't compatible with platform type of Visual Studio e.g. running 64-bit APT ActiveX controls within a 32-bit platform. A Tech Support representative has contacted you to assist you further. samini
 (posted 2016-12-05 17:49:03.893) I have PRM1/MZ7 (& TDC001) devices. OS of my computer is windows 7 (64-bit). I try to recognized those devices in "APT config", but it didn't. I check that my computer recognized the devices.
In the interface of APT config (stage tap), it did not show the S/Ns of those devices.
Without recognizing in APT config, I tried to execute vi (labview) program. In that case, it is worked but inproperly. Namely, it is recognized as other device such as linear stage. So I can't control the devices as I want.
How can I fixed this problem ?
And I also use Kinesis program. In this case, Kinesis program works properly. But, in this case, adding DLL process in vi program has problem. When I insert "Thorlabs.MotionControl.Controls.dll" in step of "Select .NET Control", some pop-up message is arised such as - version is not matched. Because version of my labview is 2011.
How can I properly control those devices in labview 2011 ? bhallewell
 (posted 2016-12-15 11:58:14.0) Response from Ben at Thorlabs: It may be worth checking the USB connection with the device in your OS device manager first to ensure the devices are connected successfully. I would advise ensuring that in APTConfig, simulator mode is un-checked & the dwell time is increased. It is good practise to check in APTUser if your devices are connected & working properly before running your LabVIEW program.
The error message that you are seeing maybe a result of the version of software you have downloaded. Please ensure this matches the type of LabVIEW you are running & that this is for a 64-bit OS.
I will contact you directly to make sure you're up & running. alexander.hupfer
 (posted 2016-11-11 06:56:07.95) Can this products be used in soft vacuum? bhallewell
 (posted 2016-11-11 04:36:46.0) Response from Ben at Thorlabs: This stage is not designed for use in a vacuum environment. zachary.wach
 (posted 2016-09-26 12:29:04.777) Can this product be utilized by LabVIEW? bhallewell
 (posted 2016-09-27 05:06:53.0) Response from Ben at Thorlabs: Hi Zachary - yes it can! Our free motion control software package called Kinesis can be found in the following link, along with a guide to making use of .NET framework controls within LabVIEW.
https://www.thorlabs.de/software_pages/ViewSoftwarePage.cfm?Code=Motion_Control joos
 (posted 2016-08-22 09:23:00.17) My PRM1Z8 turns forever when homing so I can't "home" my device. The homing parameters are correct and it used to work before. The hardware limit switch looks fine (the half-ball of the moving piece touchs the small needle of the fixed piece). Can the contact between ball and needle be rusted for not using the device in a long time ? Help would be appreciated. Thanks. Maxime Joos bhallewell
 (posted 2016-08-23 03:11:06.0) Response from Ben at Thorlabs: Thank you for your feedback. This is most likely a fault with the limit switch assembly within the stage. I will contact you directly regarding repair of the device. smee
 (posted 2015-10-09 12:24:41.037) Hi, I'm not sure which software I should install: the APT Software or the Kinesis? Which one is "better" considering the system load i.e. less CPU/RAM-usage; needs to install less drivers; runs faster? My system is Win7-32bit. Thanks bhallewell
 (posted 2015-10-09 09:58:07.0) Response from Ben at Thorlabs: Thank you for your email. The answer here is Kinesis. This is our recently released software package which in facts utilises the same drivers & FTDI communication protocol as our APT software. Kinesis however does hold improved functionality such as an advanced move sequencer & being able to stop & re-establish communications with motion control devices during runtime. cjacobs
 (posted 2015-03-06 11:10:59.677) Referring my previous post regarding the stage identification working in APT but not in labview with our own cable. I have some new info.
We must have used an old pin diagram which does not have pin 9 (ident). Our cable has lines 1,2,3,5,7,10,11,13,15). It will be difficult to redo the cables.
Would it be possible to
a) force the labview driver to the PRM1Z8 bypassing the ident feature?
b) use the ident method used in APT
c) put a ident resistor inside the dsub connector between pin 9 and 1 on the driver side. What value to use? I measure ~3875 Ohm. How accurate must this resistor value be?
Please assist! rcapehorn
 (posted 2015-03-10 01:04:57.0) Response from Rob at Thorlabs: Thank you for your feedback. I am sorry you are having issues using our product with your extension lead. As you have said, the issue is related to the ident resistor and the fact that you have not extended the pin 9 connection. I will email you directly with a solution. cjacobs
 (posted 2015-03-06 08:24:25.623) Hi, we developed our own little labview VI with the labview drivers provided. All worked fine with the PRM1Z8 connected directly to the cube driver.
Recently, we built our own extension cable with the DSUB pin-outs as provided in the manuals.
Using the thorlabs APT software, everything detects 100% and works as expected. However, if we use our labview program, the PRM1Z8 is detected as a linear stage Z606(B).
Any suggestion how to fix the problem? user
 (posted 2014-05-26 14:42:47.89) Hi!
Where can I download the software of the stage? Is there anything new? I am using aptuser 1.0.22 and for the config version 1.1.0
Is in a newer version the "bwait" function working? Many thanks for your help.
