Alignment Screens
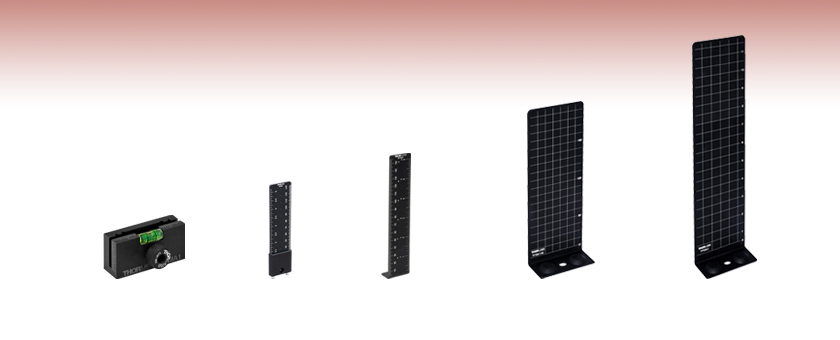
- Laser Engraved Screens with Target Grid
- 5" (130 mm), 6" (155 mm) and 12" (305 mm) Rulers with Through Holes
- Magnets Hold Screens to Optical Table or Breadboard
TPSM1/M
200 mm (7.87")
Laser Safety Screen
(10 mm Target Grid)
TPSM2
11.81" (300 mm)
Laser Safety Screen
(1/2" Target Grid)
BHMA1
Mounting Bracket for Beam Height Rulers
BHM3
6" (155 mm) Magnetic Beam Height Ruler
BHM6
5" (130 mm) Magnetic Beam Height Ruler with Pins

Please Wait
Made from anodized aluminum, the TPSM1(/M) and TPSM2(/M) Alignment Screens have been laser engraved with a target grid to assist in the alignment and height measurement of a beam. For more permanent mounting to magnetic or nonmagnetic surfaces, each screen also has a mounting slot for a 1/4"-20 or M6 cap screw.
The BHM3 and BHM4 Magnetic Beam Height Rulers feature holes at 25 mm and 1" intervals to allow a laser beam to pass through. The BHM6 Magnetic Beam Height Ruler with Pins features holes at 0.25", 5.00 mm, and 10.00 mm intervals to allow a laser beam to pass through. Additionally, it has a pair of dowels that fit into the holes of optical tables or breadboards with 1" or 25.0 mm hole spacings. All rulers are laser engraved with both imperial and metric scales.
All alignment screens and beam height rulers feature either a single (BHM3) or a pair (TPSM1(/M), TPSM2(/M), BHM4, and BHM6) of magnets in their base to enable quick placement on and removal from optical tables or breadboards.
Two beam height rulers can be attached at a 90° angle using the BHMA1 Mounting Bracket, allowing for horizontal alignment of a laser beam in addition to measuring its height off the table.
Insights into Aligning a Laser Beam
When installing a laser in an optical setup, it is good practice to start by leveling and orienting its beam so that it travels along a well-defined path. When the beam is prepared this way, not only is it easier to then divert the beam and route it through the optical elements in the system, but the results provided by tuning the system's alignment are more predictable and repeatable. The following sections describe how to:
- Level and Align the Laser Beam's Pointing Angle
- Divert the Beam and Align it to Follow a Desired Path
Click here for more Insights about lab practices and equipment.
Level and Align the Laser Beam's Pointing Angle
0:00 - Introduction
1:25 - Level and Align the Laser Beam's Pointing Angle
4:09 - Divert the Beam and Align it to Follow a Desired Path
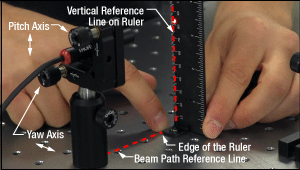
Click to Enlarge
Figure 2: The beam can be aligned to travel parallel to a line of tapped holes in the optical table. The yaw adjustment on the kinematic mount adjusts the beam angle, so that the beam remains incident on the ruler's vertical reference line as the ruler slides along the line of tapped holes.
