Pigtailed Laser Diode Mount
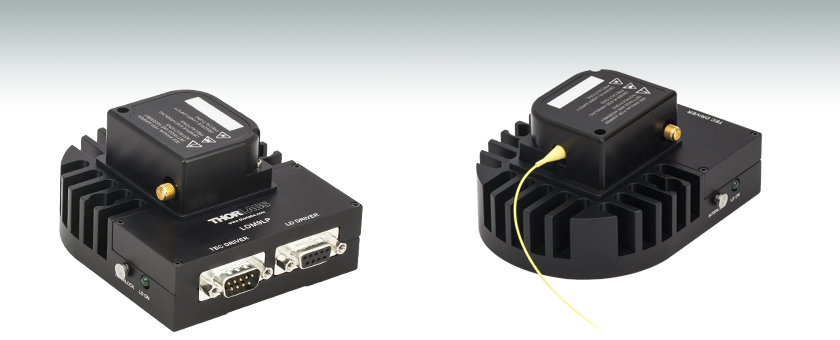
- Mounts Thorlabs’ Pigtailed LDs
- Compact Housing Protects Pigtail
- Integrated Thermistor and TEC
LDM9LP
Application Idea
LDM9LP with Mounted
Pigtail Laser Diode

Please Wait
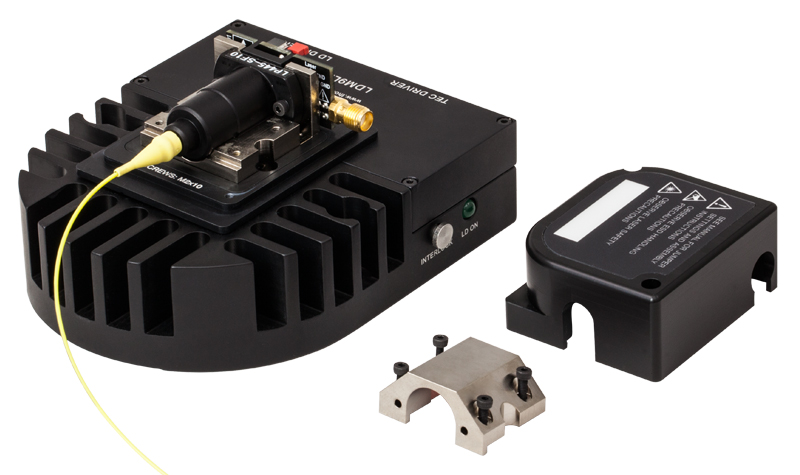
Click to Enlarge
Figure 1.1 The LDM9LP with Mounted Pigtailed LD and the Cover and Clamshell Removed
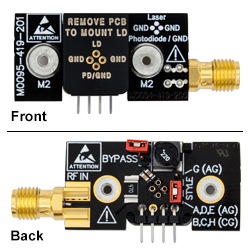
Click to Enlarge
Figure 1.3 Front (Top) and Back (Bottom) Images of the LDM9LP Circuit Board
Features
- Designed for Thorlabs' SM, PM, MM, and DFB Pigtailed Laser Diodesa (Ø5.6 or Ø9 mm, 3 or 4 Pin)
- Supports A, B, C, D, E, G, and H Pin Configurations
- TEC Element Prolongs LD Life and Stabilizes Output Power & Wavelength
- Clamshell Design Eliminates Thermal Gradients Across Diode
- Bias-T Adapter for RF Modulation of Laser Current >200 kHz
Thorlabs' LDM9LP is an LD and TEC mount designed for use with our 3- and 4-pin pigtailed diodesa. The compact housing protects the pigtail from physical damage, while also offering excellent thermal characteristics. When operating a pigtailed laser diode, temperature control is highly recommended to stabilize the laser's power and wavelength, while also prolonging the life of the laser. Typical laser diode mounts rely on contact between the diode and the mount's cold plate for heat transfer. Pigtailed laser diodes are often recessed in the pigtail's housing, offering poor contact with the cold plate of standard laser diode mounts. The LDM9LP, however, is specifically designed for operating pigtailed laser diodes. Its clamshell design reduces thermal gradients across the diode, while its cold block cradles the pigtail housing for excellent contact and heat transfer. Performance can be further improved by using thermal grease around the pigtail package within the clamshell.
The LDM9LP allows the user to quickly and easily install or remove pigtail diodes from the mount. The back of the circuit board contains a jumper for selecting the appropriate pin configuration of the laser diode (see Figure 1.3). The jumper is labeled with the compatible pin codes for easy reference. Before installing the pigtailed LD, ensure that the jumper is set correctly. Additionally, the front for the circuit board is labeled with a pinout for the socket to help orient the laser diode correctly before mounting (see Mounting Instruction tab for more detail).