Best regards,
Cornelia msoulby
 (posted 2014-05-27 09:46:58.0) Response by Mike at Thorlabs: The software can be downloaded from the following location http://www.thorlabs.de/software_pages/ViewSoftwarePage.cfm?Code=APT this should install the latest software version. You should then run the APT firmware utility to update the firmware to the latest version. The bWait function does work correctly, if the bWait parameter is set to 'False', the method returns as soon as the moving sequence has been initiated. If bWait is set to 'True', then any move command returns only after the motors have finished homing. When a client application needs to perform a move sequence, it is more efficient programming practice to set bWait to 'False' and respond to the Move Complete event. This event driven approach allows a client application to service other tasks while the motors are moving. If you need any further help please provide us with an email address or contact us at techsupport.uk@thorlabs.com cjacobs
 (posted 2014-04-16 19:19:55.35) Please update the product overview to clearly state that this rotates the whole cage and not the optic inside the cage system. The current sentence "Four #4-40 holes are provided so that the PRM1Z8 can be incorporated into a cage system" is misleading. The true operation is only clear once you look at the detailed photos in the mounting tab or in the documents.
We bought this assuming it would rotate the optic inside the cage. Rotating the whole cage seem rather pointless. We probably would have bought it regardless as their is no alternative to automate rotation of an optic inside the cage - BUT it would have been nice to know this upfront! msoulby
 (posted 2014-04-17 04:14:24.0) Response from Mike at Thorlabs: Thank you for your feedback, you are correct the PRM1MZ8 is not cage compatible and we will update the website to reflect this. Please accept our apologies for any confusion caused. We are currently developing a fully 30mm cage compatible motorised rotation stage to fill this gap in our product range and we expect this to be released towards the end of the year. myanakas
 (posted 2014-04-17 10:03:43.0) Response from Mike at Thorlabs: Thank you for pointing out this problem with our presentation. I will work to make it more clear as to how this product works. Though it is true that this product will rotate the entire cage system and not just the optic, we do offer the CPR1 Rotating Cage Plate Segment (http://www.thorlabs.com/newgrouppage9.cfm?objectgroup_id=7075) which might help solve the problem you are having. This will allow the cage segment between the CPR1 and the PRM1Z8 to have full 360 degree rotation while keeping the rest of the cage system fixed. However, it should be noted that there are only 4-40 tapped holes on the front of the rotation mount, so the PRM1Z8 cannot be placed in the center of a cage system. h.aguiar
 (posted 2014-04-16 11:12:59.943) Is it possible to control this device through Matlab? Thanks in advance. Hilton msoulby
 (posted 2014-04-17 04:07:55.0) Response from Mike at Thorlabs: Yes it is possible to control this device through Matlab, I have contacted you directly with a short user guide on how to incorporate our motors into Matlab. Arthur.Varkentin
 (posted 2014-02-13 09:54:16.463) Is it possible to combine this mount (PRM1/MZ8) with the angle plate MSAP90/M?
My goal is to get a well defined arbitrary tilt angle for a sample which is located on the angle plate. The light goes from top to bottom. msoulby
 (posted 2014-02-17 06:29:53.0) Response from Mike at Thorlabs: The PRM1/MZ8 was primarily designed to hold 1” optics and SM1 threaded components. I have contacted you directly with a possible solution. jason.hoelscher
 (posted 2014-01-21 16:25:58.573) Do you have motorized rotation mounts which afford higher rotation speeds (say at least 360°/s)? msoulby
 (posted 2014-01-21 10:32:41.0) Response from Mike at Thorlabs: At this time we do not currently have a rotation stage that can operate at these speeds. However we are currently developing a new rotation stage that will use brushless DC motors. We are aiming to have a maximum rotation speed of 1080deg/s. We recently demonstrated a prototype of this stage at a tradeshow and expect the final release to happen within the next few months. user
 (posted 2013-12-16 16:53:55.177) Please can you tell me what temperature range the motor will work over? msoulby
 (posted 2013-12-18 04:09:16.0) Response from Mike at Thorlabs: We only recommend using the stage at ambient room temperatures. As it currently stands we do not test them nor have the ability to test them at temperatures outside this range. As a result we are unable to verify any operation at lower temperatures. However cooling down a stage to below the dew point will cause condensation to build up both on and inside the stage. This excessive moisture could potentially cause problems, and as outlined in the manual this should be avoided.
From manual:
“If this equipment is used in a manner not specified by the manufacturer, the protection provided by the equipment may be impaired. In particular, excessive moisture may impair operation. Spillage of fluid, such as sample solutions, should be avoided. If spillage does occur, clean up immediately using absorbent tissue. Do not allow spilled fluid to enter the internal mechanism.” user
 (posted 2013-08-14 14:32:03.443) I am currently trying to use the PRM1Z8 as a rotatable sample holder. Is it possible to constrict the rotation angle between two fixed values (i.e. 0° and 30°) or at least rule out full rotations when homing? I've tried to change the maximum and minimum position in the instrument settings but that doesn't seem to do anything. pbui
 (posted 2013-08-20 18:11:00.0) Response from Phong at Thorlabs: Thank you for your post. Unfortunately, APT does not feature the ability to limit the rotation angle between a specified range. However, you may be able to accomplish this in a third party programming environment such as LabVIEW. To avoid full rotations when homing, you can edit the Motor Drive settings that would determine which direction the stage would spin. You can also change the "Panel Display Rotation Move Mode" under the "Rotation Stages" tab to the Rotate Quickest setting. If you have any further questions, please contact techsupport@thorlabs.com claudia.ruizdegalarretafanjul
 (posted 2013-08-01 11:42:55.853) I am trying to work with PRM1Z8 and I am completely UNABLE to run the installation software from the DVD under Windows 8 (I can do it with other IOS): the DVD is not recognized at all by my PC. Please help?