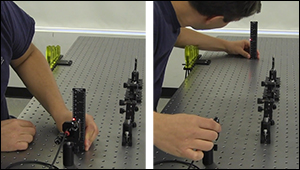
Click to Enlarge
Figure 1: Leveling the beam path with respect to the surface of an optical table requires using the pitch adjustment on the kinematic laser mount (Figure 2). The beam is parallel to the table's surface when measurements of the beam height near to (left) and far from (right) the laser's front face are equal.
Pitch (tip) and yaw (tilt) adjustments provided by a kinematic mount can be used to make fine corrections to a laser beam's angular orientation or pointing angle. This angular tuning capability is convenient when aligning a collimated laser beam to be level with respect to a reference plane, such as the surface of an optical table, and when aligning with respect to a particular direction in that plane, such as along a line of tapped holes in the table.
Before Using the Mount's Adjusters
First, rotate each adjuster on the kinematic mount to the middle of its travel range. This reduces the risk of running out of adjustment range, and the positioning stability is frequently better when at the center of an adjuster's travel range.
Then, make coarse corrections to the laser's height, position, and orientation. This can be done by adjusting the optomechanical components, such as a post and post holder, supporting the laser. Ensure all locking screws are tightened after the adjustments are complete.
Level the Beam Parallel to the Table's Surface
Leveling the laser beam is an iterative process that requires an alignment tool and the fine control provided by the mount's pitch adjuster.
Begin each iteration by measuring the height of the beam close to and far from the laser (Figure 1). A larger distance between the two measurements increases accuracy. If the beam height at the two locations differs, place the ruler in the more distant position. Adjust the pitch on the kinematic mount until the beam height at that location matches the height measured close to the laser. Iterate until the beam height at both positions is the same.
More than one iteration is necessary, because adjusting the pitch of the laser mount adjusts the height of the laser emitter. In the video for example, the beam height close to the laser was initially 82 mm, but it increased to 83 mm after the pitch was adjusted during the first iteration.
If the leveled beam is at an inconvenient height, the optomechanical components supporting the laser can be adjusted to change its height. Alternatively, two steering mirrors can be placed after the laser and aligned using a different procedure, which is detailed in the section. Steering mirrors are particularly useful for adjusting beam height and orientation of a fixed laser.
Orient the Beam Along a Row of Tapped Holes
Aligning the beam parallel to a row of tapped holes in the table is another iterative process, which requires an alignment tool and tuning of the mount's yaw adjuster.
The alignment tool is needed to translate the reference line provided by the tapped holes into the plane of the laser beam. The ruler can serve as this tool, when an edge on the ruler's base is aligned with the edges of the tapped holes that define the line (Figure 2).
The relative position of the beam with respect to the reference line on the table can be evaluated by judging the distance between the laser spot and vertical reference feature on the ruler. Vertical features on this ruler include its edges, as well as the columns formed by different-length rulings. If these features are not sufficient and rulings are required, a horizontally oriented ruler can be attached using a BHMA1 mounting bracket.
In the video, when the ruler was aligned to the tapped holes and positioned close to the laser, the beam's edge and the ends of the 1 mm rulings coincided. When the ruler was moved to a farther point on the reference line, the beam's position on the ruler was horizontally shifted. With the ruler at that distant position, the yaw adjustment on the mount was tuned until the beam's edge again coincided with the 1 mm rulings. The ruler was then moved closer to the laser to observe the effect of adjusting the mount on the beam's position. This was iterated as necessary.
Divert the Beam and Align it to Follow a Desired Path
The first steering mirror reflects the beam along a line that crosses the new beam path. A second steering mirror is needed to level the beam and align it along the new path. The procedure of aligning a laser beam with two steering mirrors is sometimes described as walking the beam, and the result can be referred to as a folded beam path. In the example shown in the video above, two irises are used to align the beam to the new path, which is parallel to the surface of the optical table and follows a row of tapped holes.