Two 1/4" through holes can be used for securing the mount to an optical table with 1/4"-20 or M6 cap screws. It is highly recommended prior to mounting the diode that users verify the diode pin configuration to ensure the laser diode drive pin is secured in the correct socket. Both the inside of the cover and the front of the circuit board contain the pinout for the socket.
DB9 connections interface with all of Thorlabs' LD Current Controllers and TEC Controllers. An RF SMA connector allows access to a Bias-T circuit for RF modulation of the laser's drive current (>200 kHz). For modulation below 200 kHz, current should be modulated through the laser diode controller. A remote interlock jack is provided for the connection of safety devices such as shutters and warning signs.
a. Due to the variety of fiber pigtailed laser diode packages offered by other companies, this mount is only designed for use with Thorlabs products. The mount can also be used with our VHG-stabilized pigtailed laser diode without the protective cover installed; this should not affect diode performance. Thorlabs offers a laser diode pigtailing service; please contact Tech Support for details.
LDM9LP Specifications | |
---|---|
Laser Diode Package | Thorlabs' SM, PM, MM, and DFB Pigtailed Laser Diodes (Ø5.6 or Ø9 mm, 3 or 4 Pin) |
Supported Pin Configurations | A, B, C, D, E, G, & H |
Laser Current (Max) | 1 A |
Laser Diode Polarity | Selectable |
Monitor Diode Polarity | Selectable |
LD Interface | DB9, Female |
RF Power (Max) | 500 mW |
RF Input Impedance | 50 Ω |
Modulation Frequency (Bias-T) | >200 kHz |
RF Input Connector | SMA |
TEC Current (Max) | 4.5 A |
TEC Voltage (Max) | 3.0 V |
TEC Heating/ Cooling Capacity | 7 W (Mounted to a 12" × 12" Breadboard) |
TEC Interface | DB9, Male |
Temperature Sensor | 10 kΩ Thermistor, ±1% at 25°C, β = 3988 |
Typical Temperature Range (LD Dependent) | 0 to 70 °C -10 to 70 °C (Mounted to a 12" × 12" Breadboard) |
Remote Interlock | 2.5 mm Phono Jack |
Dimensions (L × W × H) | 4.48" × 3.5" × 2.1" (113.8 mm × 88.9 mm × 53.3 mm) |
Figure 2.1 A list of the supported pin configurations can be found on the underside of the LDM9LP's cover.
Settings for Supported Laser Diode Pin Types
The LDM9LP is compatible with A, B, C, D, E, and G pin configurations. Figure 2.2 illustrates how each pin code should be aligned with the socket on the laser mounting PCB. Two jumper pins, shown in Figure 2.3, also need to be set. Settings are outlined in Tables 2.4 and 2.5. The BYPASS jumper should be set only if the laser is modulated via the LD Driver input.
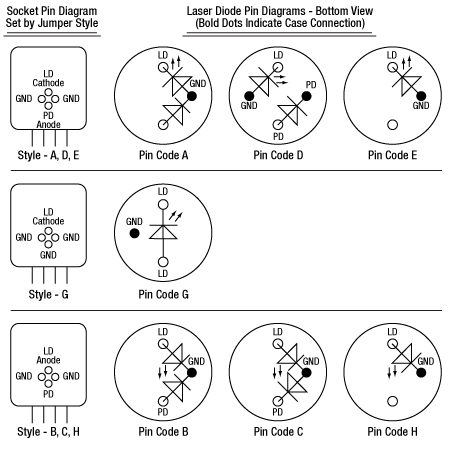
Click to Enlarge
Figure 2.2 The pin diagrams above show how the laser diode pins should align with the socket on the laser mounting PCB.
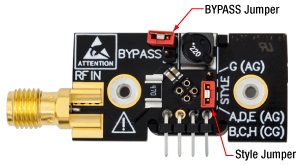
Click to Enlarge
Figure 2.3 The image shows the locations of the STYLE and BYPASS jumper pins. The STYLE jumper pin needs to be set for the pin style of the laser diode in use. The BYPASS jumper should only be set if the laser is modulated via the LD Driver input. Settings are outlined in Tables 2.4 and 2.5.