Regards
Claudia jlow
 (posted 2013-08-01 11:17:00.0) Response from Jeremy at Thorlabs: We currently do not support Windows 8 yet. I apologize for this inconvenience. kam233
 (posted 2013-05-16 16:44:57.6) I'm working with PRM1Z8 and TDC001, trying to interface with Matlab. Is it necessary to have the Gauges Blockset in Simulink to control it? If not, do you have any examples of Activex control in Matlab? Should I be using Simulink at all? There aren't many examples or helpful tutorials online that I can find. Thank you. jlow
 (posted 2013-05-21 15:22:00.0) Response from Jeremy at Thorlabs: You don't need Simulink. We have a short tutorial for importing APT into Matlab at http://www.thorlabs.com/tutorials/Thorlabs_APT_MATLAB.docx. dipankar.sarkar
 (posted 2013-05-08 06:15:29.13) PRM1/MZ8E: is it possible to switch of/reduce the backlash movement? Thanks. jlow
 (posted 2013-05-09 11:28:00.0) Response from Jeremy at Thorlabs: You can change/turn off the backlash correction movement at the end of every move. This setting is designed to help reduce the natural backlash of the stage and ensure all positions are approached from one direction. This can be changed in the settings menu in APT User. I will contact you directly to provide a screenshot for the location of that setting. ps2c11
 (posted 2013-03-06 04:35:01.02) Hi, I need to oscillate sinusoidally between two angles as requested by "steve.biedrzycki". From Thorlabs response to his question I suspect you had a potential solution to this problem. Would you be able to pass this information on to me too? cdaly
 (posted 2013-03-07 11:26:00.0) Response from Chris at Thorlabs: Thank you for using our web feedback. It is not possible to move the stage at a non-constant velocity profile within the APT software without first ending a move to change the velocity. i have not come across any way in third party software like LabView that would all this to be done either. teemu.hakala
 (posted 2013-02-11 14:12:19.25) Would it be possible to have an adapter plate to the PRM1 rotator? Plate should have SM1 threaded hole in the middle and threads/holes for 30 and 60mm cage systems. This would then be mounted to the backside of the rotator using the existing mounting holes on PRM1. This adapter would allow eg. having a fixed polarizer on one side of the rotator and rotating retarder on the other side. jlow
 (posted 2013-02-11 09:24:00.0) Response from Jeremy at Thorlabs: This adapter is not something that we have at the moment but I do see it as being quite useful. I will get in contact with you directly and discuss about possibly making this as a custom for you. bruno.ono
 (posted 2013-02-08 08:48:35.587) I like to know why PRM1Z8 dont work with program Thorlabs APT USER. I updated the program and when tried to rotate the stage with APT USER, it do not rotates, but on the TDC cube 001, it work perfectly.
The computer recognize the machine in USB port.
thank you
Bruno jlow
 (posted 2013-02-08 09:57:00.0) Response from Jeremy at Thorlabs: I apologize for the issue you are having with the PRM1Z8 and TDC001. I will contact you directly to troubleshoot this issue. tcohen
 (posted 2013-01-22 09:21:00.0) Response from Tim at Thorlabs: We have tested the radiated emission for a TDC001 when used with a Z8 motor (used inside the PRM1Z8E). Initial scans performed in a semi-anechoic screened room at a distance of 3m were sufficiently below the limit line that it was not considered necessary to move to an open area test site. I will send you our findings. olsonaj
 (posted 2013-01-14 14:58:44.337) I called and talked with a rep about this, but wanted to confirm. I am hoping to put this about a meter away from an experiment which is sensitive to magnetic fields.
Can you measure the steady state and transient (while moving) magnetic fields from this device both radial and axially?
Thanks jlow
 (posted 2012-10-03 11:09:00.0) Response from Jeremy at Thorlabs: The “Ident Resistor” pin is used to identify certain Thorlabs stages that are connected to our controller. There’s no index pulse for the PRM1Z8. There is only one limit switch on the PRM1Z8 and it is triggered when a silvered half-ball on the moving world makes contact with a corresponding notch on the fixed world. The default settings will ignore the limit switch during normal operation, however it will become active when the motor is being homed. user
 (posted 2012-09-28 17:50:31.0) Can you tell me for what pin 9 "Ident Resistor" stands for?
Does the rotational stage encoder have an "index" pulse for a home position?