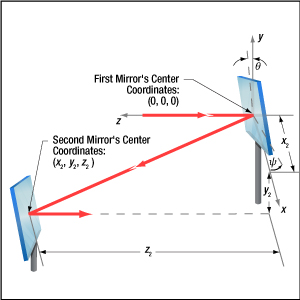
Click to Enlarge
Figure 3: The beam reflected from Mirror 1 will be incident on Mirror 2, if Mirror 1 is rotated around the x- and y-axes by angles θ and ψ, respectively. Both angles affect each coordinate (x2 , y2 , z2 ) of Mirror 2's center. Mirror 1's rotation around the x-axis is limited by the travel range of the mount's pitch (tip) adjuster, which limits Mirror 2's position and height options.
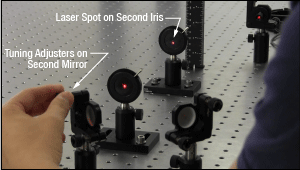
Click to Enlarge
Figure 5: The adjusters on the second kinematic mirror are used to align the beam on the second iris.
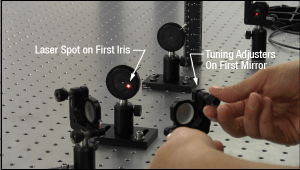
Click to Enlarge
Figure 4: The adjusters on the first kinematic mirror mount are tuned to position the laser spot on the aperture of the first iris.
Setting the Heights of the Mirrors
The center of the first mirror should match the height of the input beam path, since the first mirror diverts the beam from this path and relays it to a point on the second mirror. The center of the second mirror should be set at the height of the new beam path.
Iris Setup
The new beam path is defined by the irises, which in the video have matching heights to ensure the path is level with respect to the surface of the table. A ruler or calipers can be used to set the height of the irises in their mounts with modest precision.
When an iris is closed, its aperture may not be perfectly centered. Because of this, switching the side of the iris that faces the beam can cause the position of the aperture to shift. It is good practice to choose one side of the iris to face the beam and then maintain that orientation during setup and use.
Component Placement and Coarse Alignment
Start by rotating the adjusters on both mirrors to the middle of their travel ranges. Place the first mirror in the input beam path, and determine a position for the second mirror in the new beam path (Figure 3). The options are notably restricted by the travel range of the first mirror mount's pitch (tip) actuator, since it limits the mirror's rotation (θ ) around its x-axis. In addition to the pitch, the yaw (tilt) of the first mirror must also be considered when choosing a position
After placing the second mirror on the new beam path, position both irises after the second mirror on the desired beam path. Locate the first iris near the second mirror and the second iris as far away as possible.
While maintaining the two mirrors' heights and without touching the yaw adjusters, rotate the first mirror to direct the beam towards the second mirror. Adjust the pitch adjuster on the first mirror to place the laser spot near the center of the second mirror. Then, rotate the second mirror to direct the beam roughly along the new beam path.
First Hit a Point on the Path, then Orient
The first mirror is used to steer the beam to the point on the second mirror that is in line with the new beam path. To do this, tune the first mirror's adjusters while watching the position of the laser spot on the first iris (Figure 4). The first step is complete when the laser spot is centered on the iris' aperture.
The second mirror is used to steer the beam into alignment with the new beam path. Tune the adjusters on the second mirror to move the laser spot over the second iris' aperture (Figure 5). The pitch adjuster levels the beam, and the yaw adjuster shifts it laterally. If the laser spot disappears from the second iris, it is because the laser spot on the second mirror has moved away from the new beam path.
Tune the first mirror's adjusters to reposition the beam on the second mirror so that the laser spot is centered on the first iris' aperture. Resume tuning the adjusters on the second mirror to direct the laser spot over the aperture on the second iris. Iterate until the laser beam passes directly through the center of both irises, as shown in the video. If any adjuster reaches, or approaches, a limit of its travel range, one or both mirrors should be repositioned and the alignment process repeated.
If a yaw axis adjuster has approached a limit, note the required direction of the reflected beam and then rotate the yaw adjuster to the center of its travel range. Turn the mirror in its mount until the direction of the reflected beam is approximately correct. If the mirror cannot be rotated, reposition one or both mirrors to direct the beam roughly along the desired path. Repeat the alignment procedure to finely tune the beam's orientation.