Table 2.4 STYLE Jumper | |
---|---|
Laser Diode Pin | Jumper Position |
A, B, C, D, E, or H | Lower 2 Pins |
G | Upper 2 Pins |
Table 2.5 BYPASS Jumpera | |
---|---|
Operation Mode | Jumper Position |
Low Noise, No Modulation | Removed |
RF Modulation via RF IN (BIAS-T) | Removed |
Modulation via LD Driver Inputb | Set |
Laser Diode Connector
D-type Female
Pin # | Signal |
---|---|
1 | Interlock and Status Pin (LDC Specific) |
2 | Photodiode Cathode |
3 | Laser Ground (Case) |
4 | Photodiode Anode |
5 | Interlock and Status Return |
6 | Laser Diode Voltage (-) |
7 | Laser Diode Cathode |
8 | Laser Diode Anode |
9 | Laser Diode Voltage (+) |
TEC Connector
D-type Male
Pin # | Signal |
---|---|
1 | TEC Lockout (+) |
2 | +Thermistor |
3 | -Thermistor |
4 | +TEC |
5 | -TEC and TEC Lockout (-) |
6 | Not Connected |
7 | Not Connected |
8 | Not Connected |
9 | Not Connected |
Laser Diode Socket
G - Ground
LD - Laser Diode Pin
PD - Photodiode Pin
RF Modulation
SMA Female
This is a 50 Ω input that is AC-coupled directly to the laser through the Bias-T network for modulation frequencies >200 kHz.
Click to Enlarge
The graph above shows the RF modulation response of the LDM9LP when modulated through an external controller. The LDC202C benchtop LD current controller was used to produce the data shown above.
Click to Enlarge
The graph above shows the RF modulation response of the LDM9LP when modulated through the onboard Bias-T SMA input.
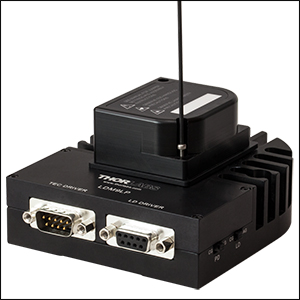
Click to Enlarge
Step 1: Using a 1.5 mm hex key (included with mount) or balldriver, remove the screws from the cover.
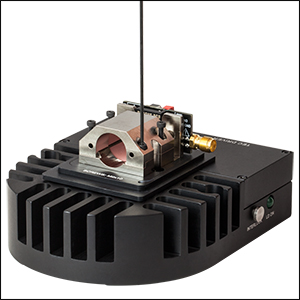
Click to Enlarge
Step 2: Using a 1.5 mm balldriver or hex key, remove the four screws securing the clamshell.
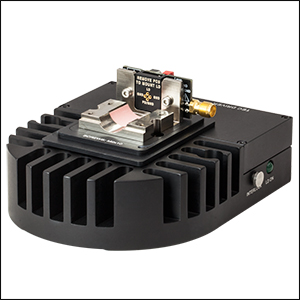
Click to Enlarge
Step 3: Finally, remove the two 1.5 mm hex screws that secure the circuit board.
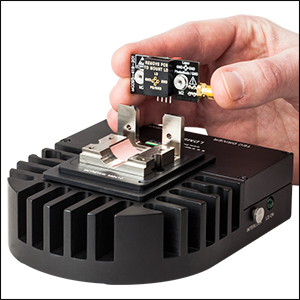
Click to Enlarge
Step 4: Gently pull the circuit board up, removing it from its socket. Before mounting a laser diode to the board, ensure that the jumpers on the back have been correctly set (see the Specs tab for more information).
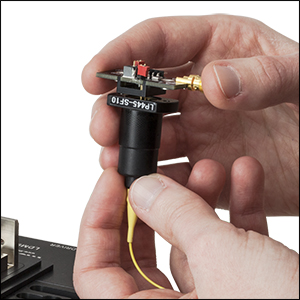
Click to Enlarge
Step 5: Install the LD into the socket, using the pinout on the circuit board to correctly align the LD's pins (see the pin configuration diagram on the Specs tab). Be sure to use a grounding strap (such as the WS01 or WS02) whenever handling LDs.
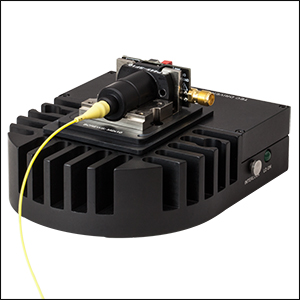
Click to Enlarge
Step 6: With the diode mounted, carfully plug the circuit board back into its socket. When firmly seated, secure with the two hex screws removed in step 3.
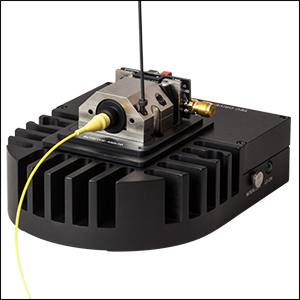
Click to Enlarge
Step 7: Replace all four screws removed in step 2. Be sure to snug up all the screws to ensure proper thermal contact.