Thanks in advance. tcohen
 (posted 2012-08-15 10:08:00.0) Response from Tim at Thorlabs: Grounding issues can cause the order to matter. Due to this we recommend following the connection procedure as outlined in the controller manual. First, please ensure that you close any APT software. Connect the TDC001 to the PC and only connect the power afterwards. After this, you can configure your motor and stage in APTConfig. If you have any other difficulties, our technical support team can assist you directly at techsupport@thorlabs.com. korea
 (posted 2012-08-14 10:32:15.0) I tried to use APT configuration utility after connecting the controller to pc. In the 'stage' tab, followed by 'Motor' field doesn't give any serial number(It show only 'none').
Also,
When I click APT user it pops up an error window saying that "Failed to load application setting. nconfiguration system failed to initialize"
Pleae help me out this. Thanks in advance. tcohen
 (posted 2012-06-12 14:02:00.0) Response from Tim at Thorlabs: Example VI’s for integrating into LabVIEW using the recommended TDC001 controller can be found on the distribution disk as well as on our “Software and Support” tab at http://www.thorlabs.com/software_pages/ViewSoftwarePage.cfm?Code=APT. You can also follow along with our guide at http://www.thorlabs.com/images/TabImages/GuideToLabVIEWandAPT.pdf which explains how to start interfacing within LabVIEW. Information on all of the method controls can be found in the APT Server Help at your downloaded directly > Thorlabs > APT > Help > APT Server Help. I will contact you for further support. tekavec
 (posted 2012-06-09 14:01:51.0) Do you have any example LabView VI's that control the PRM1Z8? I know there are the videos that show a few things with ActiveX, just wondering if you have anything else that could help me out. I'm trying to integrate moving the rotation stage into a another Labview program that I have. Thanks. tcohen
 (posted 2012-05-01 12:44:00.0) Response from Tim at Thorlabs to Philipp: I will contact you to provide detailed troubleshooting instructions. For any others who may experience a similar issue: please first try changing the homing direction to forward in APT. If this does not work, please try changing the association to the PRM1/Z7 in “APT Config”, running the stage and switching back to the PRM1/Z8. If neither of these solve the problem, it is possible that the limit switch needs evaluation. Please contact us at techsupport@thorlabs.com for further troubleshooting. philipp.bethge
 (posted 2012-05-01 17:35:52.0) hi
I have exactly the same problem as anne.hildenbrand:
-->
Hi, I am using a rotation stage PRM1/MZ8E with a TDC001 controller. Since I used manually, I am having problems homing the stage. It rotates and never stop. I try with other TDCOO1 cubes and the problem is the same. Can you help me ? Thanks in adavance.
please contact me as well
cheers
philipp james.beedell
 (posted 2012-04-12 12:31:23.0) Hi, Please can you tell me what temperature range the motor will work over and how long the cable that connects it to the control box is? Are different lengths available?
Thanks. tcohen
 (posted 2012-03-21 11:04:00.0) Response from Tim at Thorlabs: Thank you for contacting us. We have not captured MTBF data on this product and your results will be dependent on both your definition (out of specification or failure) and the environment of use. For example, some of the things that could fail are the motor, bearings and gearing. The bearings will depend on the duty cycle as well as the environment and the gearing wear will be dependent on load. I have contacted you to discuss your use and further discuss the MTBF. jeulin
 (posted 2012-03-16 03:35:54.0) Hi. What is the MTBF of the stage PRM1/MZ8? tcohen
 (posted 2012-02-29 10:15:00.0) Response from Tim at Thorlabs to Anne: Thank you for your feedback. This is either due to the homing settings or the physical limit switch. I have contacted you directly for troubleshooting. anne.hildenbrand
 (posted 2012-02-28 09:06:18.0) Hi, I am using a rotation stage PRM1/MZ8E with a TDC001 controller. Since I used manually, I am having problems homing the stage. It rotates and never stop. I try with other TDCOO1 cubes and the problem is the same. Can you help me ?
Thanks in adavance. bdada
 (posted 2011-06-20 17:31:00.0) Response from Buki at Thorlabs:
Thank you very much for your feedback. There are a couple things that you can check. Does the second computer have the APT software package installed completely? Does the hardware show up in the windows device manager? In the APT config setting of the second computer, make sure that you uncheck the "enable simulation mode". If you use a different PRM1-Z7 on the second computer, was the serial number set correctly in your program?
Please contact TechSupport@thorlabs.com if you need to continue troubleshooting this issue. greg
 (posted 2011-06-20 10:25:46.0) I have written a Labview vi to control the PRM1-Z7 and have tried to build an exe. to deploy on another computer. However the exe cannot recognise the motor on the other machine any reason for this or pointers to why this is happening? Customer Email: greg@novelpolymers.com This customer would like to be contacted. jjurado
 (posted 2011-05-13 09:31:00.0) Response from Javier at Thorlabs to last poster: Thank you very much for your feedback. We will modify the technical drawings to show the distances from the optical axis to the mounting holes of this rotation mount. Will will upload the drawing to the web once the changes have been made. In the meantime, please contact us at techsupport@thorlabs.com if you have any further questions or comments. user
 (posted 2011-05-05 17:57:20.0) Unless I am reading the drawing wrong, it seems that the AutoCad PDF for the PRM1Z8 does not have the distances from the optical axis to the mounting points labeled. This is actually the most important dimension, I think... miguel.araque
 (posted 2011-02-10 13:14:02.0) Hi,
We are having problems homing our stage: it just goes on spinning until we tell it to stop via APT-user. Full-stop also takes a while to reach (10 sec or so). We tried all possible combinations of limit switches/HW switches and homing directions to no avail. We tried with other TDC001 cubes, as we have three, and the problem persists.