If a pitch axis adjuster has approached a limit, either increase the two mirrors' separation or reduce the height difference between the new and incident beam paths. Both options will result in the pitch adjuster being positioned closer to the center of its travel range after the alignment procedure is repeated.
Posted Comments: | |
williamg
 (posted 2016-02-12 15:49:47.28) I have an improvement suggestion for the family of vertical rulers like BHM1 etc. It would be nice if both sides had the scales, but the back side had the metric and imperial scales switched. In other words, when you look on one face, it's imperial scale on the left, but when you look on the other face, it's metric scale on the left. This would be very useful in crowded optical setups, when it's inconvenient or impossible to set up the ruler to use the desired scale.
It would also be nice to have an option to buy a vertical ruler (like BHM1) that has both magnetic feet on the same side (like TPSM1 does). I often need to take height measurements inside a laser, where floor space is very limited, and feet on opposite sides make it very difficult sometimes. Such ruler, with both scales on both sides, like described in the first paragraph, would be very nice to have, indeed. cevered
 (posted 2016-02-16 10:25:44.0) Thank you very much for your valuable product feedback. I have begun a discussion within our internal ideas forum and we will inform you of any new releases or suggestions that may arise from your feedback. christoph.testud
 (posted 2015-05-20 15:52:27.753) Dear Sir or Madam,
we are using the alignment screens in our laser lab and would suggest that the magnet in the base do not need to be so strong. If you is not careful the screen can easily snap onto the optical table.
Best regards,
Christoph Testud
Christoph Testud
University of Hamburg
Center for Free Electron Laser Science (CFEL)
Geb. 99, office 02-129
Luruper Chaussee 149
22761 Hamburg
Tel.: +49 (0)40 8998 6287
christoph.testud@uni-hamburg.de msoulby
 (posted 2015-05-26 06:50:44.0) Response from Mike at Thorlabs: The laser safety screens are designed to be used on steel optical tables, we used magnets rather than screw slots in order to give the customer greater flexibility when placing the screen. The magnets are strong in order to help prevent the safety screen from being knocked and moving easily, which could be a potential hazard if you are using the screen to block a beam. |

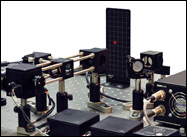
Click to Enlarge
TPSM1 in a Beam Stabilization Setup
- Aluminum Laser Safety Screen with Laser-Engraved Target Grid
- Available in Two Sizes:
- TPSM1(/M): 7.87" x 2.95" (200.0 mm x 75.0 mm), Footprint: 2.95" x 1.38" (75.0 mm x 35.0 mm)
- TPSM2(/M): 11.81" x 2.95" (300.0 mm x 75.0 mm), Footprint: 2.95" x 1.38" (75.0 mm x 35.0 mm)
- Two Magnets on Underside Provide Holding Force
- Slotted Mounting Hole for Non-Magnetic Surfaces
- Homogeneously Diffusive Anodized Coating
- Damage Threshold: >350 J/cm2 (1064 nm, 20 ns, 20 Hz, Ø1.14 mm)
Our Magnetic Laser Safety Screens are laser engraved on one side with a 1/2" (10 mm for metric versions) target grid for rough laser alignment, while the other side is blank to provide a complete beam blocking option. The base of the screen is fitted with a pair of magnets that hold the screen to magnetic work surfaces and provide flexibility of movement. A through hole is also provided to allow the screen to be tightened down using a cap screw for more permanent placement or for use in non-magnetic applications. The compact size of the screen allows it to fit into small gaps between your accessories, enabling easy integration into a laser setup. This screen is constructed from bead-blasted aluminum to remove any sharp edges, which is then anodized to create a homogeneously diffusive surface.
Please note: Due to the presence of strong magnets, these laser screens should not be used in the vicinity of pacemakers, credit cards, or other devices affected by magnetic fields.

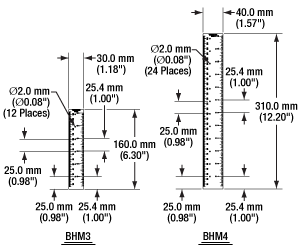
Click to Enlarge
Each ruler has holes next to the major ticks of the metric and imperial scales to allow a laser beam to pass through.
