Motorized Kinematic Mount
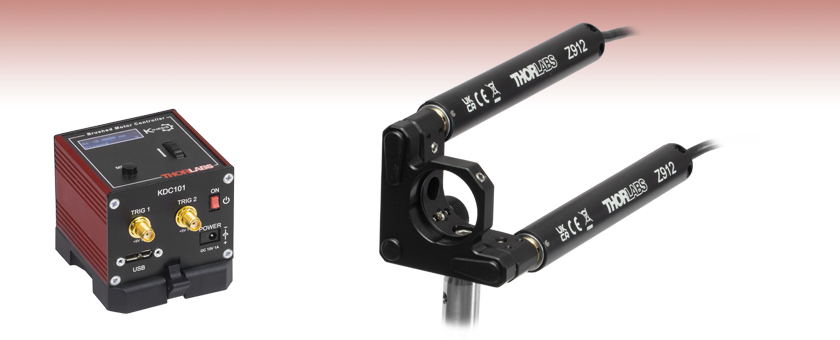
- Motorized Tip/Tilt Ø1" Mirror Mount
- Ideal for OEM Applications
KDC101
Controller for
the KS1-Z9
(2 Required,
Shown with Included Mounting Plate)
KS1-Z9
Motorized Kinematic Mount

Please Wait
Features
- Ultra Stable Ø1" Mirror Mounts
- Two Motorized Actuators, One Manual Actuator
- ±4° Pitch and Yaw Adjustment
Thorlabs offers the popular Ultra-Stable KS1 Ø1" mirror mount in a motorized version. The KS1-Z9 mount comes with two of our Z912 12 mm Motorized Actuators and includes a 1/4"-80 threaded adjuster, which allows for greater pitch and yaw adjustment over standard two adjuster mounts. The mount is fabricated from black anodized aluminum.
The two Z912 DC Actuators are equipped with commercial grade internal limit switches to provide overdrive protection. The motors also have an encoder to provide 1.1 arcsec angular step size. Two KDC101 K-Cube™ DC servo motor controllers are required for use with KS1-Z9 motorized mount, one for each channel. The KDC101 and compatible power supplies are not included with the motorized kinematic mount, but are available below.
Please refer to the Actuator Specs tab for more information on these motorized actuators.
Z912 Actuators
Item # | Z912 |
---|---|
Mounting Barrel | 1/4"-80 Threaded |
Travel Range | 12 mm (0.47") |
Encoder Resolutiona | 34,555 counts/mm (Linear Displacement) |
Maximum Pushing Force | 45 N |
Homing Repeatability | ±6 µm |
Uncompensated Backlash | 13 µm |
Uncompensated Bidirectional Repeatability | ±7 µm |
Residual Backlash After Compensationb | 0.7 µm |
Compensated Bidirectional Repeatability | ±0.7 µm |
Travel Accuracyc | 9 µm |
Minimum Repeatable Incremental Movement | 0.2 µm |
Maximum Speedd | 2.6 mm/s |
Maximum Acceleration | 4 mm/s2 |
Maximum Phase to Phase Resistance | 33.0 Ω (Max) |
Maximum Phase to Phase Inductance | 0.6 mH (Max) |
Tested Lifetimee | >100,000 Cycles |
Operating Temperature Range | 41 to 104 °F (5 to 40 °C) |
Weight | 0.13 kg |
Motor Typef | DC Servo |
Cable Length | 485.0 mm (19.09") |
Required Controller | KDC101 |
How to Calculate the Linear Displacement per Encoder Count
For the Z912, there are 512 encoder counts per revolution of the motor. The output shaft of the motor goes into a 67.49:1 planetary gear head. This requires the motor to rotate 67.49 times to rotate the 1.0 mm pitch lead screw one revolution. The end result is the lead screw advances by 1.0 mm.
The linear displacement of the actuator per encoder count is given by
512 x 67.49 = 34,555 encoder counts per revolution of the lead screw,
whereas the linear displacement of the lead screw per encoder count is given by
1.0 mm / 34,555 counts = 2.9 x 10-5 mm (29 nm).
Software
Kinesis Version 1.14.49
The Kinesis Software Package, which includes a GUI for control of Thorlabs' Kinesis system controllers.
Also Available:
- Communications Protocol
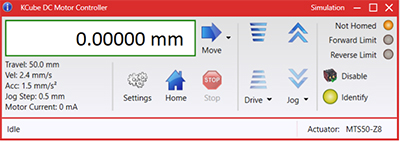
Kinesis GUI Screen
Thorlabs offers the Kinesis® software package to drive our wide range of motion controllers. The software can be used to control devices in the Kinesis family, which covers a wide variety of motion controllers ranging from small, low-powered, single-channel drivers (such as the K-Cubes™) to high-power, multi-channel benchtop units and modular 19" rack nanopositioning systems (the MMR60x Rack System).
The Kinesis Software features .NET controls which can be used by 3rd party developers working in the latest C#, Visual Basic, LabVIEW™, or any .NET compatible languages to create custom applications. Low-level DLL libraries are included for applications not expected to use the .NET framework and APIs are included with each install. A Central Sequence Manager supports integration and synchronization of all Thorlabs motion control hardware.
By providing this common software platform, Thorlabs has ensured that users can mix and match any of our motion control devices in a single application, while only having to learn a single set of software tools. In this way, it is perfectly feasible to combine any of the controllers from single-axis to multi-axis systems and control all from a single, PC-based unified software interface.
The software package allows two methods of usage: graphical user interface (GUI) utilities for direct interaction with and control of the controllers 'out of the box', and a set of programming interfaces that allow custom-integrated positioning and alignment solutions to be easily programmed in the development language of choice.
Legacy Software
Select products are still capable of running the legacy APT™ software package. Information on software compatibility can be found in the product documentation (), and additional details about the APT software can be found here.
Posted Comments: | |
cbrideau
 (posted 2013-09-17 19:03:38.147) I REALLY need this in a KCB1 for use in a cage setup. Is it possible to fit a KCB1 with a pair of Z8's as a new product proposal or a custom job? It would save me a lot of trouble if it could be done. Also, are Z812's necessary? Will a Z86 do the job? jlow
 (posted 2013-09-19 16:14:00.0) Response from Jeremy at Thorlabs: We do not currently have a motorized KCB1 but we will look at possibly modifying our current KCB1 for use with the Z806. The Z812 is necessary in the KS1 mount because it would not provide the necessary travel for the adjustment range when the corner adjustment screw is screwed in by a significant amount. I will contact you directly regarding possibly customizing the KCB1 with motors. Thorlabs
 (posted 2010-12-06 10:17:10.0) Response from Javier at Thorlabs to k1w05: the ZST13 actuator is compatible with the KS2 kinematic mirror mount. Also, the ZST actuators include forward and reverse mechanical limit switches in order to prevent overshooting in the travel. k1w05
 (posted 2010-12-05 07:37:38.0) I want to used KS2 with ZST13, is they work. Can you install an Electro-Mechanical Limit Switching to Prevent Motor Damage? Thank you! Tyler
 (posted 2009-03-12 10:43:01.0) A response from Tyler at Thorlabs to John: Our APT DC Servo Motor Driver Controllers come with a software package that includes a graphical computer interface that can be used to control and monitor the servo motor. This interface only provides the linear position of the actuator. However, the software package includes all of the necessary drivers to easily build your own interface using a program like LabVIEW. Your program could include a calibration routine that converted the linear actuator position into an angular position that could be displayed real-time on the computer screen. I will have a member of our technical support department contact you with more information about this possibility. john.wang
 (posted 2009-03-05 13:39:05.0) Is there angular readout on this DC Servo Motorized Mirror Mounts?
I am looking for the automated gimble mirror mount with readout that can display the anguler moving.
John Wang |