Any feedback would we welcome. jjurado
 (posted 2011-02-02 14:44:00.0) Response from Javier at Thorlabs to jripoll: Thank you very much for submitting your inquiry. The BSC101 is not compatible with the PRM1Z8 rotation stage for two reasons:
(1) It is designed for stepper motor actuators.
The BDC101 is the recommended controller for high-current DC servo actuators.
(2) The high current output of the BSC/BDC series controllers exceeds the electrical input parameter of the Z8 actuators.
The recommended controller is the TDC001.
We will update our website to make this information clearer. jripoll
 (posted 2011-02-02 05:44:47.0) Can I control the PRM1Z8E with the high current BSC101 controller? tor
 (posted 2011-01-10 11:40:38.0) Response from Tor at Thorlabs to Will: The actual rotation of the stage would need to be measured independently in order to accurately determine the angular displacement from encoder counts. willtalmadge
 (posted 2010-12-23 04:54:47.0) In the specifications it says that there are 34,304 encoder counts per output shaft rotation. Im having trouble finding out how to convert output shaft revolutions to the stage angular displacement. Im familiar with the pitch value of 17.87. However, if I assume that is 17.87 degrees / shaft-rev I dont seem to get useful velocities in counts/sec to send to the TDC001 when instructing it to home. Plus that seems like a rather large value if I assume the shaft is a worm drive.
Ive read the LM628 documentation so Im familiar with how velocity is supposed to be calculated in counts/sample. Could someone perhaps clarify this so I can be converting velocity values is deg/sec to counts/sec in an accurate manner? tor
 (posted 2010-11-12 16:54:42.0) A response from Tor at Thorlabs: Thank you for your inquiry. While we have not tested this, our engineer indicates that this may be possible using MoveVelocity and stopprofiled commands. I will send command details to you directly. steve.biedrzycki
 (posted 2010-11-11 15:06:08.0) I need to do a sinusoidal variation between two angles. Is it possible to cycle between two positions without pausing with a non-linear velocity profile? What factors limit the cycle rate? Thorlabs
 (posted 2010-09-23 17:47:19.0) Response from Javier at Thorlabs to michaelorger: The PAA632 extension cable is compatible with the PRM1-Z7 rotation mount. michaelorger
 (posted 2010-09-23 11:49:53.0) Does the PAA632 work with the Z7 rotation mount? If not, is there an extension cable available for the Z7? Thanks user
 (posted 2010-05-06 12:32:01.0) A response from Oli at Thorlabs to Thomas:
Yes, Absolutely. You just need to set the limit switch settings to either ignore or home only and the display mode to continuous. Then it should work fine. thomas.juffmann
 (posted 2010-05-06 11:49:08.0) Hi,
can I run the prm1z8 continuously in one direction (more than one revolution?)? cheers. user
 (posted 2010-05-05 08:41:47.0) A response from Oliver at Thorlabs: It may be that you have not correctly configured the motor and driver in APT config, or the stage may have an error. Please feel free to contact me at techsupport.uk@thorlabs.com to disscuss the problem further. user
 (posted 2010-05-04 18:49:04.0) i think my problem is similar to lundeen below - i have this system and using the APT software gives unrepeatable position readouts. where can you put in a lookup table on the APT software? and can you account for this drift in the stage position? it seems like a lookup table wont solve this. ohoward
 (posted 2009-11-30 10:50:20.0) A response from Oliver at Thorlabs to jeff.lundeen:
The encoder output of the motor is used to give you the position output. An effective pitch that takes into account the gearing of the worm drive is used. To find the encoder count you divide the position by the pitch (17.87) and multiply the result by the encoder counts per rev (512). The encoder simply measures the rotation of the motor, not of the stage.
If you have sufficient measuring equipment you can calibrate the actual turn of the stage with the encoder count (or position output). Once you have created this lookup table APT config allows you to associate this calibration file with the stage. jeff.lundeen
 (posted 2009-11-23 18:18:06.0) I have the PRM1Z8 and the TDC001 controller. Does the user have access to the encoder output? How is the actual position determined? Unlike the linear motors, there is no encoder settings in the APT user software for the PRM1Z8, so it is not clear what role the encoder plays? e.g. can we calibrate the rotate vs encoder counts and then use this for more accurate movement (as is done in the linear motors)? klee
 (posted 2009-10-26 17:42:32.0) A response from Ken at Thorlabs to shalin.mehta: Unfortunately, we do not have any motorized rotation stage that can be used in the 60mm cage system. shalin.mehta
 (posted 2009-10-26 04:10:16.0) I need to use a motorized rotation mount inside a 60mm cage system. I want to mount a 1" optic in a light-path consisting of cage system and need to rotate the optic through computer. Is there a way of assembling above (or another) motorized rotation mount in 60mm cage system?