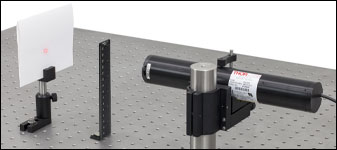
Click to Enlarge
Light from a HeNe Laser Passing Through a Hole in a BHM3 Ruler
- Imperial and Metric Laser Engraved Scales
- 1.0 mm Metric Graduations
- 1/16" Imperial Graduations
- Facilitate Laser Beam Alignment Using Holes Spaced at 1" and 25 mm Intervals
- Measure Beam Height on Magnetic Optical Tables or Breadboards
- Neodymium Magnets Provide Holding Force
- Homogeneously Diffusive Anodized Coating
Our BHM3 and BHM4 Magnetic Rulers measure beam heights up to 6" (155 mm) or 12" (305 mm), respectively. The front of the screen is laser engraved with 1.0 mm and 1/16" graduations for beam height measurement. A series of twelve or twenty four Ø2.0 mm (Ø0.08") holes (on the BHM3 and BHM4 respectively) are positioned next to the engraved numbers at 25.0 mm and 1.00" intervals to allow a laser beam to pass through the ruler.
The base of each ruler is fitted with either one or two neodymium magnets that hold the ruler to magnetic work surfaces and provide flexibility of movement when compared to an option that is bolted to the table. The BHM3 has one of these magnets, while the BHM4 has a pair. Both rulers are constructed from bead-blasted aluminum to remove any sharp edges and then anodized to create a homogeneously diffusive surface. The compact size allows the tool to fit into small gaps between components, enabling easy integration into a setup.
We also offer the BHMA1 bracket below for attaching two beam height rulers, allowing for the alignment of a laser beam horizontally in addition to measuring its height off the table.
Please note: Due to the presence of magnets, this ruler should not be used in the vicinity of pacemakers, credit cards, or other devices affected by magnetic fields.
Item # | Ruler Surface Dimensions (W x H) |
Footprint (L x W) |
Thickness | Numbered Graduations |
Graduations | Hole Spacing |
Hole Diameter |
Damage Threshold |
---|---|---|---|---|---|---|---|---|
BHM3 | 30 mm x 160 mm (1.18" x 6.30") |
20 mm x 30 mm (0.79" x 1.18") |
2.0 mm (0.8") |
Every 1" and 10 mm | 1/16" and 1.0 mm | 1.00" and 25.0 mm | 2.0 mm (0.08") |
>350 J/cm2 (1064 nm, 20 ns, 20 Hz, Ø1.14 mm) |
BHM4 | 40 mm x 310 mm (1.57" x 12.20") |
20 mm x 40 mm (0.79" x 1.57") |

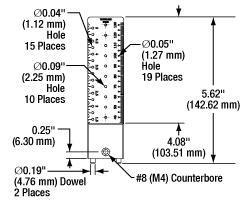
Click for Details
The ruler has holes next to the major ticks of the
imperial and metric scales, as well as along the center line of the ruler, to allow a laser beam to pass through.
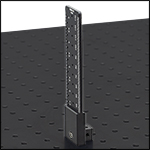
Click to Enlarge
When using non-magnetic surfaces, an MSCB3(/M) cube can be secured to the back of the ruler for increased stability.
- Imperial and Metric Laser Engraved Scale
- 1.0 mm Metric Graduations
- 1/16" Imperial Graduations
- Facilitate Laser Beam Alignment Using Holes Spaced at 0.25", 5.00 mm, and 10.00 mm Intervals
- Dowel Pins for Aligning to Holes of Optical Tables or Breadboards
- Neodymium Magnets Provide Holding Force
Our BHM6 Magnetic Ruler with Dowel Pins can be used to measure beam heights up to 5" (130 mm). The ruler body is constructed from anodized aluminum, and both sides are laser engraved with 1.0 mm and 1/16" graduations. A series of holes are positioned next to the imperial and metric graduations, as well as at intervals along the center of the ruler, to allow a laser beam to pass through. For hole diameters and spacing, please refer to the drawing to the right.