- Motorized ±4° Tip/Tilt Adjustment
- Angular Step Size (Repeatable): 1.1 arcsec (5.3 µrad)
- 34,555 counts/revolutions Rotary Encoder
- Commercial-Grade Limit Switches Prevent Motor Damage
- Required (Not Included, Sold Separately Below):
- Two KDC101 Brushed DC Servo Motor Controllers
- Power Supply
The KS1-Z9 features an Ultra-Stable KS1 Ø1" mirror mount and combines it with two Z912 12 mm Motorized Actuators. Higher precision adjustments can be made with the motorized actuators than with manual adjusters. The mount also features one 1/4"-80 adjuster, which allows for greater pitch and yaw adjustment over standard two adjuster kinematic mounts, while also providing Z-translation. This manual adjuster can be removed and replaced with a motorized actutor, for full motorized adjustment (see the photo to the right).

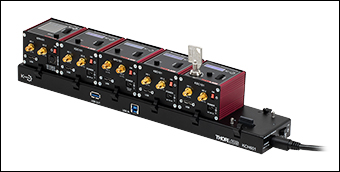
KCH601 USB Controller Hub (Sold Separately) with Installed K-Cube™ Modules
- Front Panel Velocity Wheel and Digital Display for Controlling Motorized Stages or Actuators
- Two Bidirectional Trigger Ports to Read or Control External Equipment
- Interfaces with Computer Using Included USB Cable
- Fully Compatible with Kinesis® Software Package
- Compact Footprint: 60.0 mm x 60.0 mm x 49.2 mm (2.42" x 2.42" x 1.94")
- Power Supply Not Included (See Below)
Thorlabs' KDC101 K-Cube Brushed DC Motor Controller provides local and computerized control of a single motor axis. It features a top-mounted control panel with a velocity wheel that supports four-speed bidirectional control with forward and reverse jogging as well as position presets. A backlit digital display is also included that can have the backlit dimmed or turned off using the top-panel menu options. The front of the unit contains two bidirectional trigger ports that can be used to read a 5 V external logic signal or output a 5 V logic signal to control external equipment. Each port can be independently configured.
The unit is fully compatible with our Kinesis software package. Please see the Kinesis Software tab for more information.
Please note that this controller does not ship with a power supply. Compatible power supplies are listed below. Additional information can be found on the main KDC101 DC Servo Motor Controller page.

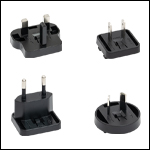
Click for Details
Each KPS201 power supply includes one region-specific adapter, which can be selected upon checkout.
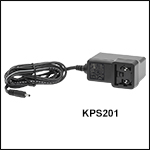
Click to Enlarge
The KPS201 Power Supply Unit
- Individual Power Supply
- KPS201: For K-Cubes™ or T-Cubes™ with 3.5 mm Jacks
- USB Controller Hubs Provide Power and Communications
- KCH301: For up to Three K-Cubes or T-Cubes
- KCH601: For up to Six K-Cubes or T-Cubes
The KPS201 power supply outputs +15 VDC at up to 2.66 A and can power a single K-Cube or T-Cube with a 3.5 mm jack. It plugs into a standard wall outlet.
The KCH301 and KCH601 USB Controller Hubs each consist of two parts: the hub, which can support up to three (KCH301) or six (KCH601) K-Cubes or T-Cubes, and a power supply that plugs into a standard wall outlet. The hub draws a maximum current of 10 A; please verify that the cubes being used do not require a total current of more than 10 A. In addition, the hub provides USB connectivity to any docked K-Cube or T-Cube through a single USB connection.
For more information on the USB Controller Hubs, see the full web presentation.