-Shalin klee
 (posted 2009-08-12 14:34:10.0) A response from Ken at Thorlabs to wu47: Yes, you can use LabView to control PRM1/MZ8E. There are video tutorials available on our website. http://www.thorlabs.com/tutorials/APTProgramming.cfm wu47
 (posted 2009-08-12 13:41:37.0) can I use labview to control PRM1/MZ8E? jens
 (posted 2009-06-02 20:03:30.0) A reply from Jens at Thorlabs: the 0.5 degree step size will not be a problem for the motorized PRM stage, so I am not entirely sure if you are referring to another degree of freedom like adding tip/tild in addition to the rotation. That would require a combination of the rotation stage with another element on top of it. As for the low temperature condensation could be a concern but we will not to check the requirements in detail. I will contact you directly to discuss all possible solutions. topasnadm
 (posted 2009-06-02 10:07:25.0) Do you have something similar to PRM1Z8 for which one can get 0.5 degree change in angle? It has to be motorized and go to low temperatures as well (approx 0F). Thank you. Tyler
 (posted 2008-10-22 11:11:20.0) A response from Tyler at Thorlabs to odd.england: The PRM1-Z7 is DC motor driven rotation stage and requires a DC Servo Motor driver with a computer interface in order to be controlled by a computer. The TDC001 is one of our DC servo motor drivers. It has a USB interface that comes with a fully functional graphical software interface and Active X controls for those that want to program their own interface. For assistance choosing the best driver for your application please contact our technical support team. Thank you for your interest in our motorized rotation stage. odd.england
 (posted 2008-10-21 14:14:36.0) hello, I was wondering if the PRM1-Z7 hooks directly up to a PC and if i were to hook it up to a PC, would i need the Servo Motor Controller? cheers. Laurie
 (posted 2008-10-07 09:04:10.0) Response from Laurie at Thorlabs to milan.vrastil: Thank you for your feedback. We have measured the accuracy of the angular position of the PRM1 to be 0.1 degrees. By this, we mean the sum of all uncertainties of the device including stiction/friction, influence of elastic deformations, windup and design resolution (not including backlash since we are only considering one direction of rotation). milan.vrastil
 (posted 2008-09-30 00:48:00.0) What is accuracy of angular position of PRM1? Tyler
 (posted 2008-06-19 11:15:30.0) A response from Tyler at Thorlabs to lsandstrom: The linear play of the rotating platform in the housing is +/- 0.00075" (19 um) worst case and +/-0.00025" (6um)best case. As a result the worst case eccentricity of a spot located one inch from the center of rotation would be 0.00075. I hope that this answers your question; if not, please post again. We appreciate your feedback. lsandstrom
 (posted 2008-06-17 07:12:15.0) What is the PRM1 wobble and eccentricity specification? |
Rotation Mount and Stage Selection Guide
Thorlabs offers a wide variety of manual and motorized rotation mounts and stages. Rotation mounts are designed with an inner bore to mount a Ø1/2", Ø1", or Ø2" optic, while rotation stages are designed with mounting taps to attach a variety of components or systems. Motorized options are powered by a DC Servo motor, 2 phase stepper motor, piezo inertia motor, or an Elliptec™ resonant piezo motor. Each offers 360° of continuous rotation.
Manual Rotation Mounts
Rotation Mounts for Ø1/2" Optics | |||||||
---|---|---|---|---|---|---|---|
Item # | MRM05(/M) | RSP05(/M) | CRM05 | PRM05(/M)a | SRM05 | KS05RS | CT104 |
Click Photo to Enlarge |
![]() |
![]() |
![]() |
![]() |
![]() |
![]() |
![]() |
Features | Mini Series | Standard | External SM1 (1.035"-40) Threads |
Micrometer | 16 mm Cage-Compatible | ±4° Kinematic Tip/Tilt Adjustment Plus Rotation | Compatible with 30 mm Cage Translation Stages and 1/4" Translation Stagesb |
Additional Details |
Rotation Mounts for Ø1" Optics | ||||||||
---|---|---|---|---|---|---|---|---|
Item # | RSP1(/M) | LRM1 | RSP1D(/M) | DLM1(/M) | CLR1(/M) | RSP1X15(/M) | RSP1X225(/M) | PRM1(/M)a |
Click Photo to Enlarge |
![]() |
![]() |
![]() |
![]() |
![]() |
![]() |
![]() |
![]() |
Features | Standard | External SM1 (1.035"-40) Threads |
Adjustable Zero | Two Independently Rotating Carriages | Rotates Optic Within Fixed Lens Tube System |
Continuous 360° Rotation or 15° Increments |