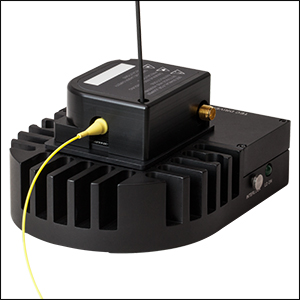
Click to Enlarge
Step 8: Replace the screws holding the cover onto the mount.
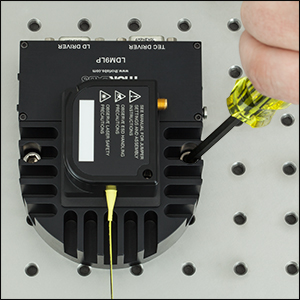
Click to Enlarge
Step 9: Finally, secure the LDM9LP to a breadboard or optical table with 2 1/4"-20 (M6) cap screws.
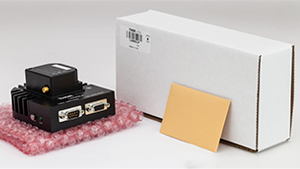
Click to Enlarge
Figure 6.1 LDM9LP Packaging
Item # | % Weight Reduction |
CO2-Equivalent Reductiona |
---|---|---|
LDM9LP | 14.71% | 5.26 kg |
Smart Pack
- Reduce Weight of Packaging Materials
- Increase Usage of Recyclable Packing Materials
- Improve Packing Integrity
- Decrease Shipping Costs
Thorlabs' Smart Pack Initiative is aimed at waste minimization while still maintaining adequate protection for our products. By eliminating any unnecessary packaging, implementing packaging design changes, and utilizing eco-friendly packaging materials for our customers when possible, this initiative seeks to improve the environmental impact of our product packaging. Products listed above are now shipped in re-engineered packaging that minimizes the weight and the use of non-recyclable materials.b As we move through our product line, we will indicate re-engineered packages with our Smart Pack logo.
Posted Comments: | |
Tielyr Creason
 (posted 2025-01-07 09:12:20.297) I had a lot of help on deciding on this system with support from the thorlabs technical support agent Bijoya Mandal. jpolaris
 (posted 2025-01-08 05:09:13.0) Thank you for taking the time to leave a positive comment about the support you received from Bijoya. Salem Hegazy
 (posted 2023-05-25 07:32:06.94) I purchased the units:
- Mount: LDM9LP
- LD: LP785-SAV50
- LD Controller: LDC205C
However, I have no TEC controller. Please let me know if it is OK to operate this system without the TEC controller. (Or this will damage the LD). In other words, is there a problem (or what are the disadvantages) for not using TEC controller?
Also, If it is OK to operate the system without TEC, is there any JMPR to be plugged/unplugged in the purchased unit, or just let it as it is. cdolbashian
 (posted 2023-06-01 02:14:10.0) Good afternoon Salem. While a TEC element/controller is not strictly necessary to use when using such a laser package, it is greatly encouraged. Excessive heat in the package is one of the easiest and fastest ways to reduce the lifetime of your laser element. I have contacted you directly with more information. Eloy Montesinos
 (posted 2023-04-27 12:40:53.103) Hello
I'm trying to use this mount (LDM9LP) with the LPSC-1550-FC laser, connected to a third party controller (ILX LightWave LDC-3742 B). I have made a cable to interface according the manual, and still not working, the controller launch a "Open Circuit" alert.
The connections and configurations have been checked and everything is in order. The factory Interlock is installed and the resistor is properly computed and connected, so the status LD is ON state.
What could be the error?
Do you have a detailed scheme of the circuit in the Interlock Pins? ksosnowski
 (posted 2023-05-01 09:32:09.0) Thanks for reaching out to Thorlabs. The LDM9LP's Status LED is powered from the interlock line of the connected laser controller, so this implies the Open Circuit error might result directly from an improper connection or setting on the mount or laser controller. When the laser connection is open, the constant current driver attempts to ramp up voltage to meet the setpoint, but due to high resistance, may hits the driver compliance voltage limit first. Wrong polarity of diodes may result in this error as well, and reversing laser polarity can break the diode. Most controllers, have a separate error message for interlock related events, as described in their device manuals. I have reached out directly to discuss this issue further. Adriana Riofrio
 (posted 2021-07-24 23:19:14.763) Good evening, we have purchased the LDM9LP but we want to use a controller from another manufacturer (arroyo instruments). We have worked out the current and temperature control wire but we have a 501 message related to the interlock. The 2.5 mm Mono Phono Jack did not come to us, is it necessary to connect it with an external voltage source at 5V? Could you tell me how the circuit should look?