The base of the ruler has a pair of dowel pins that fit into the holes of optical tables or breadboards with 1" or 25.0 mm hole spacings. Two neodymium magnets in the base provide increased stability when the ruler is used on magnetic surfaces. A #8 (M4) counterbore allows an MSCB3(/M) cube to be mounted on the rear of the part, as depicted in the image to the right, providing extra stability to setups that are not assembled on a magnetic surface. The ruler's compact size allows it to fit into small gaps between components, enabling easy integration into a setup.
Unlike the BHM3 and BHM4 rulers, the surface of this ruler is not bead-blasted prior to anodization and additional specular reflection of incident beams may occur.
Please note: Due to the presence of magnets, this ruler should not be used in the vicinity of pacemakers, credit cards, or other devices affected by magnetic fields.
Item # | Ruler Surface Dimensions (W x H) |
Footprint (L x W) |
Thickness | Numbered Graduations |
Graduations | Hole Diameter and Spacing |
Damage Threshold |
---|---|---|---|---|---|---|---|
BHM6 | 1.38" x 4.08" (35.05 mm x 103.51 mm) |
0.38" x 1.38" (9.55 mm x 35.05 mm) |
0.13" (3.18 mm)a |
Every 1/2" and 10 mm |
1/16" and 1.0 mm |
1.12 mm (0.04") with 0.25" Spacing, 1.27 mm (0.05") with 5.00 mm Spacing, 2.25 mm (0.09") with 10.00 mm Spacing |
>350 J/cm2 (1064 nm, 20 ns, 20 Hz, Ø1.14 mm) |

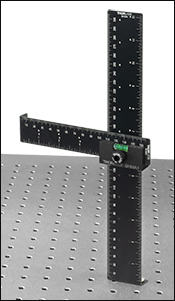
Click to Enlarge
BHM3 Ruler Mounted at 90° on a BHM4 Ruler Using the BHMA1 Bracket
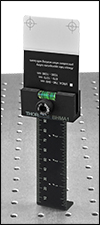
Click to Enlarge
VRC4 IR Detector Card on a BHM3 Ruler
- Mount Two Beam Height Rulers Perpendicularly
- Ideal for Horizontal and Vertical Beam Measurements
- Mount a Laser Viewing Card to a Beam Height Ruler
- Built-In Spirit Level Simplifies Leveling of the Mounted Card or Ruler
- Laser Engraved with 1.0 mm Graduations
- Constructed From Black Delrin®*
Thorlabs' BHMA1 Mounting Bracket allows two beam height rulers to be attached at a 90° angle. This capability allows for alignment of a laser beam horizontally in addition to measuring its height off the table. As shown in the image to the right, the bracket can also be used to attach Laser Viewing Cards to a ruler, allowing for the viewing of UV, NIR, or MIR beams.
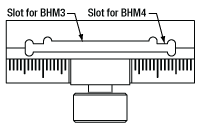
Click for Details
BHMA1 Mechanical Drawing
Constructed from durable black Delrin, this bracket contains a built-in spirit level (bubble level) for consistent leveling of the mounted part. When the bubble is centered between the two graduations the bracket is level. When the center of the bubble is under one of the graduations then the bracket is rotated by 31 arcminutes.
Laser engraved 1.0 mm spaced graduations are also included on three sides of the bracket. These markings can be used to indicate how far the mounted part has been translated horizontally or to repeatably add a ruler or viewing card into the setup.
A through slot in the top of the bracket, shown in the drawing to the left, is shaped to fit over the top of the BHM3 and BHM4 rulers. Once fitted the bracket is free to translate vertically across the ruler. From here a second ruler or a viewing card is placed in the space between the first ruler and the front of the bracket. Everything is held in place by applying pressure using the thumbscrew on the front of the bracket.
Please Note: These brackets are created from Delrin and are not rated for laser safety.
*Delrin® is a registered trademark of DuPont Polymers, Inc.