Continuous 360° Rotation or 22.5° Increments |
Micrometer |
Additional Details |
Rotation Mounts for Ø1" Optics | ||||||
---|---|---|---|---|---|---|
Item # | LM1-A & LM1-B(/M) |
CRM1T(/M) | CRM1LT(/M) | CRM1PT(/M) | KS1RS | K6XS |
Click Photo to Enlarge |
![]() ![]() |
![]() |
![]() |
![]() |
![]() |
![]() |
Features | Optic Carriage Rotates Within Mounting Ring | 30 mm Cage-Compatiblea | 30 mm Cage-Compatible for Thick Opticsa |
30 mm Cage-Compatible with Micrometera |
±4° Kinematic Tip/Tilt Adjustment Plus Rotation | Six-Axis Kinematic Mounta |
Additional Details |
Rotation Mounts for Ø2" Optics | |||||||
---|---|---|---|---|---|---|---|
Item # | RSP2(/M) | RSP2D(/M) | PRM2(/M) | LM2-A & LM2-B(/M) |
LCRM2A(/M) | KS2RS | K6X2 |
Click Photo to Enlarge | ![]() |
![]() |
![]() |
![]() ![]() |
![]() |
![]() |
![]() |
Features | Standard | Adjustable Zero |
Micrometer | Optic Carriage Rotates Within Mounting Ring | 60 mm Cage-Compatible | ±4° Kinematic Tip/Tilt Adjustment Plus Rotation | Six-Axis Kinematic Mount |
Additional Details |
Rotation Drive Mechanism and Adjustment Range | Manual, 360° Continuous | Coarse: Manual, 360° Continuous; Fine: ±7° Micrometer |
Manual, 360° Continuous | ||||
Optic Mounting | Internally SM2-Threaded Carriage | Internal SM2 Threads in LM2-A |
Internally SM2-Threaded Carriage | ||||
Maximum Accepted Optic Thickness | 0.51" (13 mm) | 0.54" (13.7 mm) | 0.48" (12.2 mm) | 0.46" (11.7 mm) | 0.52" (13.2 mm) | 0.47" (12 mm) | 0.53" (13.4 mm) |
Post Mounting | 8-32 (M4) Tap | 8-32 (M4) Tap in LM2-B | 8-32 (M4) Tap | Four Counterbores for 8-32 (M4) Cap Screws | Six Counterbores for 8-32 (M4) Cap Screws | ||
Cage System Compatibility | N/A | Four 4-40 (M3) Taps on Rotation Dial with 60 mm Spacing |
N/A | Four Bores for Ø6 mm Cage Rods with 60 mm Spacing |
N/A | N/A |
Manual Rotation Stages
Manual Rotation Stages | ||||||
---|---|---|---|---|---|---|
Item # | RP005(/M) | PR005(/M) | MSRP01(/M) | RP01(/M) | RP03(/M) | QRP02(/M) |
Click Photo to Enlarge |
![]() |
![]() |
![]() |
![]() |
![]() |
![]() |
Features | Standard | Two Hard Stops | ||||
Additional Details |
Manual Rotation Stages | ||||||
---|---|---|---|---|---|---|
Item # | XRNR1(/M) | XRR1(/M) | PR01(/M) | CR1(/M) | XYR1(/M) | OCT-XYR1(/M) |
Click Photo to Enlarge |
![]() |
![]() |
![]() |
![]() |
![]() |
![]() |
Features | Fine Rotation Adjuster and 2" Wide Dovetail Quick Connect |
Fine Rotation Adjuster and 3" Wide Dovetail Quick Connect |
Fine Rotation Adjuster and SM1-Threaded Central Aperture |
Fine Pitch Worm Gear | Rotation and 1/2" Linear XY Translation | |
Additional Details |
Motorized Rotation Mounts and Stages
Motorized Rotation Mounts and Stages with Central Clear Apertures | |||||
---|---|---|---|---|---|
Item # | DDR25(/M) | PDR1C(/M) | PDR1(/M) | PDR1V(/M) | PDXR1(/M) |
Click Photo to Enlarge |
![]() |
![]() |
![]() |
![]() |
![]() |
Features | Compatible with SM05 Lens Tubes, 16 mm Cage System, & 30 mm Cage System |
Compatible with 16 mm Cage System |
Compatible with SM05 Lens Tubes & 30 mm Cage System |
Vacuum-Compatible; Also Compatible with SM05 Lens Tubes & 30 mm Cage System |
Compatible with SM05 Lens Tubes & 30 mm Cage System |
Additional Details |
Motorized Rotation Mounts and Stages with Central Clear Apertures | |||||
---|---|---|---|---|---|
Item # | K10CR1(/M) | PRM1Z8(/M)a | DDR100(/M) | ELL14 | HDR50(/M) |
Click Photo to Enlarge |
![]() |
![]() |
![]() |
![]() |
![]() |
Features | Compatible with SM1 Lens Tubes & 30 mm Cage System | Compatible with SM1 Lens Tubes, 16 mm Cage System, 30 mm Cage System |
Compatible with SM1 Lens Tubes, Open Frame Design for OEM Applications |
Compatible with SM2 Lens Tubes |
|
Additional Details |
Motorized Rotation Mounts and Stages with Tapped Platforms | ||
---|---|---|
Item # | PRMTZ8(/M)a | ELL18(/M)b |
Click Photo to Enlarge |
![]() |
![]() |
Features | Tapped Mounting Platform for Mounting Prisms or Other Optics | Tapped Mounting Platform, Open Frame Design for OEM Applications |
Additional Details |

The central aperture of the PRM1Z8 rotation mount has a standard SM1 internal thread, for compatibility with a range of optics. Two SM1RR retaining rings are included to secure optical components in this aperture. The rotating platform features four 4-40 holes, four 8-32 (M4) holes and four 6-32 (M3) holes to allow for the addition of accessories. Please see the Mounting tab for all of the possible mounting options.