I appreciate your response cdolbashian
 (posted 2021-08-19 01:57:47.0) Thank you for contacting us here at Thorlabs! It seems like you are simply missing the interlock pin for your device. I have reached out to you directly to resolve this. Chad Bender
 (posted 2020-08-27 16:48:43.677) I am trying to bring back into service an old ITC502 controller. The pinout for the controller LD Driver DB9 appears to match the current pinout for the LDM9LP. However, the TEC has clearly changed in the past decade (controller has a DB15). Does Thorlabs provide a cable that can connect these devices, or will I need to fabricate a custom cable? I can certainly do that - would just prefer to save time if I can buy an COTS cable. MKiess
 (posted 2020-08-31 06:55:16.0) Hello Chad, thank you for your inquiry.
The cables that came with the ITC502 are also compatible with the LDM0LP.
The pin configurations of the newer controllers are the same as the ITC502. The matching cables would be the CAB400 for the laser controller and the CAB420-15 for the temperature controller. These cables are still available on our website. Hosung Byun
 (posted 2020-05-30 01:31:28.05) Hello, Thorlab!
This is Hosung Byun, graduated student at Seoul National University in Korea.
I bought 'LDM9LP Mount' to operate 'LP635-SF8' diode laser.
And I try to use LDC220C & TED200C for drivers, which are fully functional to LDM56/M.
But I found that TED200C can not detect the sensor, indicating 'no sensor', while LDC220C works.
So I want to know whether TED200C is not compatible to LDM9LP, although it is written "All Thorlabs TED series temperature controllers" in manual.
If not, let me know expected reasons for this and solutions,
or I would like to exchange it.
Thank you.
Kind regards,
Hosung Byun. asundararaj
 (posted 2020-06-01 03:04:56.0) Thank you for contacting Thorlabs. The TED200C is compatible with the LDM9LP. Typically, the "NO SENSOR" message would indicate that the temperature sensor is incorrectly selected or not connected. The temperature sensor in the LDM9LP is a 10 kΩ Thermistor. I have contacted you directly to assist further. Hugh Wilson
 (posted 2019-04-03 22:09:52.347) Hello,
I would like to ask about the pink/grey pads of material placed in the inside of the clamshell of the LDM9LP (visible in step 3 of the mounting instructions: https://www.thorlabs.com/newgrouppage9.cfm?objectgroup_id=4839&pn=LDM9LP)
Do they have any function or should they be removed prior to applying thermal paste and mounting the diode?
Thank you very much for your help.
Best,
Hugh YLohia
 (posted 2019-04-08 03:09:19.0) Hello Hugh, thank you for contacting Thorlabs. This is a thermally conductive pad and is meant to maximize the thermal contact in place of thermal grease. It’s a bit cleaner to use than thermal grease since the connection is designed to be user-serviceable. That being said, you may remove the pad prior to applying thermal grease if it looks like your application produces a high heat load. Bernard Alunda
 (posted 2019-03-16 12:45:01.73) Hello,
I have a question regarding the laser diode mount LDM9LP. In chapter of the manual, section about RF modulation, what does the "Use the laser controller to establish the DC operating point of the laser"? I am using LDC501 to drive the laser. Please let me know. Thank you and hoping to hear from you soonest.
Warmest Regards,
Ben llamb
 (posted 2019-03-28 09:01:54.0) Hello Ben, thank you for your feedback. That sentence in the manual refers to establishing a center point around which you will be modulating, a point above the laser threshold value in most cases. I have reached out to you directly for any further clarification. jlow
 (posted 2012-08-03 16:47:00.0) Response from Jeremy at Thorlabs to Hazen: To mount the pigtail on this, one would set the pigtail down on the bottom copper plate first before slowly trying to get the pins to slide in (mostly done by feel). While this is do-able (but definitely not ideal), the steep viewing angle does make it quite difficult to mount our pigtail in an easy way, which means this would warrant a redesign of the mounting part. We would certainly welcome any additional feedback you are willing to share with us. I will let our engineering group know about this and get started on ideas on improving this mount. hbabcock
 (posted 2012-08-03 15:31:02.0) These work well once you manage to get your diode mounted. However in my experience getting your diode in position is a lot more difficult than one would hope. I have on several occasions managed to almost destroy the pins on the diode trying to get them lined up & inserted into the mounting socket. It might be easier if the brass/copper bottom plate was also removable so that you were not forced to come in at such a steep angle?
-Hazen Babcock |