The PRM1Z8 is supplied with 19.6" (0.5 m) of cable. An 8 ft (2.5 m) extension cable (PAA632) is available separately.

The KPRM1E and KPRM1E/M bundles include a PRM1Z8 or PRM1/MZ8 Motorized Rotation Mount, respectively, with a KDC101 K-Cube™ DC Servo Motor Controller. This controller is an ideal companion for smooth, continuous motion that can be automated via the software interface. Each bundle ships complete with a KPS101* power supply and a location-specific adapter.
The KPRM1E(/M) is supplied with 19.6" (0.5 m) of cable. An 8 ft (2.5 m) extension cable (PAA632) is available separately.
*This previous-generation item is not available for individual purchase. If a replacement is needed, the KPS201 Power Supply can be used.

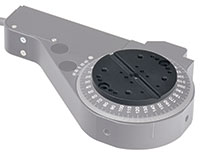
The rotating platform features several accessories. The central aperture has a standard SM1 internal thread, for compatibility with a range of optics. Four #4-40 holes are provided so that the PRM1Z8 can be incorporated into a cage system. Additional threaded mounting holes allow for the addition of accessories or post mounting.
The PRM1SP1 (PRM1SP1/M) accessory plate is fixed to the rotating top plate by two 6-32UNC (M3) bolts (supplied), allowing any of Thorlabs' standard 3 mm tongue & groove accessories (optic mounts, diode holders, fiber chucks etc) to be used. Using this plate, the total deck height becomes 1.1" (28 mm).
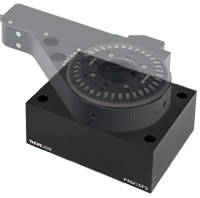
The PRM1SP3 base plate is similar to the PRM1SP2 described opposite, but delivers a total deck height of 2.26" (57.5 mm). If used together with the PRM1SP1 described above, the deck height is 2.43" (62.5 mm) and is compatibe with our range of 3-axis stages (NanoMax, MicroBlock, and RollerBlock).
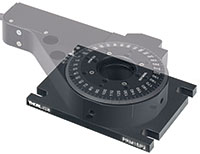
The PRM1SP2 base plate is used to provide a more stable installation solution, with a deck height of 1.15" (29 mm). If used together with the PRM1SP1 described above, the deck height is 1.32" (34 mm).

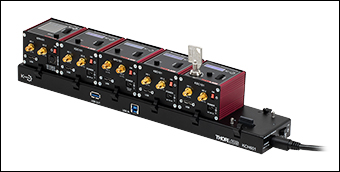
KCH601 USB Controller Hub (Sold Separately) with Installed K-Cube™ Modules
- Front Panel Velocity Wheel and Digital Display for Controlling Motorized Stages or Actuators
- Two Bidirectional Trigger Ports to Read or Control External Equipment
- Interfaces with Computer Using Included USB Cable
- Fully Compatible with Kinesis® Software Package
- Compact Footprint: 60.0 mm x 60.0 mm x 49.2 mm (2.42" x 2.42" x 1.94")
- Power Supply Not Included (See Below)
Thorlabs' KDC101 K-Cube Brushed DC Motor Controller provides local and computerized control of a single motor axis. It features a top-mounted control panel with a velocity wheel that supports four-speed bidirectional control with forward and reverse jogging as well as position presets. A backlit digital display is also included that can have the backlit dimmed or turned off using the top-panel menu options. The front of the unit contains two bidirectional trigger ports that can be used to read a 5 V external logic signal or output a 5 V logic signal to control external equipment. Each port can be independently configured.
The unit is fully compatible with our Kinesis software package. Please see the Kinesis Software tab for more information.
Please note that this controller does not ship with a power supply. Compatible power supplies are listed below. Additional information can be found on the main KDC101 DC Servo Motor Controller page.

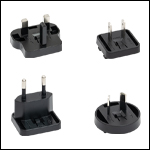
Click for Details
Each KPS201 power supply includes one region-specific adapter, which can be selected upon checkout.
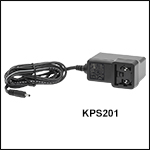
Click to Enlarge
The KPS201 Power Supply Unit
- Individual Power Supply
- KPS201: For K-Cubes™ or T-Cubes™ with 3.5 mm Jacks
- USB Controller Hubs Provide Power and Communications
- KCH301: For up to Three K-Cubes or T-Cubes
- KCH601: For up to Six K-Cubes or T-Cubes
The KPS201 power supply outputs +15 VDC at up to 2.66 A and can power a single K-Cube or T-Cube with a 3.5 mm jack. It plugs into a standard wall outlet.
The KCH301 and KCH601 USB Controller Hubs each consist of two parts: the hub, which can support up to three (KCH301) or six (KCH601) K-Cubes or T-Cubes, and a power supply that plugs into a standard wall outlet. The hub draws a maximum current of 10 A; please verify that the cubes being used do not require a total current of more than 10 A. In addition, the hub provides USB connectivity to any docked K-Cube or T-Cube through a single USB connection.
For more information on the USB Controller Hubs, see the full web presentation.